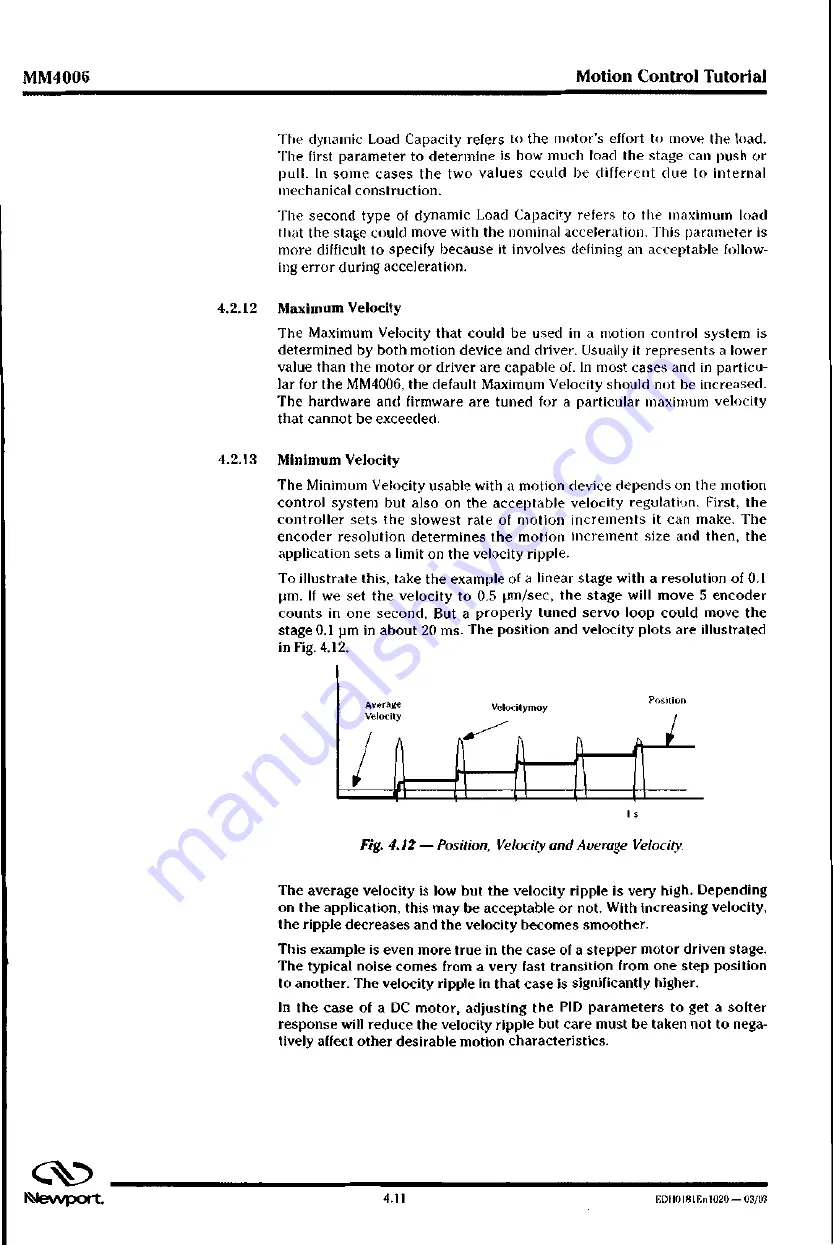
MM4006
M
o
t
i
o
n
Control Tutorial
The dynamic Load Capacity refers to the motor's effort to move the load.
The first parameter to determine is how much load the stage can push or
pull. In some cases the two values could be different clue to internal
mechanical construction.
The second type of dynamic Load Capacity refers to the maximum load
that the stage could move with the nominal acceleration. This parameter is
more difficult to specify because it involves defining an acceptable follow-
ing error during acceleration.
