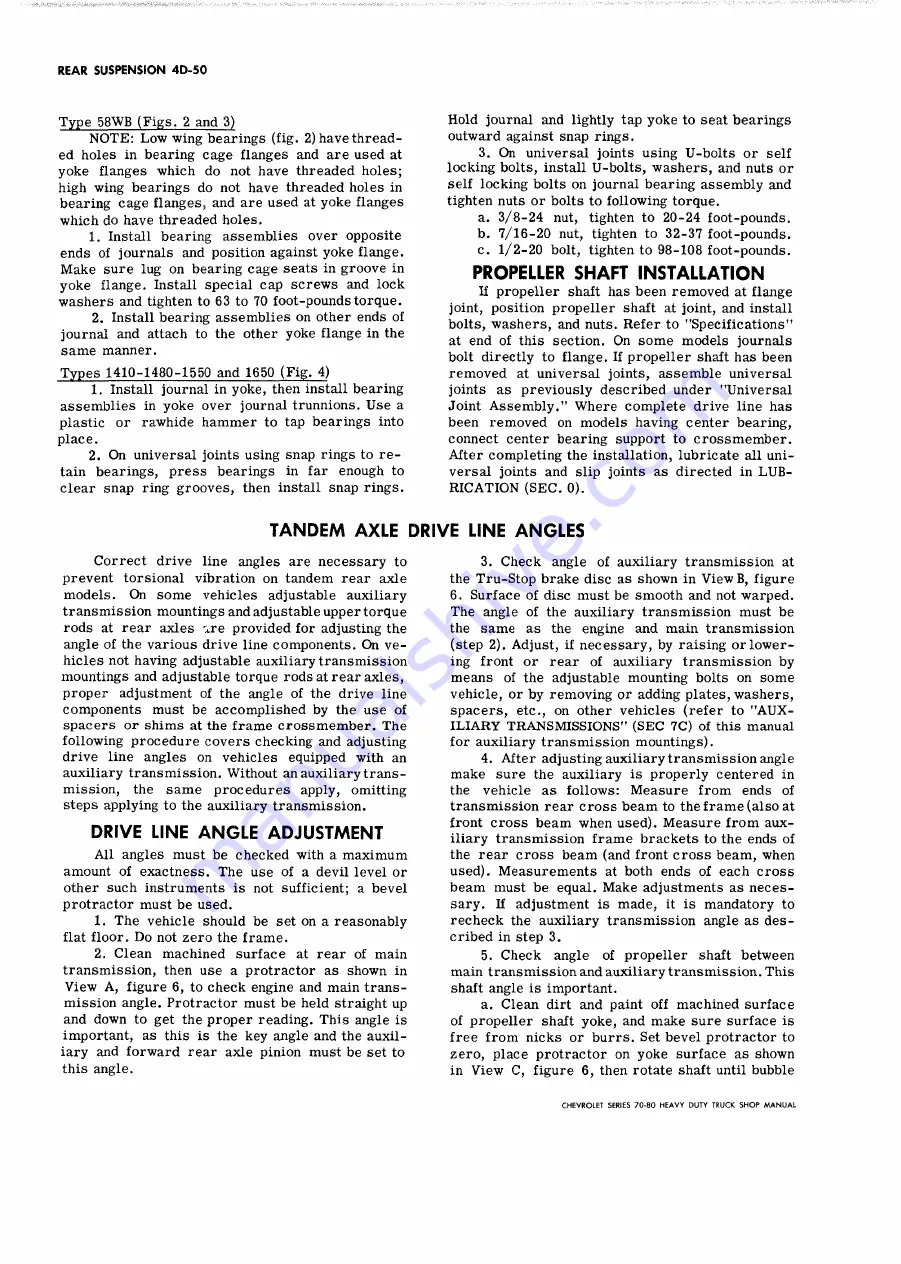
REAR SUSPENSION 4D-50
Type 58WB (Figs. 2 and 3)
N O T E : Low wing bearings (fig. 2) have thread
ed holes in bearing cage flanges and are used at
yoke flanges which do not have threaded holes;
high wing bearings do not have threaded holes in
bearing cage flanges, and are used at yoke flanges
which do have threaded holes.
1. Install bearing assemblies over opposite
ends of journals and position against yoke flange.
Make sure lug on bearing cage seats in groove in
yoke flange. Install special cap screws and lock
washers and tighten to 63 to 70 foot-pounds torque.
2. Install bearing assemblies on other ends of
journal and attach to the other yoke flange in the
same manner.
Types 1410-1480-1550 and 1650 (Fig. 4)
1. Install journal in yoke, then install bearing
assemblies in yoke over journal trunnions. Use a
plastic or rawhide hammer to tap bearings into
place.
