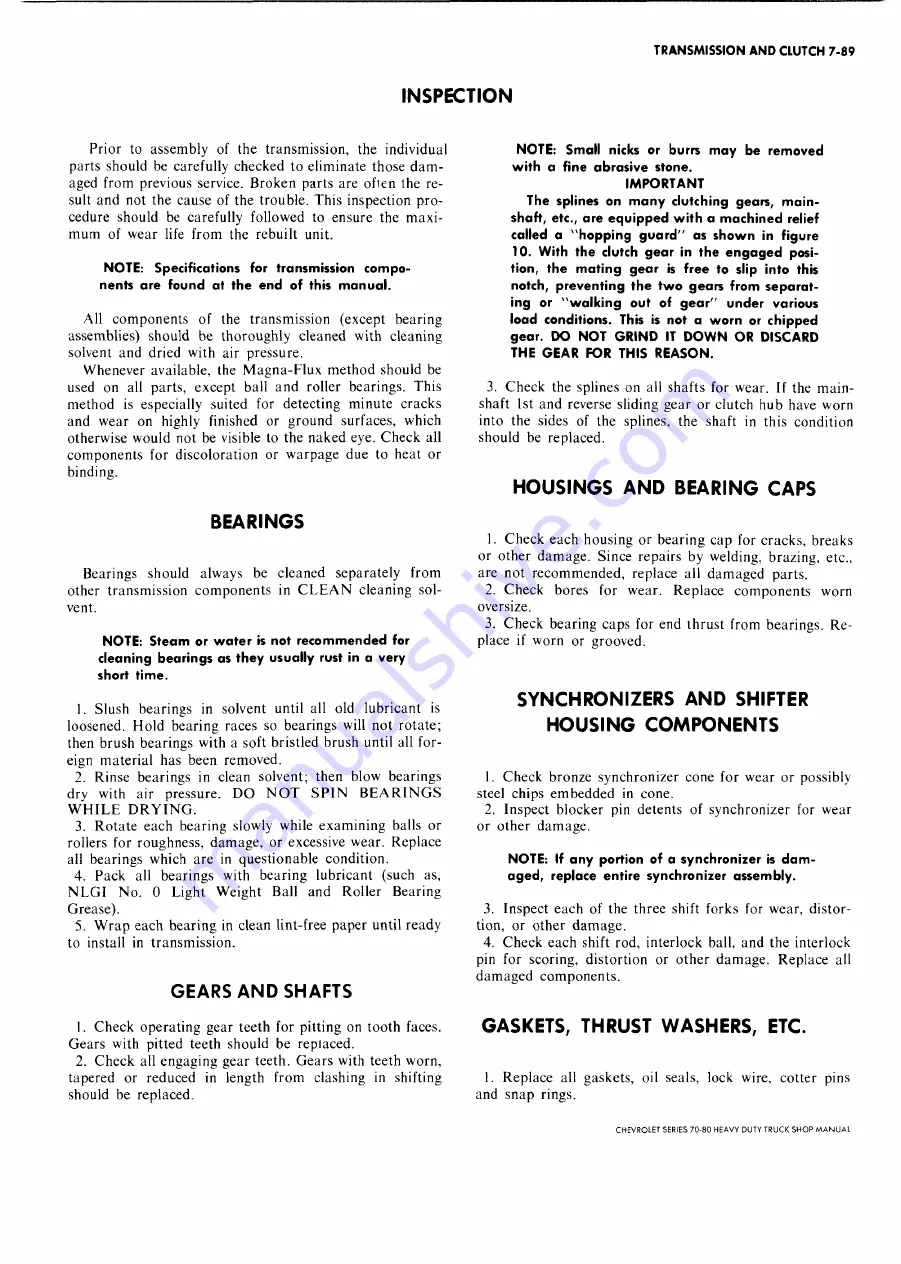
TRANSMISSION AND CLUTCH 7-89
INSPECTION
Prior to assem bly of the transm ission, the individual
parts should be carefully checked to elim inate those d a m
aged from previous service. B roken parts are ofien the re
sult and not the cause of the trouble. This inspection p ro
cedure should be carefully followed to ensure the m ax i
m um of wear life from the rebuilt unit.
N O T E : Specification s for tran sm issio n c o m p o
nents a re fo u n d at the e n d o f this m a n u a l.
All com ponents of the transm ission (except bearing
assemblies) should be thoroughly cleaned with cleaning
solvent and dried with air pressure.