4.2.12 M a x i m u m Velocity
The Maximum Velocity that could be used in a motion control system is
determined by both motion device and driver. Usually it represents a lower
value than the motor or driver are capable of. In most cases and in particu-
lar for the MM4006, the default Maximum Velocity should not be increased.
The hardware and firmware are tuned for a particular maximum velocity
that cannot be exceeded.
4.2.13 M i n i m u m Velocity
The Minimum Velocity usable with a motion device depends on the motion
control system but also on the acceptable velocity regulation. First, the
controller sets the slowest rate of motion increments i t can make. The
encoder resolution determines the motion increment size and
then, the
application sets a limit on the velocity ripple.
To illustrate this, take the example of a linear stage
with
a
resolution of 0.1
pm. If we set the velocity to 0.5 pm/sec,
the stage will move
5
encoder
counts in one second. But a properly tuned servo loop could move the
stage 0.1 pm in about 20 ms. The position and velocity plots are illustrated
in Fig. 4.12.
Average
Velocity
Velocitymoy
Position
I s
Fig. 4.12
— Position, Velocity and Average Velocity.
The average velocity is low but the velocity ripple is very high. Depending
on the application, this may be acceptable or not. With increasing velocity,
the ripple decreases and the velocity becomes smoother.
This example is even more true in the case of a stepper motor driven stage.
The typical noise comes from a very fast transition from one step position
to another. The velocity ripple in that case is significantly higher.
In the case of a DC motor, adjusting the PID parameters to get a softer
response will reduce the velocity ripple but care must be taken not to nega-
tively affect other desirable motion characteristics.
( % )
N e V V p O r t
4
.
1
1
E
M
I
°
8 I En1020 — 03/03
Summary of Contents for MM4006
Page 9: ...F D110181En1020 03 03 b J e w p o r t...
Page 11: ...MM4006 8 Axis Motion Controller Driver evvport...
Page 41: ...MM4006 Introduction FPI 111181Eli11120 0 1 03 1 3O tNevvport...
Page 42: ...Section 2 Local Mode C Newport...
Page 43: ...MM4006 8 Axis Motion Controller Driver C N e w p o r t...
Page 96: ...Section 3 Remote Mode C klevvport...
Page 97: ...Newport...
Page 310: ...Section 4 Motion Control Tutorial Ilevvport...
Page 311: ...MM4006 8 Axis Motion Controller Driver C EDI10181En 1020 03 03 2 N e V V p O r t...
Page 313: ...MM4006 8 Axis Motion Controller Driver cv ED110181E01020 03 03 4 2 M e v v p o r t...
Page 334: ...Section 5 Trajectory Functions Tutorial Newport...
Page 335: ...MM4006 8 Axis Motion Controller Driver C Newport...
Page 337: ...MM4006 8 Axis Motion Controller Driver EDH0181En1020 03 03 5 2 N e w p o r t...
Page 346: ...Section 6 Feature Descriptions Tutorial Newport...
Page 347: ...MM4006 8 Axis Motion Controller Driver C Nevvport...
Page 349: ...MM4006 8 Axis Motion Controller Driver ED11018lEn I 020 03 03 6 2 N e v v p O r t...
Page 359: ...MM4006 F e a t u r e Descriptions Tutorial cv EDI10181En1020 03 03 6 12 N e w p o r t...
Page 360: ...Section 7 Servo Tuning rano at 1 2 2 p EOF 110 1 0 0 0 0 0 ill fpL4 cv Newport...
Page 361: ...MM4006 8 Axis Motion Controller Driver C Nevvport...
Page 363: ...MM4006 8 Axis Motion Controller Driver EDH0181En 1020 03 03 7 2...
Page 368: ...Section 8 Appendices INevvport...
Page 369: ...MM4006 8 Axis Motion Controller Driver CkJ Newport...
Page 371: ...MM4006 8 Axis Motion Controller Driver EDI10181EnI020 03 03 8 2 N e v v p o r t...
Page 410: ...A7 h7s z c 7...