2. On universal joints using snap rings to re
tain bearings, press bearings in far enough to
clear snap ring grooves, then install snap rings.
Hold journal and lightly tap yoke to seat bearings
outward against snap rings.
3.
On universal joints using U-bolts or self
locking bolts, install U-bolts, washers, and nuts or
self locking bolts on journal bearing assembly and
tighten nuts or bolts to following torque.
a. 3/8-24 nut, tighten to 20-24 foot-pounds.
b. 7/16-20 nut, tighten to 32-37 foot-pounds.
c. 1/2-20 bolt, tighten to 98-108 foot-pounds.
PROPELLER SHAFT INSTALLATION
If propeller shaft has been removed at flange
joint, position propeller shaft at joint, and install
bolts, washers, and nuts. Refer to "Specifications"
at end of this section. On some models journals
bolt directly to flange. If propeller shaft has been
removed at universal joints, assemble universal
joints as previously described under "Universal
Joint Assembly." Where complete drive line has
been removed on models having center bearing,
connect center bearing support to crossmember.
After completing the installation, lubricate all uni
versal joints and slip joints as directed in L U B
R ICA TIO N (SEC. 0).
TANDEM AXLE DRIVE LINE ANGLES
Correct drive line angles are necessary to
prevent torsional vibration on tandem rear axle
models. On some vehicles adjustable auxiliary
transmission mountings and adjustable upper torque
rods at rear axles ire provided for adjusting the
angle of the various drive line components. On ve
hicles not having adjustable auxiliary transmission
mountings and adjustable torque rods at rear axles,
proper adjustment of the angle of the drive line
components must be accomplished by the use of
spacers or shims at the frame crossmember. The
following procedure covers checking and adjusting
drive line angles on vehicles equipped with an
auxiliary transmission. Without an auxiliary trans
mission, the same procedures apply, omitting
steps applying to the auxiliary transmission.
DRIVE LINE ANGLE ADJUSTMENT
All angles must be checked with a maximum
amount of exactness. The use of a devil level or
other such instruments is not sufficient; a bevel
protractor must be used.
1. The vehicle should be set on a reasonably
flat floor. Do not zero the frame.
2. Clean machined surface at rear of main
transmission, then use a protractor as shown in
View A, figure 6, to check engine and main trans
mission angle. Protractor must be held straight up
and down to get the proper reading. This angle is
important, as this is the key angle and the auxil
iary and forward rear axle pinion must be set to
this angle.
3. Check angle of auxiliary transmission at
the Tru-Stop brake disc as shown in View B, figure
6 . Surface of disc must be smooth and not warped.
The angle of the auxiliary transmission must be
the same as the engine and main transmission
(step 2). Adjust, if necessary, by raising or lower
ing front or rear of auxiliary transmission by
means of the adjustable mounting bolts on some
vehicle, or by removing or adding plates, washers,
spacers, etc., on other vehicles (refer to " A U X
IL IA R Y TRAN SM ISSION S" (SEC 7C) of this manual
for auxiliary transmission mountings).
4. After adjusting auxiliary transmission angle
make sure the auxiliary is properly centered in
the vehicle as follows: Measure from ends of
transmission rear cross beam to the frame (also at
front cross beam when used). Measure from aux
iliary transmission frame brackets to the ends of
the rear cross beam (and front cross beam, when
used). Measurements at both ends of each cross
beam must be equal. Make adjustments as neces
sary. If adjustment is made, it is mandatory to
recheck the auxiliary transmission angle as des
cribed in step 3.
5. Check angle of propeller shaft between
main transmission and auxiliary transmission. This
shaft angle is important.
a.
Clean dirt and paint off machined surface
of propeller shaft yoke, and make sure surface is
free from nicks or burrs. Set bevel protractor to
zero, place protractor on yoke surface as shown
in View C, figure 6 , then rotate shaft until bubble
CHEVROLET SERIES 70-80 HEAVY DUTY TRUCK SH OP M ANUAL
Summary of Contents for 70 1969 Series
Page 1: ...CHEVROLET HEAVY DUTY TRUCK SHOP MANUAL...
Page 3: ......
Page 11: ...LUBRICATION 0 4 CHEVROLET SERIES 70 80 HEAVY DUTY TRUCK SHOP MANUAL...
Page 27: ......
Page 119: ......
Page 361: ......
Page 371: ......
Page 427: ......
Page 443: ......
Page 451: ......
Page 493: ......
Page 499: ......
Page 549: ......
Page 555: ......
Page 609: ......
Page 715: ...am...
Page 745: ......
Page 910: ......
Page 913: ......