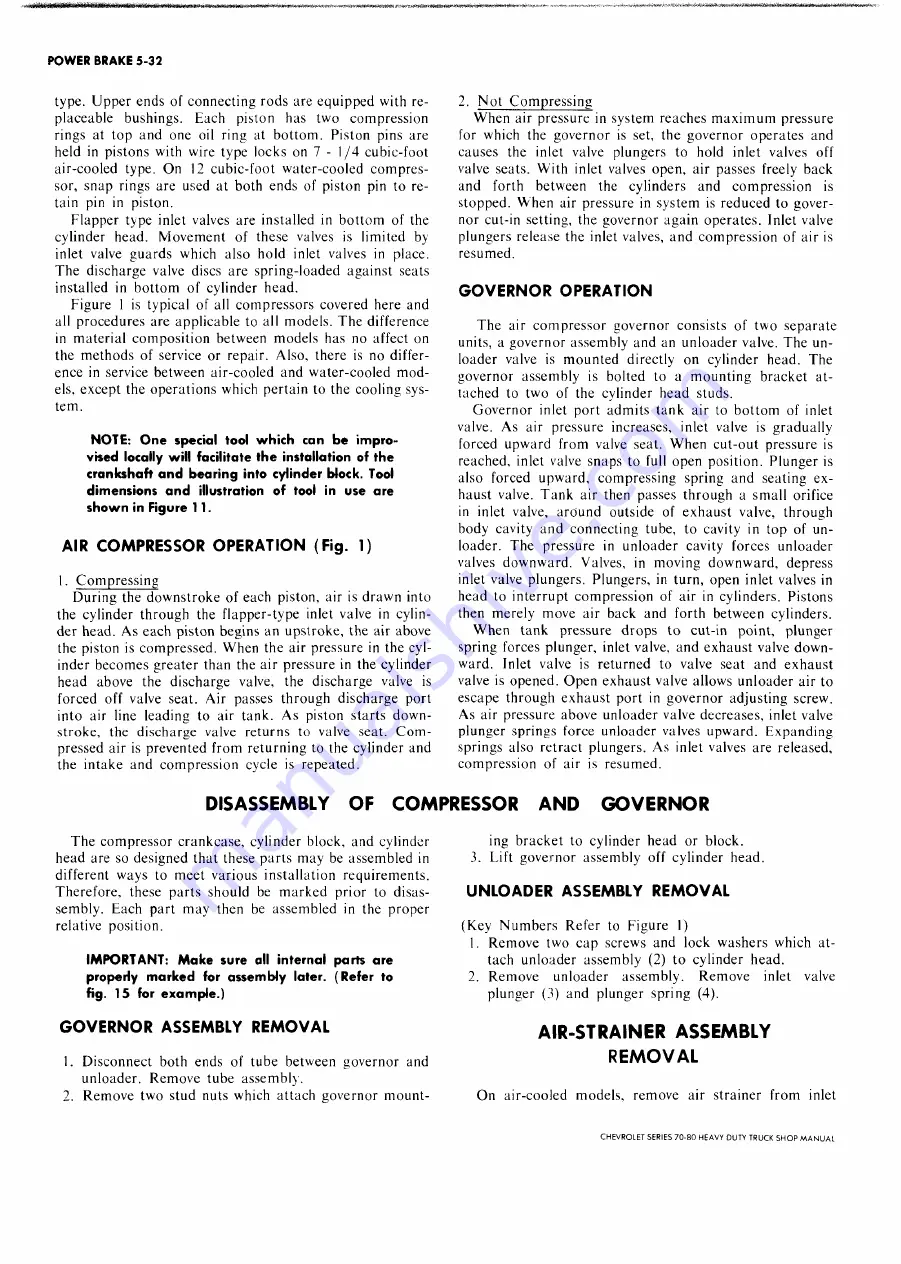
POWER BRAKE 5-32
type. U pper ends of connecting rods are equipped with re
placeable bushings. Each piston has two compression
rings at top and one oil ring at bottom . Piston pins are
held in pistons with wire type locks on 7 - 1/4 cubic-foot
air-cooled type. On 12 cubic-foot water-cooled com pres
sor, snap rings are used at both ends of piston pin to re
tain pin in piston.
Flapper type inlet valves are installed in bottom of the
cylinder head. M ovem ent of these valves is limited by
inlet valve guards which also hold inlet valves in place.
T he discharge valve discs are spring-loaded against seats
installed in bottom of cylinder head.
Figure 1 is typical of all com pressors covered here and
all procedures are applicable to all models. The difference
in m aterial com position between models has no affect on
the m ethods of service or repair. Also, there is no differ
ence in service between air-cooled and water-cooled m od
els, except the operations which pertain to the cooling sys
tem.
