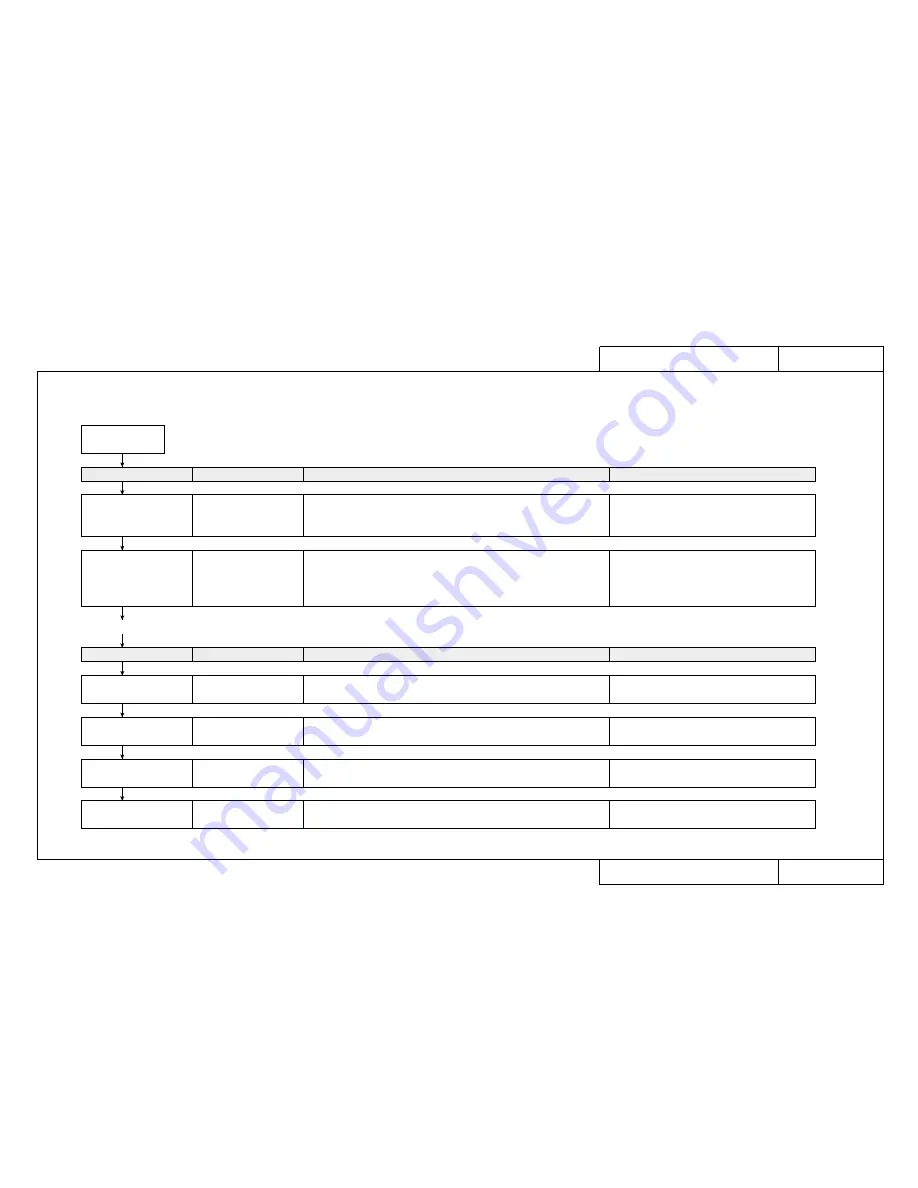
10
C O N 4 0 1 0
Model Name:
RJ–4100
C O N 4 0 1 0
Model Name:
RJ–4100
How to use the Maintenance Manual
How to use the Maintenance Manual
■
Fault maintenance work procedures and how to use the Maintenance Manual
When a user reports an equipment fault, use the following procedure to carry out fault recovery tasks.
A fault occurs
Task
Page
Details
Reference materials
Check fault circumstances,
select fault details from
Trouble-Shooting Lists
Trouble-Shooting List
TRB
❉❉❉❉
Check circumstances by “fax” or “telephone”. Check error
messages, check user usage conditions, retry after changing settings, output
diagnostic pattern, etc. Select fault symptoms produced by user from
the Trouble-Shooting List.
Conduct a consultation by “fax” or “telephone”.
Check possibility of user error or recovery by daily inspection. Check error
messages, check user usage conditions, output diagnostic pattern, output
setup list. Retry after changing settings, etc.
Primary Consultation
ENT
❉❉❉❉
Operation Manual, basic
knowledge, daily care, periodic maintenance/
inspection/cleaning
Task
Page
Details
Reference materials
Gather the necessary
maintenance parts
Matrix Map
MAP
❉❉❉❉
Gather the necessary maintenance parts
Maintenance Parts list, Maintenance Tools list,
Exploded views
Conduct a tracing inquiry
Fault Tracing Procedures
EXA
❉❉❉❉
Conduct an inquiry to trace the cause of the fault
Basic knowledge
Replace parts and adjust
Replacement and Adjustment
Procedures REP
❉❉❉❉
Replace or readjust parts suspected to be faulty.
Carry out adjustments after replacing parts.
Basic knowledge
Final check
Test Procedures
TST
❉❉❉❉
Separate causes of faults and check operation after faults have been
rectified.
Conduct a primary
consultation with the user
• If you are unable to resolve the fault at this point, take the necessary maintenance parts and make an on-site visit.