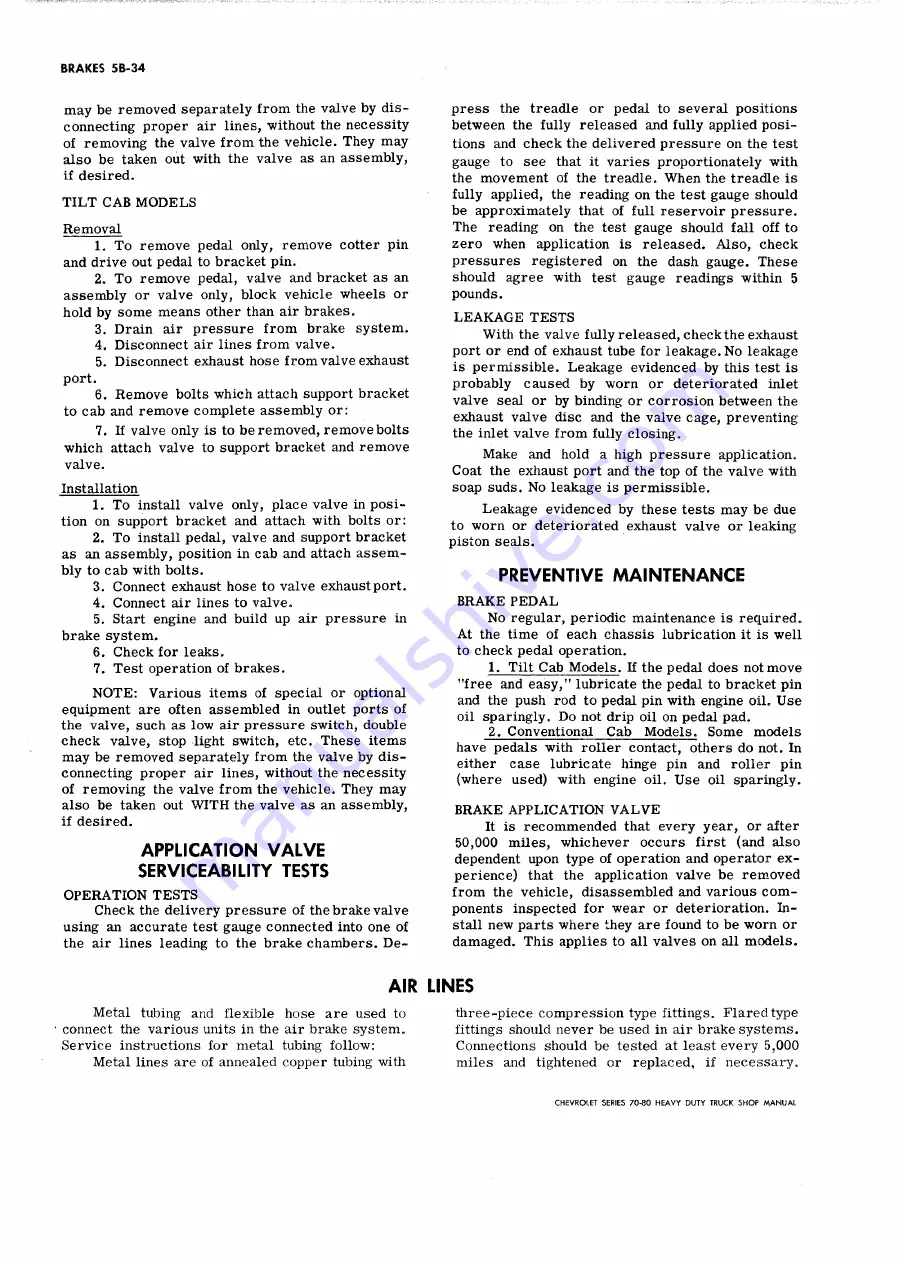
BRAKES 5B-34
may be removed separately from the valve by dis
connecting proper air lines, without the necessity
of removing the valve from the vehicle. They may
also be taken out with the valve as an assembly,
if desired.
T IL T CAB M O D E L S
Removal
1. To remove pedal only, remove cotter pin
and drive out pedal to bracket pin.
2. To remove pedal, valve and bracket as an
assembly or valve only, block vehicle wheels or
hold by some means other than air brakes.
