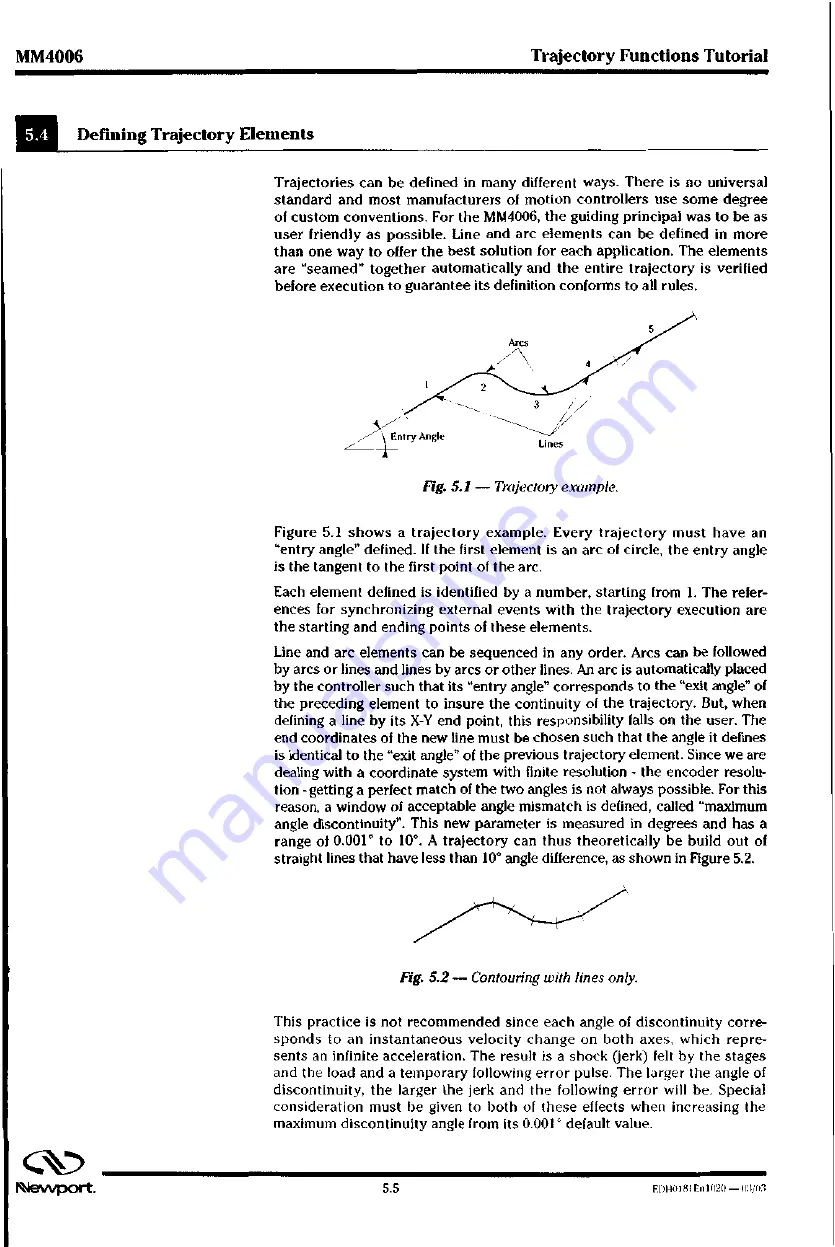
MM4006
Trajectory Functions Tutorial
5.4
Defining Trajectory Elements
Trajectories can be defined in many different ways. There is no universal
standard and most manufacturers of motion controllers use some degree
of custom conventions. For the MM4006, the guiding principal was to be as
user friendly as possible. Line and arc elements can be defined i n more
than one way to offer the best solution for each application. The elements
are "seamed" together automatically and the entire trajectory is verified
before execution to guarantee its definition conforms to all rules.
Entry Angle
Arcs
3
Lines
Fig. 5.1 — Trajectory example.