W henever available, the M agna-F lux m ethod should be
used on all parts, except ball and roller bearings. This
m ethod is especially suited for detecting m inute cracks
and wear on highly finished or ground surfaces, which
otherwise would not be visible to the naked eye. C heck all
com ponents for discoloration or w arpage due to heat or
binding.
BEARINGS
Bearings should always be cleaned separately from
other transm ission com ponents in C L E A N cleaning sol
vent.
N O T E : S te a m or w a t e r is not re c o m m e n d e d for
c le a n in g b e a r in g s a s th e y u su a lly rust in a very
short tim e.
1. Slush bearings in solvent until all old lubricant is
loosened. H old bearing races so bearings will not rotate;
then brush bearings with a soft bristled brush until all for
eign m aterial has been removed.
2. Rinse bearings in clean solvent; then blow bearings
dry with air pressure. D O N O T S P IN B E A R IN G S
W H IL E D R Y IN G .
3. R otate each bearing slowly while exam ining balls or
rollers for roughness, dam age, or excessive wear. Replace
all bearings which are in questionable condition.
4. Pack all bearings with bearing lubricant (such as,
N L G I N o. 0 Light W eight Ball and Roller Bearing
Grease).
5. W rap each bearing in clean lint-free paper until ready
to install in transm ission.
GEARS A N D SHAFTS
1. C heck operating gear teeth for pitting on tooth faces.
Gears with pitted teeth should be replaced.
2. C heck all engaging gear teeth. G ears with teeth worn,
tapered or reduced in length from clashing in shifting
should be replaced.
N O T E : S m a ll nicks or burrs m a y be re m o ve d
w ith a fin e a b r a s iv e stone.
IM P O R T A N T
The sp lin es on m a n y clu tch in g ge ars, m a in
shaft, etc., are e q u ip p e d w it h a m a c h in e d relief
called a " h o p p in g g u a r d " a s s h o w n in figu re
10. W ith the clutch g e a r in the e n g a g e d posi
tion, the m a t in g g e a r is free to slip into this
notch, p re v e n tin g the tw o g e a r s from s e p a r a t
in g or ''w a l k in g out of g e a r " u n d e r v a rio u s
lo a d conditions. This is not a w o r n or c h ip p e d
g e a r. D O N O T G R I N D IT D O W N O R D IS C A R D
T H E G E A R F O R T H IS R E A S O N .
3. Check the splines on all shafts for wear. If the m ain
shaft 1st and reverse sliding gear or clutch hub have worn
into the sides of the splines, the shaft in this condition
should be replaced.
H O U SIN G S A N D BEARIN G CAPS
1. Check each housing or bearing cap for cracks, breaks
or other dam age. Since repairs by welding, brazing, etc.,
are not recom m ended, replace all dam aged parts.
2. Check bores for wear. R eplace com ponents worn
oversize.
3. Check bearing caps for end thrust from bearings. R e
place if worn or grooved.
SYN CH RO N IZERS A N D SHIFTER
H O U SIN G C O M PO N EN T S
1. Check bronze synchronizer cone for wear or possibly
steel chips em bedded in cone.
2. Inspect blocker pin detents of synchronizer for wear
or other dam age.
N O T E : If a n y portion o f a syn ch ron ize r is d a m
a g e d , replace entire synch ronize r a sse m b ly .
3. Inspect each of the three shift forks for wear, distor
tion, or other dam age.
4. C heck each shift rod, interlock ball, and the interlock
pin for scoring, distortion or other dam age. Replace all
dam aged com ponents.
GASKETS, THRUST WASHERS, ETC.
1. Replace all gaskets, oil seals, lock wire, cotter pins
and snap rings.
CHEVROLET SERIES 70-80 H EAVY DUTY TRUCK SH O P M A N U A L
Summary of Contents for 70 1969 Series
Page 1: ...CHEVROLET HEAVY DUTY TRUCK SHOP MANUAL...
Page 3: ......
Page 11: ...LUBRICATION 0 4 CHEVROLET SERIES 70 80 HEAVY DUTY TRUCK SHOP MANUAL...
Page 27: ......
Page 119: ......
Page 361: ......
Page 371: ......
Page 427: ......
Page 443: ......
Page 451: ......
Page 493: ......
Page 499: ......
Page 549: ......
Page 555: ......
Page 609: ......
Page 715: ...am...
Page 745: ......
Page 910: ......
Page 913: ......