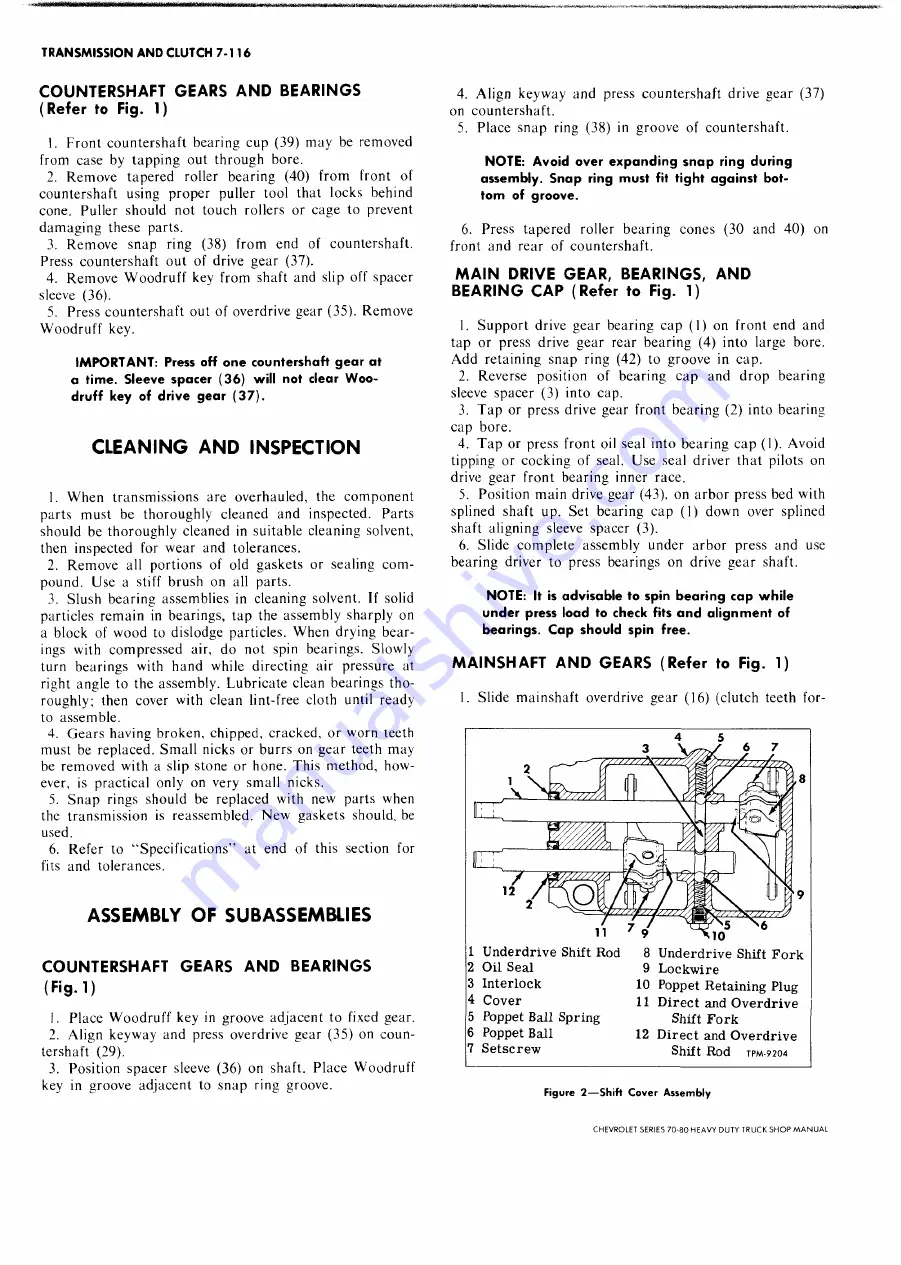
TRANSMISSION AND CLUTCH 7-116
COUNTERSHAFT GEARS AND BEARINGS
(Refer to Fig. 1)
1. F ront countershaft bearing cup (39) m ay be removed
from case by tapping out through bore.
2. Remove tapered roller bearing (40) from front of
countershaft using proper puller tool that locks behind
cone. Puller should not touch rollers or cage to prevent
dam aging these parts.
