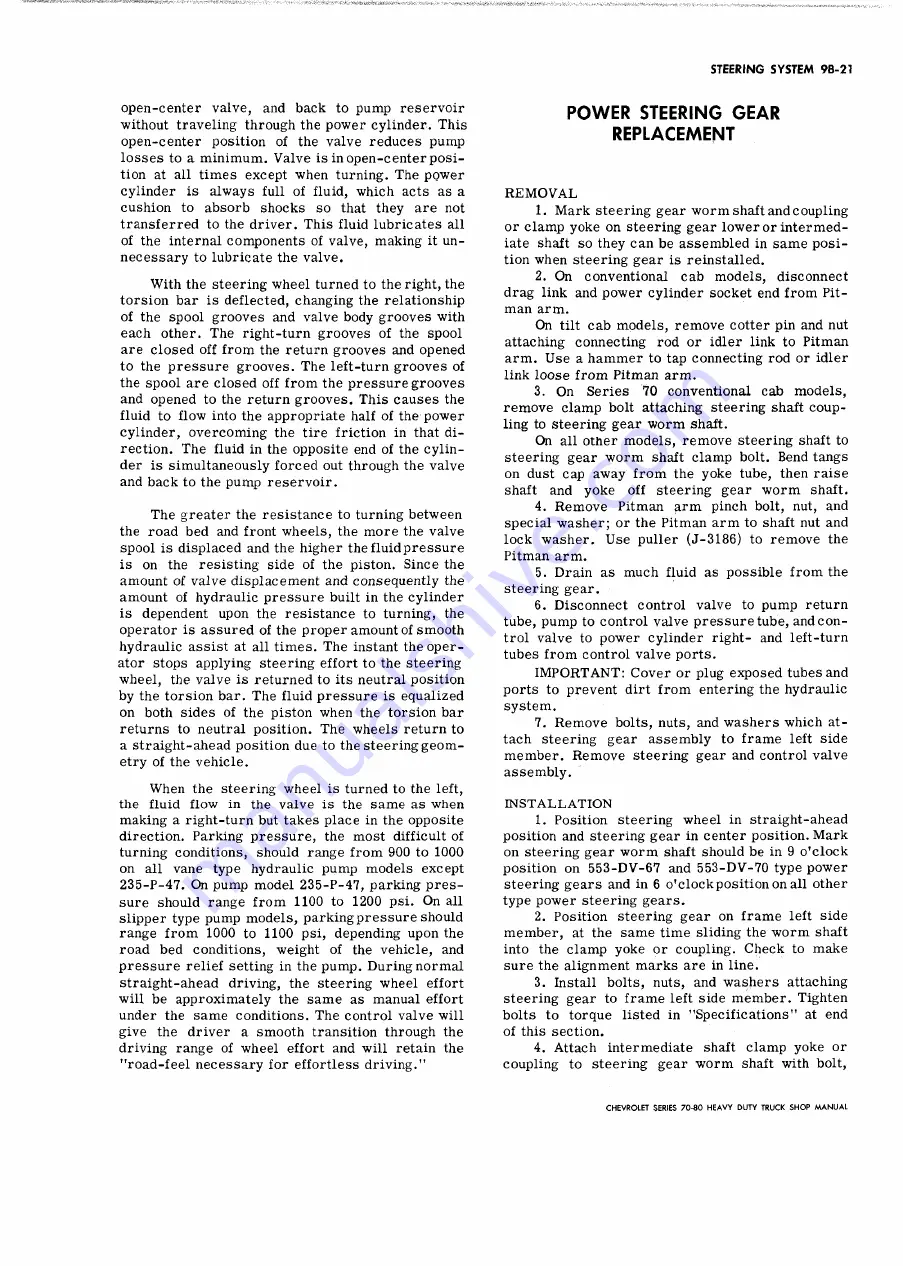
STEERING SYSTEM 9B-21
open-center valve, and back to pump reservoir
without traveling through the power cylinder. This
open-center position of the valve reduces pump
losses to a minimum. Valve is in open-center posi
tion at all times except when turning. The power
cylinder is always full of fluid, which acts as a
cushion to absorb shocks so that they are not
transferred to the driver. This fluid lubricates all
of the internal components of valve, making it un
necessary to lubricate the valve.
With the steering wheel turned to the right, the
torsion bar is deflected, changing the relationship
of the spool grooves and valve body grooves with
each other. The right-turn grooves of the spool
are closed off from the return grooves and opened
to the pressure grooves. The left-turn grooves of
the spool are closed off from the pressure grooves
and opened to the return grooves. This causes the
fluid to flow into the appropriate half of the power
cylinder, overcoming the tire friction in that di
rection. The fluid in the opposite end of the cylin
der is simultaneously forced out through the valve
and back to the pump reservoir.
