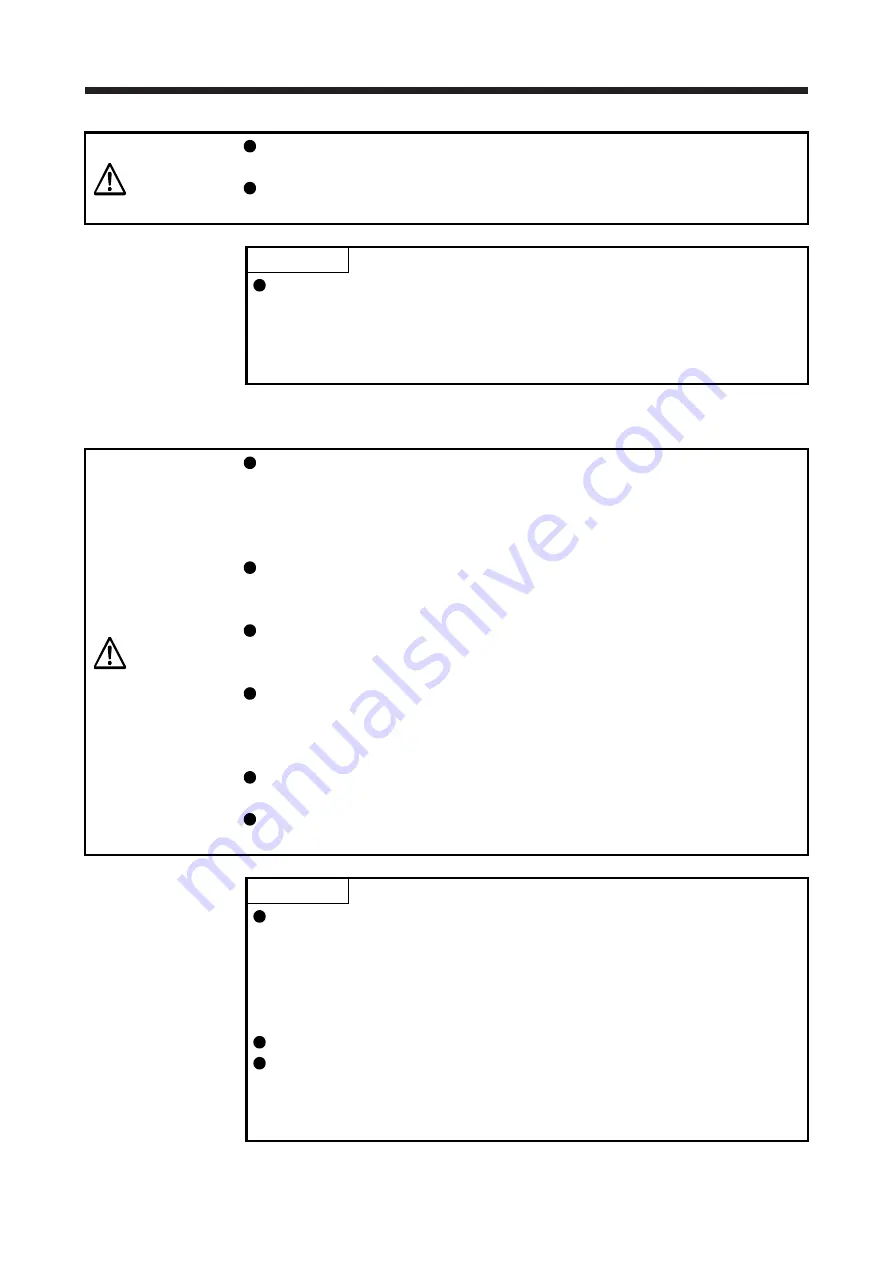
3. SIGNALS AND WIRING
3 - 2
CAUTION
Connecting a servo motor for different axis to the CNP3A, CNP3B, or CN3C
connector may cause a malfunction.
Before wiring, switch operation, etc., eliminate static electricity. Otherwise, it may
cause a malfunction.
POINT
When you use a linear servo motor, replace the following words in the left to the
words in the right.
Load to motor inertia ratio
→
Load to motor mass ratio
Torque
→
thrust
(Servo motor) Speed
→
(Linear servo motor) Speed
3.1 Input power supply circuit
CAUTION
Always connect a magnetic contactor between the power supply and the main
circuit power supply (L1/L2/L3) of the servo amplifier, in order to configure a
circuit that shuts down the power supply on the side of the servo amplifier’s power
supply. If a magnetic contactor is not connected, continuous flow of a large
current may cause a fire when the servo amplifier malfunctions.
When alarms are occurring in all axes of A, B, and C, shut off the main circuit
power supply. Not doing so may cause a fire when a regenerative transistor
malfunctions or the like may overheat the regenerative resistor.
Check the servo amplifier model, and then input proper voltage to the servo
amplifier power supply. If input voltage exceeds the upper limit, the servo amplifier
will break down.
The servo amplifier has a built-in surge absorber (varistor) to reduce exogenous
noise and to suppress lightning surge. Exogenous noise or lightning surge
deteriorates the varistor characteristics, and the varistor may be damaged. To
prevent a fire, use a molded-case circuit breaker or fuse for input power supply.
Connecting a servo motor for different axis to the CNP3A, CNP3B, or CN3C
connector may cause a malfunction.
The N- terminal is not a neutral point of the power supply. Incorrect wiring will
cause a burst, damage, etc.
POINT
Even if alarm has occurred, do not switch off the control circuit power supply.
When the control circuit power supply has been switched off, optical module
does not operate, and optical transmission of SSCNET III/H communication is
interrupted. Therefore, the next axis servo amplifier displays "AA" at the
indicator and turns into base circuit shut-off. The servo motor stops with starting
dynamic brake.
EM2 has the same device as EM1 in the torque control mode.
Connect the 1-phase 200 V AC to 240 V AC power supply to L1 and L3. One of
the connecting destinations is different from MR-J3W Series Servo Amplifier.
When using MR-J4W as a replacement for MR-J3W, be careful not to connect
the power to L2.
Summary of Contents for MR-J4W2-0303B6
Page 39: ...2 INSTALLATION 2 8 MEMO ...
Page 97: ...4 STARTUP 4 20 MEMO ...
Page 181: ...6 NORMAL GAIN ADJUSTMENT 6 28 MEMO ...
Page 235: ...9 DIMENSIONS 9 6 MEMO ...
Page 245: ...10 CHARACTERISTICS 10 10 MEMO ...
Page 309: ...13 USING STO FUNCTION 13 14 MEMO ...
Page 365: ...15 USING A DIRECT DRIVE MOTOR 15 24 MEMO ...
Page 389: ...16 FULLY CLOSED LOOP SYSTEM 16 24 MEMO ...
Page 461: ...17 APPLICATION OF FUNCTIONS 17 72 MEMO ...
Page 556: ...APPENDIX App 41 ...
Page 585: ...MEMO ...