3. R em ove snap ring (38) from end of countershaft.
Press countershaft out of drive gear (37).
4. R em ove W oodruff key from shaft and slip off spacer
sleeve (36).
5. Press countershaft out of overdrive gear (35). Remove
W oodruff key.
IMPORTANT: Press off one countershaft gear at
a time. Sleeve spacer (36) will not clear Woo
druff key of drive gear (37).
CLEANING A N D INSPECTION
1. W hen transm issions are overhauled, the com ponent
parts m ust be thoroughly cleaned and inspected. Parts
should be thoroughly cleaned in suitable cleaning solvent,
then inspected for wear and tolerances.
2. Remove all portions of old gaskets or sealing co m
pound. Use a stiff brush on all parts.
3. Slush bearing assemblies in cleaning solvent. If solid
particles rem ain in bearings, tap the assem bly sharply on
a block of wood to dislodge particles. W hen drying bear
ings with com pressed air, do not spin bearings. Slowly
turn bearings with hand while directing air pressure at
right angle to the assembly. Lubricate clean bearings th o
roughly; then cover with clean lint-free cloth until ready
to assemble.
4. G ears having broken, chipped, cracked, or worn teeth
m ust be replaced. Sm all nicks or burrs on gear teeth may
be removed with a slip stone or hone. This m ethod, how
ever, is practical only on very small nicks.
5. Snap rings should be replaced with new parts when
the transm ission is reassembled. New gaskets should, be
used.
6. Refer to “ Specifications” at end of this section for
fits and tolerances.
ASSEMBLY OF SUBASSEMBLIES
COUNTERSHAFT GEARS AND BEARINGS
(Fig-1)
1. Place W oodruff key in groove adjacent to fixed gear.
2. Align keyway and press overdrive gear (35) on coun
tershaft (29).
3. Position spacer sleeve (36) on shaft. Place W oodruff
key in groove adjacent to snap ring groove.
4. Align keyway and press countershaft drive gear (37)
on countershaft.
5. Place snap ring (38) in groove of countershaft.
NOTE: Avoid over expanding snap ring during
assembly. Snap ring must fit tight against bot
tom of groove.
6. Press tapered roller bearing cones (30 and 40) on
front and rear of countershaft.
MAIN DRIVE GEAR, BEARINGS, AND
BEARING CAP (Refer to Fig. 1)
1. S upport drive gear bearing cap (1) on front end and
tap or press drive gear rear bearing (4) into large bore.
Add retaining snap ring (42) to groove in cap.
2. Reverse position of bearing cap and drop bearing
sleeve spacer (3) into cap.
3. T ap or press drive gear front bearing (2) into bearing
cap bore.
4. T ap or press front oil seal into bearing cap (1). Avoid
tipping or cocking of seal. Use seal driver th at pilots on
drive gear front bearing inner race.
5. Position m ain drive gear (43), on arbor press bed with
spliried shaft up. Set bearing cap (1) down over splined
shaft aligning sleeve spacer (3).
6. Slide com plete assembly under arbor press and use
bearing driver to press bearings on drive gear shaft.
NOTE: It is advisable to spin bearing cap while
under press load to check fits and alignment of
bearings. Cap should spin free.
MAINSHAFT AND GEARS (Refer to Fig. 1)
1. Slide m ainshaft overdrive gear (16) (clutch teeth for-
CHEVROLET SERIES 70-80 H EAVY DUTY TRUCK S H O P M A N U A L
Summary of Contents for 70 1969 Series
Page 1: ...CHEVROLET HEAVY DUTY TRUCK SHOP MANUAL...
Page 3: ......
Page 11: ...LUBRICATION 0 4 CHEVROLET SERIES 70 80 HEAVY DUTY TRUCK SHOP MANUAL...
Page 27: ......
Page 119: ......
Page 361: ......
Page 371: ......
Page 427: ......
Page 443: ......
Page 451: ......
Page 493: ......
Page 499: ......
Page 549: ......
Page 555: ......
Page 609: ......
Page 715: ...am...
Page 745: ......
Page 910: ......
Page 913: ......