Figure 5.1 shows a trajectory example. Every trajectory must have an
"entry angle" defined. If the first element is an arc of circle, the entry angle
is the tangent to the first point of the arc.
Each element defined is identified by a number, starting from 1. The refer-
ences for synchronizing external events with the trajectory execution are
the starting and ending points of these elements.
Line and arc elements can be sequenced in any order. Arcs can be followed
by arcs or lines and lines by arcs or other lines. An arc is automatically placed
by the controller such that its "entry angle" corresponds to the "exit angle" of
the preceding element to insure the continuity of the trajectory. But, when
defining a line by its X-Y end point, this responsibility falls on the user. The
end coordinates of the new line must be chosen such that the angle it defines
is identical to the "exit angle" of the previous trajectory element. Since we are
dealing with a coordinate system with finite resolution - the encoder resolu-
tion - getting a perfect match of the two angles is not always possible. For this
reason, a window of acceptable angle mismatch is defined, called "maximum
angle discontinuity". This new parameter is measured in degrees and has a
range of 0.001° to 10°. A trajectory can thus theoretically be build out of
straight lines that have less than 10° angle difference, as shown in Figure 5.2.
Fig. 5.2 — Contouring with lines only.
This practice is not recommended since each angle of discontinuity corre-
sponds t o an instantaneous velocity change on both axes, which repre-
sents an infinite acceleration. The result is a shock (jerk) felt by the stages
and the load and a temporary following error pulse. The larger the angle of
discontinuity, the larger the jerk and the following error will be. Special
consideration must be given to both of these effects when increasing the
maximum discontinuity angle from its 0.001' default value.
(%)
Newport.
5
.
5
EDH01 81 En 1020 — 03/03
Summary of Contents for MM4006
Page 9: ...F D110181En1020 03 03 b J e w p o r t...
Page 11: ...MM4006 8 Axis Motion Controller Driver evvport...
Page 41: ...MM4006 Introduction FPI 111181Eli11120 0 1 03 1 3O tNevvport...
Page 42: ...Section 2 Local Mode C Newport...
Page 43: ...MM4006 8 Axis Motion Controller Driver C N e w p o r t...
Page 96: ...Section 3 Remote Mode C klevvport...
Page 97: ...Newport...
Page 310: ...Section 4 Motion Control Tutorial Ilevvport...
Page 311: ...MM4006 8 Axis Motion Controller Driver C EDI10181En 1020 03 03 2 N e V V p O r t...
Page 313: ...MM4006 8 Axis Motion Controller Driver cv ED110181E01020 03 03 4 2 M e v v p o r t...
Page 334: ...Section 5 Trajectory Functions Tutorial Newport...
Page 335: ...MM4006 8 Axis Motion Controller Driver C Newport...
Page 337: ...MM4006 8 Axis Motion Controller Driver EDH0181En1020 03 03 5 2 N e w p o r t...
Page 346: ...Section 6 Feature Descriptions Tutorial Newport...
Page 347: ...MM4006 8 Axis Motion Controller Driver C Nevvport...
Page 349: ...MM4006 8 Axis Motion Controller Driver ED11018lEn I 020 03 03 6 2 N e v v p O r t...
Page 359: ...MM4006 F e a t u r e Descriptions Tutorial cv EDI10181En1020 03 03 6 12 N e w p o r t...
Page 360: ...Section 7 Servo Tuning rano at 1 2 2 p EOF 110 1 0 0 0 0 0 ill fpL4 cv Newport...
Page 361: ...MM4006 8 Axis Motion Controller Driver C Nevvport...
Page 363: ...MM4006 8 Axis Motion Controller Driver EDH0181En 1020 03 03 7 2...
Page 368: ...Section 8 Appendices INevvport...
Page 369: ...MM4006 8 Axis Motion Controller Driver CkJ Newport...
Page 371: ...MM4006 8 Axis Motion Controller Driver EDI10181EnI020 03 03 8 2 N e v v p o r t...
Page 410: ...A7 h7s z c 7...