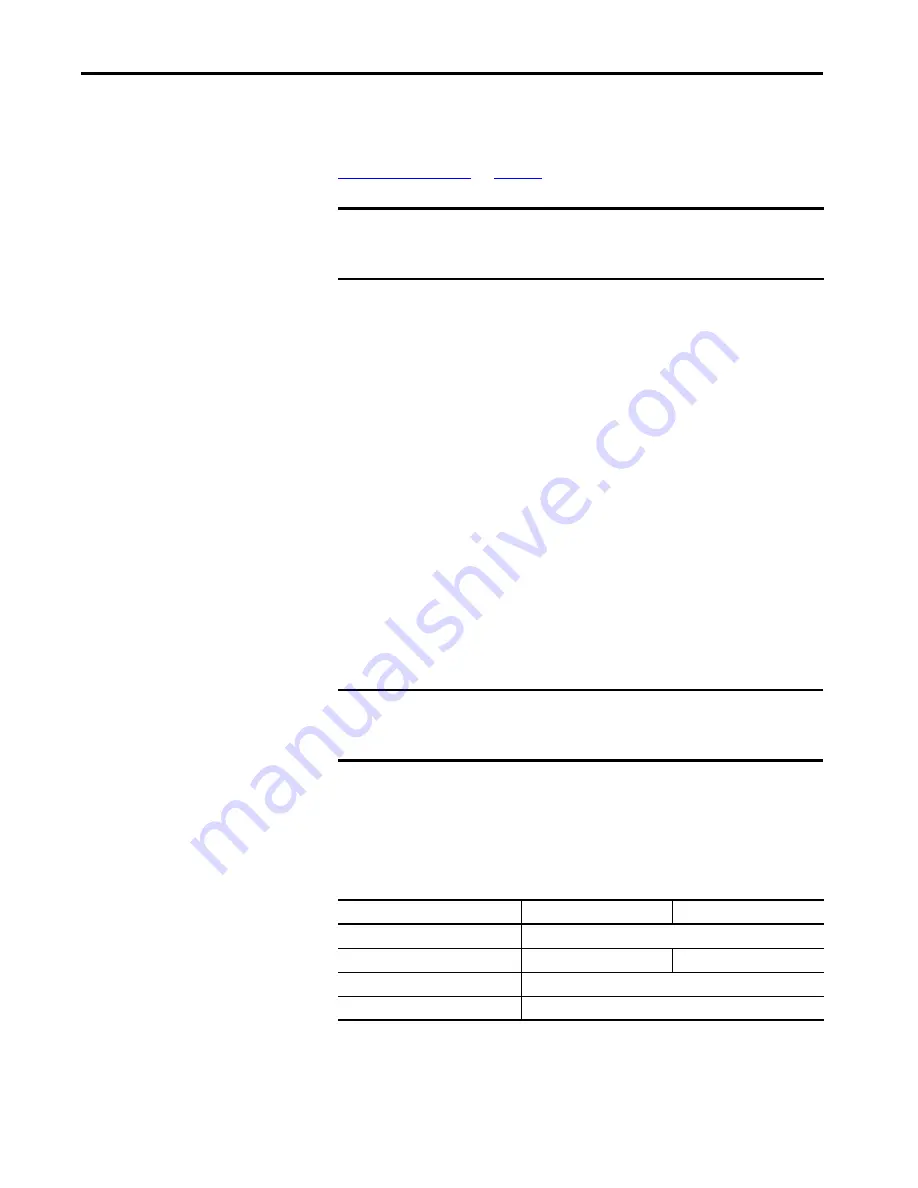
262
Rockwell Automation Publication 2198-UM002E-EN-P - February 2018
Chapter 9
Kinetix 5700 Safe Torque-off Function
For safety system requirements, including information on the safety network
number (SNN), verifying the safety signature, and functional verification tests
refer to the appropriate GuardLogix controller publication as defined in
Description of Operation
The safe torque-off (STO) feature provides a method, with sufficiently low
probability of failure, to force the power-transistor control signals to a disabled
state. When the command to execute the STO function is received from the
GuardLogix controller, all of the drive output-power transistors are released
from the ON-state. This results in a condition where the drive is coasting.
Disabling the power transistor output does not provide mechanical isolation of
the electrical output that is required for some applications.
These conditions must be met for integrated control of the STO function:
• The Kinetix 5700 add-on-profile (AOP) must be added to the Bulletin
1756 EtherNet/IP communication module, configured as part of the
GuardLogix 5570 or Compact GuardLogix 5370 controller I/O tree.
• The AOP must be configured for Safety-only or Motion and Safety
connections
• The safety bypass jumper wires must be removed.
The Kinetix 5700 drive STO function response time is less than 10 ms.
Response time for the drive is the delay between the time the drive STO
command receives the CIP Safety™ packet with an STO request and the time
when motion producing power is removed from the motor.
Table 136 - Safe Torque-off Network Specifications
IMPORTANT
You must read, understand, and fulfill the requirements detailed in the
GuardLogix controller systems safety reference manual prior to operating
a safety system that uses a GuardLogix controller and Kinetix 5700 drive.
IMPORTANT
If the STO bypass jumper wires were applied during machine
commissioning or maintenance, they must be removed before the drive
will operate in Integrated STO mode.
Attribute
2198-
xxxx
-ERS3
2198-
xxxx
-ERS4
Safety connection RPI, min
6 ms
Input assembly connections
(1)
(1) Motion and Safety and Safety Only connections with the inverter uses 1 input assembly connection and 1 output assembly
connection.
3
1
1
Integrated safety open request support
Type 1 and Type 2 requests