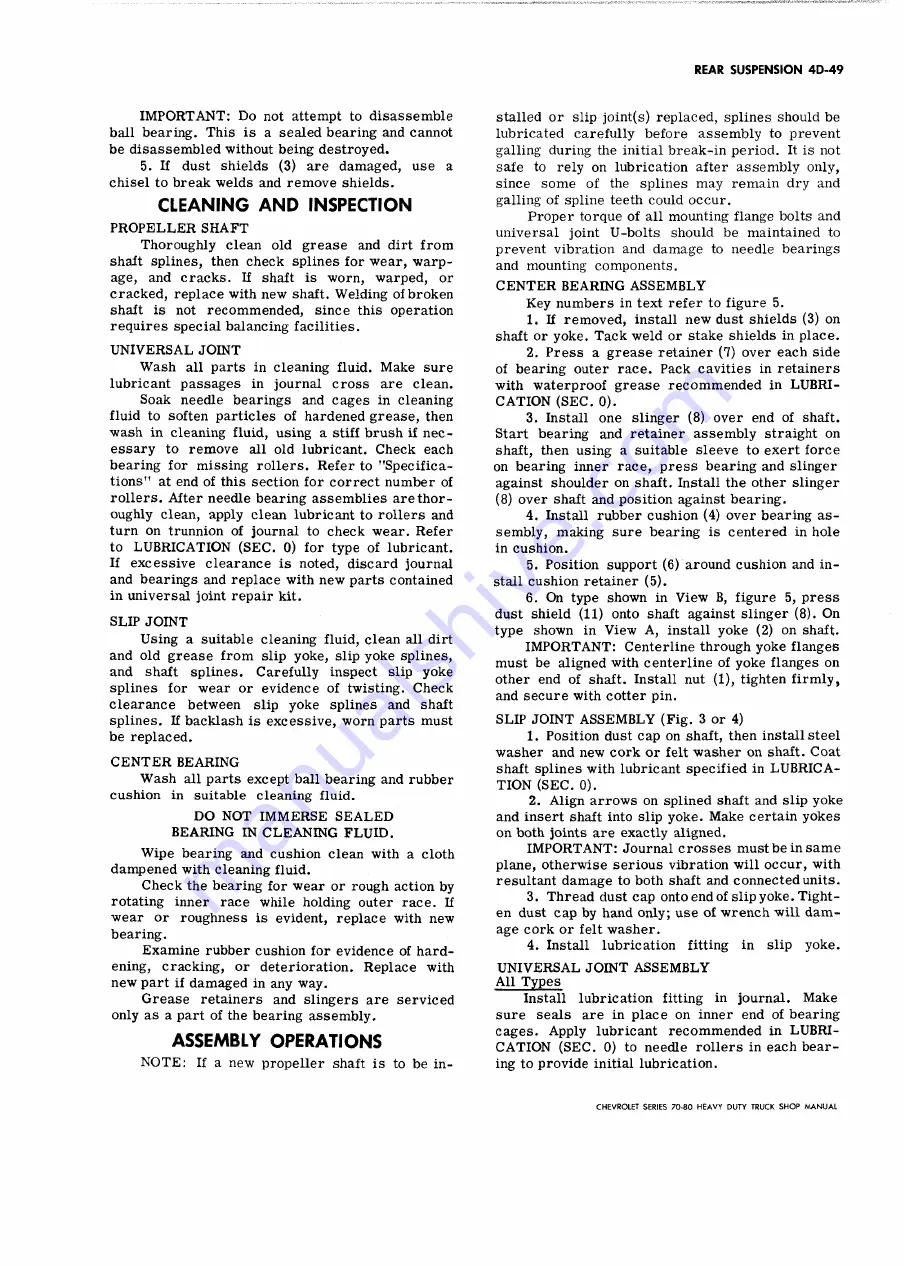
REAR SUSPENSION 4D-49
IM P O R T A N T : Do not attempt to disassemble
ball bearing. This is a sealed bearing and cannot
be disassembled without being destroyed.
5.
If dust shields (3) are damaged, use a
chisel to break welds and remove shields.
CLEANING A N D INSPECTION
P R O P E L L E R S H A F T
Thoroughly clean old grease and dirt from
shaft splines, then check splines for wear, warp-
age, and cracks. If shaft is worn, warped, or
cracked, replace with new shaft. Welding of broken
shaft is not recommended, since this operation
requires special balancing facilities.
U N IV E R S A L JOIN T
Wash all parts in cleaning fluid. Make sure
lubricant passages in journal cross are clean.
