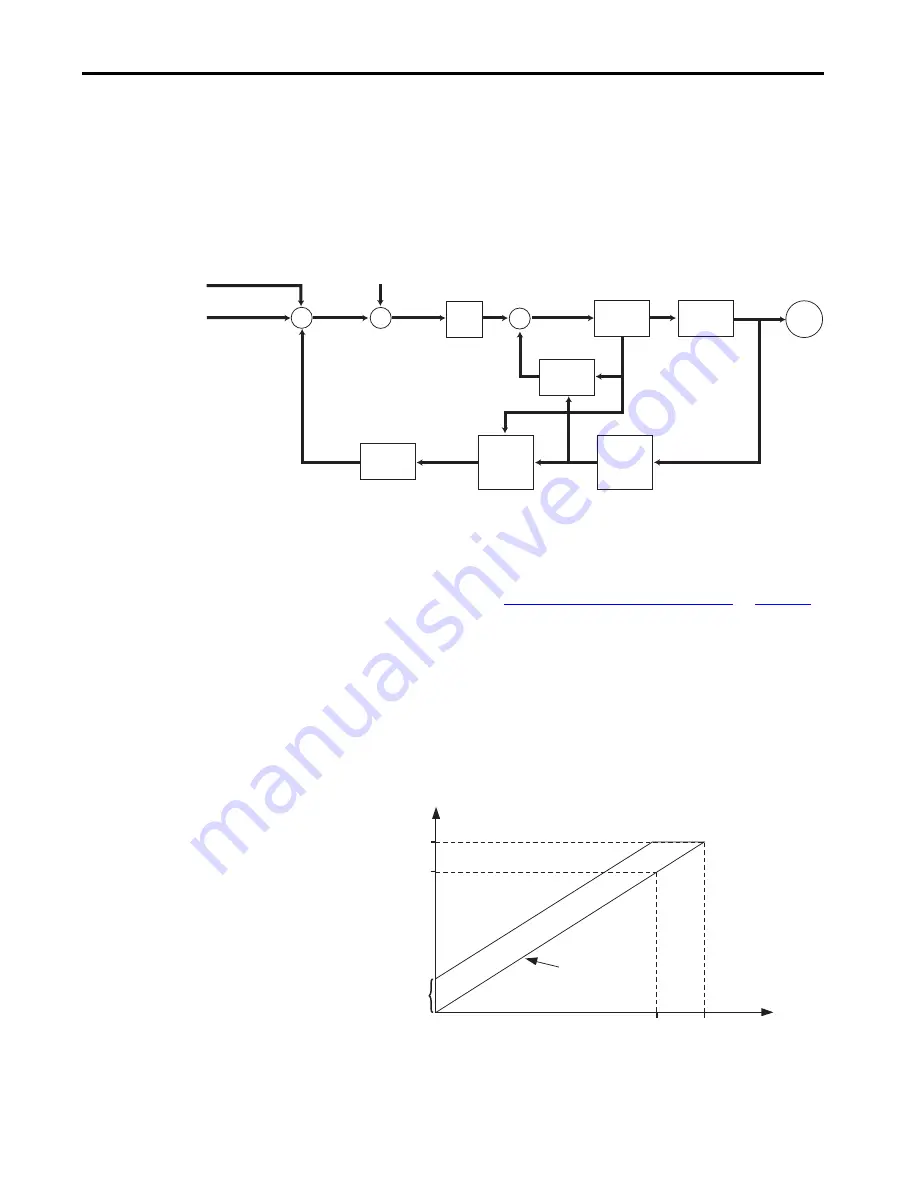
Rockwell Automation Publication 2198-UM002E-EN-P - February 2018
329
Motor Control Feature Support
Appendix D
Sensorless Vector
The Sensorless Vector method uses a volts/hertz core enhanced by a current
resolver, slip estimator, and a voltage-boost compensator based on the
operating conditions of the motor.
Figure 159 - Sensorless Vector Method
The algorithms operate on the knowledge of the relationship between the
rated slip and torque of the motor. The drive uses applied voltages and
measured currents to estimate operating slip-frequency. You can enter values to
identify the motor resistance value or you can run a motor test to identify the
motor resistance value (see
Motor Tests and Autotune Procedure
).
Motor nameplate data and test results are ways to accurately estimate the
required boost voltage.
The sensorless vector method offers better torque production and speed
regulation over a wider speed range than basic volts/hertz.
Dynamic boost is applied internally to compensate voltage drop and improve
starting torque.
Figure 160 - Approximate Load Curve
+
x
+
Velocity Trim
Velocity Command
Slip Speed
V/Hz
Motor Pole
Pairs
Vboost
Estimator
Voltage
Control
Current
Feedback
Current
Resolver
Torque
Estimate
Load
Torque
Estimator
Slip
Estimation
Inverter
Motor
Frequency,
max
Ideal, volts/hertz
Base Frequency,
(nameplate)
Dynamic Boost Applied
Base Voltage
(nameplate)
Voltage, max