The greater the resistance to turning between
the road bed and front wheels, the more the valve
spool is displaced and the higher the fluid pressure
is on the resisting side of the piston. Since the
amount of valve displacement and consequently the
amount of hydraulic pressure built in the cylinder
is dependent upon the resistance to turning, the
operator is assured of the proper amount of smooth
hydraulic assist at all times. The instant the oper
ator stops applying steering effort to the steering
wheel, the valve is returned to its neutral position
by the torsion bar. The fluid pressure is equalized
on both sides of the piston when the torsion bar
returns to neutral position. The wheels return to
a straight-ahead position due to the steering geom
etry of the vehicle.
When the steering wheel is turned to the left,
the fluid flow in the valve is the same as when
making a right-turn but takes place in the opposite
direction. Parking pressure, the most difficult of
turning conditions, should range from 900 to 1000
on all vane type hydraulic pump models except
235-P-47. On pump model 235-P-47, parking pres
sure should range from 1100 to 1200 psi. On all
slipper type pump models, parking pressure should
range from 1000 to 1100 psi, depending upon the
road bed conditions, weight of the vehicle, and
pressure relief setting in the pump. During normal
straight-ahead driving, the steering wheel effort
will be approximately the same as manual effort
under the same conditions. The control valve will
give the driver a smooth transition through the
driving range of wheel effort and will retain the
"road-feel necessary for effortless driving."
POWER STEERING GEAR
REPLACEMENT
R E M O V A L
1. Mark steering gear worm shaft and coupling
or clamp yoke on steering gear lower or intermed
iate shaft so they can be assembled in same posi
tion when steering gear is reinstalled.
2. On conventional cab models, disconnect
drag link and power cylinder socket end from Pit
man arm.
On tilt cab models, remove cotter pin and nut
attaching connecting rod or idler link to Pitman
arm. Use a hammer to tap connecting rod or idler
link loose from Pitman arm.
3. On Series 70 conventional cab models,
remove clamp bolt attaching steering shaft coup
ling to steering gear worm shaft.
On all other models, remove steering shaft to
steering gear worm shaft clamp bolt. Bend tangs
on dust cap away from the yoke tube, then raise
shaft and yoke off steering gear worm shaft.
4. Remove Pitman arm pinch bolt, nut, and
special washer; or the Pitman arm to shaft nut and
lock washer. Use puller (J-3186) to remove the
Pitman arm.
5. Drain as much fluid as possible from the
steering gear.
6. Disconnect control valve to pump return
tube, pump to control valve pressure tube, and con
trol valve to power cylinder right- and left-turn
tubes from control valve ports.
IM P O R T A N T : Cover or plug exposed tubes and
ports to prevent dirt from entering the hydraulic
system.
7. Remove bolts, nuts, and washers which at
tach steering gear assembly to frame left side
member. Remove steering gear and control valve
assembly.
IN S T A L L A T IO N
1. Position steering wheel in straight-ahead
position and steering gear in center position. Mark
on steering gear worm shaft should be in 9 o'clock
position on 553-DV-67 and 553-DV-70 type power
steering gears and in 6 o'clockposition on all other
type power steering gears.
2. Position steering gear on frame left side
member, at the same time sliding the worm shaft
into the clamp yoke or coupling. Check to make
sure the alignment marks are in line.
3. Install bolts, nuts, and washers attaching
steering gear to frame left side member. Tighten
bolts to torque listed in "Specifications” at end
of this section.
4. Attach intermediate shaft clamp yoke or
coupling to steering gear worm shaft with bolt,
CHEVROLET SERIES 70 -80 H EAVY DUTY TRUCK SH O P M A N U A L
Summary of Contents for 70 1969 Series
Page 1: ...CHEVROLET HEAVY DUTY TRUCK SHOP MANUAL...
Page 3: ......
Page 11: ...LUBRICATION 0 4 CHEVROLET SERIES 70 80 HEAVY DUTY TRUCK SHOP MANUAL...
Page 27: ......
Page 119: ......
Page 361: ......
Page 371: ......
Page 427: ......
Page 443: ......
Page 451: ......
Page 493: ......
Page 499: ......
Page 549: ......
Page 555: ......
Page 609: ......
Page 715: ...am...
Page 745: ......
Page 910: ......
Page 913: ......