Soak needle bearings and cages in cleaning
fluid to soften particles of hardened grease, then
wash in cleaning fluid, using a stiff brush if nec
essary to remove all old lubricant. Check each
bearing for missing rollers. Refer to "Specifica
tions" at end of this section for correct number of
rollers. After needle bearing assemblies are thor
oughly clean, apply clean lubricant to rollers and
turn on trunnion of journal to check wear. Refer
to LU BR ICA TION (SEC. 0) for type of lubricant.
If excessive clearance is noted, discard journal
and bearings and replace with new parts contained
in universal joint repair kit.
SLIP JO IN T
Using a suitable cleaning fluid, clean all dirt
and old grease from slip yoke, slip yoke splines,
and shaft splines. Carefully inspect slip yoke
splines for wear or evidence of twisting. Check
clearance between slip yoke splines and shaft
splines. If backlash is excessive, worn parts must
be replaced.
C E N T E R BEARING
W ash all parts except ball bearing and rubber
cushion in suitable cleaning fluid.
D O N O T IM M E R S E S E A L E D
BEARING IN C L E A N IN G F L U ID .
Wipe bearing and cushion clean with a cloth
dampened with cleaning fluid.
Check the bearing for wear or rough action by
rotating inner race while holding outer race. If
wear or roughness is evident, replace with new
bearing.
Examine rubber cushion for evidence of hard
ening, cracking, or deterioration. Replace with
new part if damaged in any way.
Grease retainers and slingers are serviced
only as a part of the bearing assembly.
ASSEMBLY OPERATIONS
N O T E : If a new propeller shaft is to be in
stalled or slip joint(s) replaced, splines should be
lubricated carefully before assembly to prevent
galling during the initial break-in period. It is not
safe to rely on lubrication after assembly only,
since some of the splines may remain dry and
galling of spline teeth could occur.
Proper torque of all mounting flange bolts and
universal joint U-bolts should be maintained to
prevent vibration and damage to needle bearings
and mounting components.
C E N T E R BEARIN G A S S E M B L Y
Key numbers in text refer to figure 5.
1. If removed, install new dust shields (3) on
shaft or yoke. Tack weld or stake shields in place.
2. Press a grease retainer (7) over each side
of bearing outer race. Pack cavities in retainers
with waterproof grease recommended in LUBRI
C A T IO N (SEC. 0).
3. Install one slinger (8) over end of shaft.
Start bearing and retainer assembly straight on
shaft, then using a suitable sleeve to exert force
on bearing inner race, press bearing and slinger
against shoulder on shaft. Install the other slinger
(8) over shaft and position against bearing.
4. Install rubber cushion (4) over bearing as
sembly, making sure bearing is centered in hole
in cushion.
5. Position support (6) around cushion and in
stall cushion retainer (5).
6 . On type shown in View B, figure 5, press
dust shield (11) onto shaft against slinger (8). On
type shown in View A, install yoke (2) on shaft.
IM P O R T A N T : Centerline through yoke flanges
must be aligned with centerline of yoke flanges on
other end of shaft. Install nut (1), tighten firmly,
and secure with cotter pin.
SLIP JO IN T A S S E M B L Y (Fig. 3 or 4)
1. Position dust cap on shaft, then install steel
washer and new cork or felt washer on shaft. Coat
shaft splines with lubricant specified in LU B R IC A
TIO N (SEC. 0).
2. Align arrows on splined shaft and slip yoke
and insert shaft into slip yoke. Make certain yokes
on both joints are exactly aligned.
IM P O R T A N T : Journal crosses must be in same
plane, otherwise serious vibration will occur, with
resultant damage to both shaft and connected units.
3. Thread dust cap onto end of slip yoke. Tight
en dust cap by hand only; use of wrench will dam
age cork or felt washer.
4. Install lubrication fitting in slip yoke.
U N IV E R S A L JO IN T A S S E M B L Y
All Types
Install lubrication fitting in journal. Make
sure seals are in place on inner end of bearing
cages. Apply lubricant recommended in LUBRI
C A T IO N (SEC. 0) to needle rollers in each bear
ing to provide initial lubrication.
CHEVROLET SERIES 70-80 H EAVY DUTY TRUCK SH O P M A N U A L
Summary of Contents for 70 1969 Series
Page 1: ...CHEVROLET HEAVY DUTY TRUCK SHOP MANUAL...
Page 3: ......
Page 11: ...LUBRICATION 0 4 CHEVROLET SERIES 70 80 HEAVY DUTY TRUCK SHOP MANUAL...
Page 27: ......
Page 119: ......
Page 361: ......
Page 371: ......
Page 427: ......
Page 443: ......
Page 451: ......
Page 493: ......
Page 499: ......
Page 549: ......
Page 555: ......
Page 609: ......
Page 715: ...am...
Page 745: ......
Page 910: ......
Page 913: ......