3. Drain air pressure from brake system.
4. Disconnect air lines from valve.
5. Disconnect exhaust hose from valve exhaust
port.
6 . Remove bolts which attach support bracket
to cab and remove complete assembly or:
7. If valve only is to be removed, remove bolts
which attach valve to support bracket and remove
valve.
Installation
1. To install valve only, place valve in posi
tion on support bracket and attach with bolts or:
2. To install pedal, valve and support bracket
as an assembly, position in cab and attach assem
bly to cab with bolts.
3. Connect exhaust hose to valve exhaust port.
4. Connect air lines to valve.
5. Start engine and build up air pressure in
brake system.
6 . Check for leaks.
7. Test operation of brakes.
N O T E : Various items of special or optional
equipment are often assembled in outlet ports of
the valve, such as low air pressure switch, double
check valve, stop light switch, etc. These items
may be removed separately from the valve by dis
connecting proper air lines, without the necessity
of removing the valve from the vehicle. They may
also be taken out W IT H the valve as an assembly,
if desired.
APPLICATION VALVE
SERVICEABILITY TESTS
O P E R A T IO N T E ST S
Check the delivery pressure of the brake valve
using an accurate test gauge connected into one of
the air lines leading to the brake chambers. D e
press the treadle or pedal to several positions
between the fully released and fully applied posi
tions and check the delivered pressure on the test
gauge to see that it varies proportionately with
the movement of the treadle. When the treadle is
fully applied, the reading on the test gauge should
be approximately that of full reservoir pressure.
The reading on the test gauge should fall off to
zero when application is released. Also, check
pressures registered on the dash gauge. These
should agree with test gauge readings within 5
pounds.
L E A K A G E T ESTS
With the valve fully released, check the exhaust
port or end of exhaust tube for leakage. No leakage
is permissible. Leakage evidenced by this test is
probably caused by worn or deteriorated inlet
valve seal or by binding or corrosion between the
exhaust valve disc and the valve cage, preventing
the inlet valve from fully closing.
Make and hold a high pressure application.
Coat the exhaust port and the top of the valve with
soap suds. No leakage is permissible.
Leakage evidenced by these tests may be due
to worn or deteriorated exhaust valve or leaking
piston seals.
PREVENTIVE MAINTENANCE
B R A K E P E D A L
No regular, periodic maintenance is required.
At the time of each chassis lubrication it is well
to check pedal operation.
1. Tilt Cab Models. If the pedal does not move
"free and easy," lubricate the pedal to bracket pin
and the push rod to pedal pin with engine oil. Use
oil sparingly. Do not drip oil on pedal pad.
2. Conventional Cab Models. Some models
have pedals with roller contact, others do not. In
either case lubricate hinge pin and roller pin
(where used) with engine oil. Use oil sparingly.
B R A K E A PPLIC A TIO N V A L V E
It is recommended that every year, or after
50,000 miles, whichever occurs first (and also
dependent upon type of operation and operator ex
perience) that the application valve be removed
from the vehicle, disassembled and various com
ponents inspected for wear or deterioration. In
stall new parts where they are found to be worn or
damaged. This applies to all valves on all models.
AIR LINES
Metal tubing and flexible hose are used to
connect the various units in the air brake system.
Service instructions for metal tubing follow:
Metal lines are of annealed copper tubing with
three-piece compression type fittings. Flared type
fittings should never be used in air brake systems.
Connections should be tested at least every 5,000
miles and tightened or replaced, if necessary.
CHEVROLET SERIES 70-80 H EAVY DUTY TRUCK SH O P M A N U A L
Summary of Contents for 70 1969 Series
Page 1: ...CHEVROLET HEAVY DUTY TRUCK SHOP MANUAL...
Page 3: ......
Page 11: ...LUBRICATION 0 4 CHEVROLET SERIES 70 80 HEAVY DUTY TRUCK SHOP MANUAL...
Page 27: ......
Page 119: ......
Page 361: ......
Page 371: ......
Page 427: ......
Page 443: ......
Page 451: ......
Page 493: ......
Page 499: ......
Page 549: ......
Page 555: ......
Page 609: ......
Page 715: ...am...
Page 745: ......
Page 910: ......
Page 913: ......