NOTE: One special tool which can be impro
vised locally will facilitate the installation of the
crankshaft and bearing into cylinder block. Tool
dimensions and illustration of tool in use are
shown in Figure 11.
AIR COMPRESSOR OPERATION (Fig. 1)
1. C om pressing
During the dow nstroke of each piston, air is draw n into
the cylinder through the flapper-type inlet valve in cylin
der head. As each piston begins an upstroke, the air above
the piston is compressed. W hen the air pressure in the cyl
inder becomes greater than the air pressure in the cylinder
head above the discharge valve, the discharge valve is
forced off valve seat. Air passes through discharge port
into air line leading to air tank. As piston starts dow n
stroke, the discharge valve returns to valve seat. C o m
pressed air is prevented from returning to the cylinder and
the intake and com pression cycle is repeated.
2. N o t C om pressing
W hen air pressure in system reaches m axim um pressure
for which the governor is set, the governor operates and
causes the inlet valve plungers to hold inlet valves off
valve seats. W ith inlet valves open, air passes freely back
and forth between the cylinders and com pression is
stopped. W hen air pressure in system is reduced to gover
nor cut-in setting, the governor again operates. Inlet valve
plungers release the inlet valves, and com pression of air is
resumed.
GOVERNOR OPERATION
The air com pressor governor consists of two separate
units, a governor assem bly and an unloader valve. The un
loader valve is m ounted directly on cylinder head. The
governor assem bly is bolted to a m ounting bracket at
tached to two of the cylinder head studs.
Governor inlet port adm its tank air to bottom of inlet
valve. As air pressure increases, inlet valve is gradually
forced upward from valve seat. W hen cut-out pressure is
reached, inlet valve snaps to full open position. Plunger is
also forced upw ard, com pressing spring and seating ex
haust valve. T ank air then passes through a sm all orifice
in inlet valve, around outside of exhaust valve, through
body cavity and connecting tube, to cavity in top of un
loader. The pressure in unloader cavity forces unloader
valves dow nward. Valves, in moving dow nw ard, depress
inlet valve plungers. Plungers, in turn, open inlet valves in
head to interrupt com pression of air in cylinders. Pistons
then merely move air back and forth between cylinders.
W hen tank pressure drops to cut-in point, plunger
spring forces plunger, inlet valve, and exhaust valve dow n
ward. Inlet valve is returned to valve seat and exhaust
valve is opened. Open exhaust valve allows unloader air to
escape through exhaust port in governor adjusting screw.
As air pressure above unloader valve decreases, inlet valve
plunger springs force unloader valves upw ard. Expanding
springs also retract plungers. As inlet valves are released,
compression of air is resumed.
DISASSEMBLY OF CO MPRESSOR A N D G O V ERN O R
The com pressor crankcase, cylinder block, and cylinder
head are so designed that these parts m ay be assembled in
different ways to m eet various installation requirem ents.
Therefore, these parts should be m arked prior to disas
sembly. Each part m ay then be assem bled in the proper
relative position.
IMPORTANT: Make sure all internal parts are
properly marked for assembly later. (Refer to
fig. 15 for example.)
GOVERNOR ASSEMBLY REMOVAL
1. Disconnect both ends of tube between governor and
unloader. Rem ove tube assembly.
2. Rem ove two stud nuts which attach governor m ount
ing bracket to cylinder head or block.
3. Lift governor assembly off cylinder head.
UNLOADER ASSEMBLY REMOVAL
(Key N um bers Refer to Figure 1)
1. Remove two cap screws and lock washers which at
tach unloader assembly (2) to cylinder head.
2. Remove unloader assembly. Rem ove inlet valve
plunger (3) and plunger spring (4).
AIR-STRAINER ASSEMBLY
REMOVAL
O n air-cooled models, remove air strainer from inlet
CHEVROLET SERIES 70-80 HEAVY DUTY TRUCK SH O P M A N U A L
Summary of Contents for 70 1969 Series
Page 1: ...CHEVROLET HEAVY DUTY TRUCK SHOP MANUAL...
Page 3: ......
Page 11: ...LUBRICATION 0 4 CHEVROLET SERIES 70 80 HEAVY DUTY TRUCK SHOP MANUAL...
Page 27: ......
Page 119: ......
Page 361: ......
Page 371: ......
Page 427: ......
Page 443: ......
Page 451: ......
Page 493: ......
Page 499: ......
Page 549: ......
Page 555: ......
Page 609: ......
Page 715: ...am...
Page 745: ......
Page 910: ......
Page 913: ......