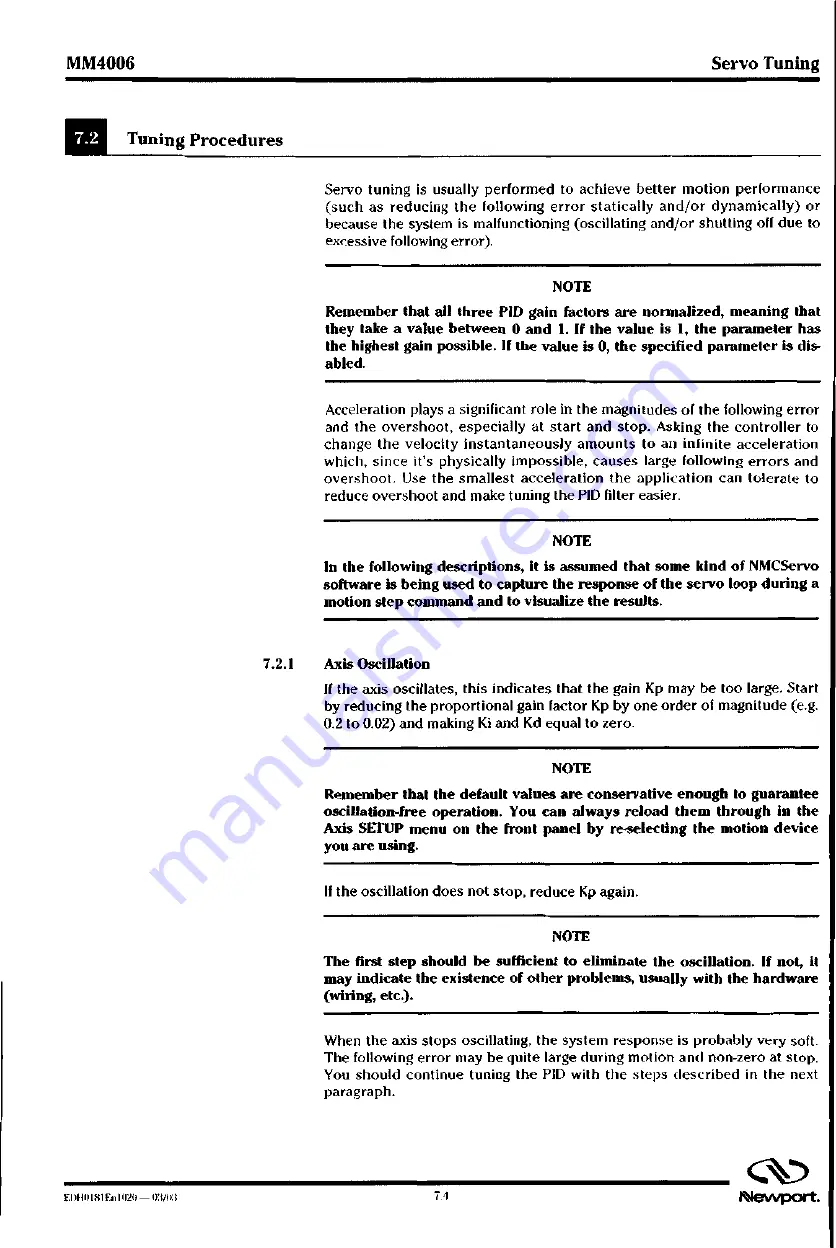
MM4006
Servo Tuning
7.2
Tuning Procedures
Servo tuning is usually performed to achieve better motion performance
(such as reducing the following error statically and/or dynamically) or
because the system is malfunctioning (oscillating and/or shutting off due to
excessive following error).
NOTE
Remember that all three PID gain factors are normalized, meaning that
they take a value between 0 and 1. If the value is 1, the parameter has
the highest gain possible. If the value is 0, the specified parameter is dis-
abled.
Acceleration plays a significant role in the magnitudes of the following error
and the overshoot, especially at start and stop. Asking the controller to
change the velocity instantaneously amounts to an infinite acceleration
which, since it's physically impossible, causes large following errors and
overshoot. Use the smallest acceleration the application can tolerate to
reduce overshoot and make tuning the PID filter easier.
NOTE
In the following descriptions, it is assumed that some kind of NMCServo
software is being used to capture the response of the servo loop during a
motion step command and to visualize the results.
7.2.1 A x i s Oscillation
If
the axis oscillates, this indicates that the gain Kp may be too large. Start
by reducing the proportional gain factor Kp by one order of magnitude (e.g.
0.2 to 0.02) and making Ki and Kd equal to zero.
NOTE
Remember that the default values are conservative enough to guarantee
oscillation-free operation. You can always reload them through in the
Axis SETUP menu on the front panel by re-selecting the motion device
you are using.
If
the oscillation does not stop, reduce Kp again.
NOTE
The first step should be sufficient to eliminate the oscillation. I f not, it
may indicate the existence of other problems, usually with the hardware
(wiring, etc).
When the axis stops oscillating, the system response is probably very soft.
The following error may be quite large during motion and non-zero at stop.
You should continue tuning the PID with the steps described in the next
paragraph.
C * ,
El )110181En11120 — 03/03
7.4
N
e
v
v
p
o
r
t
.
Summary of Contents for MM4006
Page 9: ...F D110181En1020 03 03 b J e w p o r t...
Page 11: ...MM4006 8 Axis Motion Controller Driver evvport...
Page 41: ...MM4006 Introduction FPI 111181Eli11120 0 1 03 1 3O tNevvport...
Page 42: ...Section 2 Local Mode C Newport...
Page 43: ...MM4006 8 Axis Motion Controller Driver C N e w p o r t...
Page 96: ...Section 3 Remote Mode C klevvport...
Page 97: ...Newport...
Page 310: ...Section 4 Motion Control Tutorial Ilevvport...
Page 311: ...MM4006 8 Axis Motion Controller Driver C EDI10181En 1020 03 03 2 N e V V p O r t...
Page 313: ...MM4006 8 Axis Motion Controller Driver cv ED110181E01020 03 03 4 2 M e v v p o r t...
Page 334: ...Section 5 Trajectory Functions Tutorial Newport...
Page 335: ...MM4006 8 Axis Motion Controller Driver C Newport...
Page 337: ...MM4006 8 Axis Motion Controller Driver EDH0181En1020 03 03 5 2 N e w p o r t...
Page 346: ...Section 6 Feature Descriptions Tutorial Newport...
Page 347: ...MM4006 8 Axis Motion Controller Driver C Nevvport...
Page 349: ...MM4006 8 Axis Motion Controller Driver ED11018lEn I 020 03 03 6 2 N e v v p O r t...
Page 359: ...MM4006 F e a t u r e Descriptions Tutorial cv EDI10181En1020 03 03 6 12 N e w p o r t...
Page 360: ...Section 7 Servo Tuning rano at 1 2 2 p EOF 110 1 0 0 0 0 0 ill fpL4 cv Newport...
Page 361: ...MM4006 8 Axis Motion Controller Driver C Nevvport...
Page 363: ...MM4006 8 Axis Motion Controller Driver EDH0181En 1020 03 03 7 2...
Page 368: ...Section 8 Appendices INevvport...
Page 369: ...MM4006 8 Axis Motion Controller Driver CkJ Newport...
Page 371: ...MM4006 8 Axis Motion Controller Driver EDI10181EnI020 03 03 8 2 N e v v p o r t...
Page 410: ...A7 h7s z c 7...