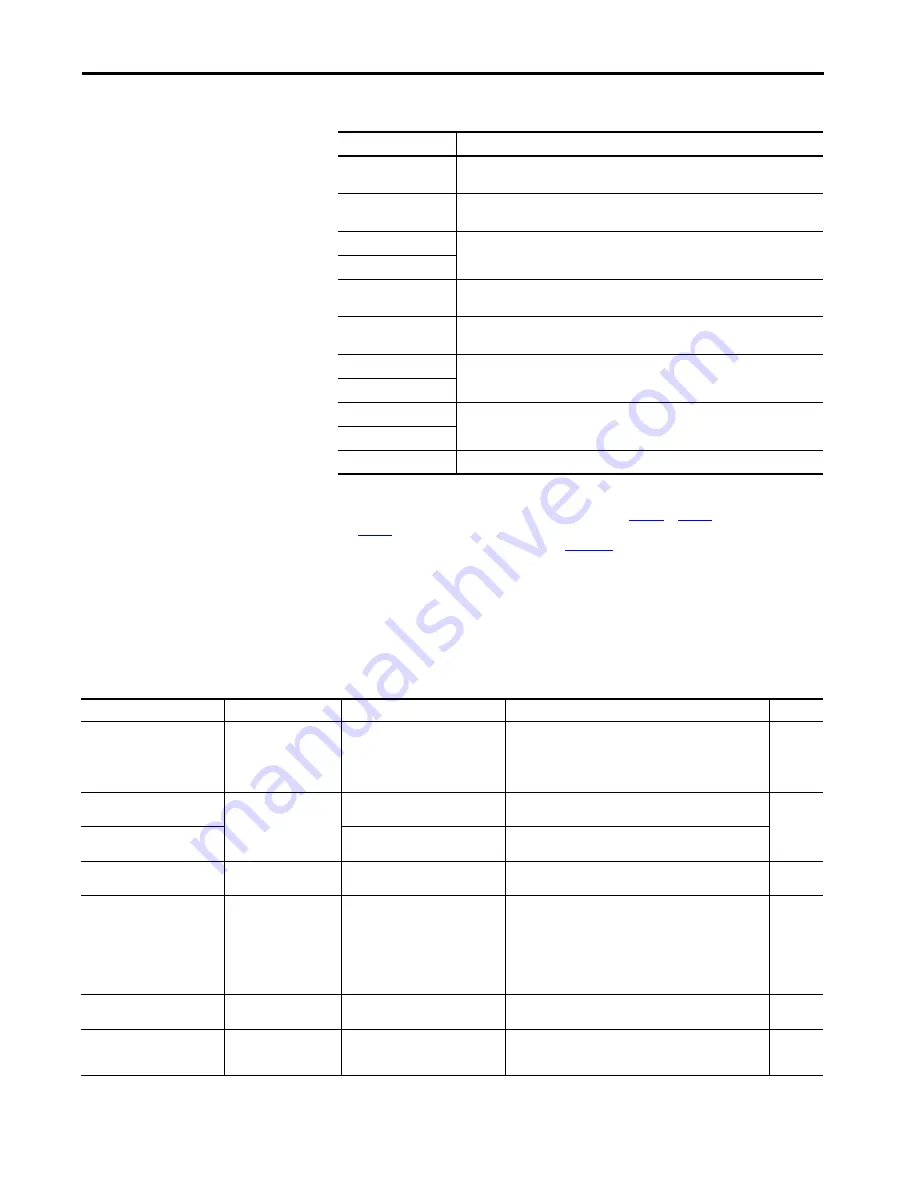
Rockwell Automation Publication 2198-UM002E-EN-P - February 2018
215
Troubleshoot the Kinetix 5700 Drive System
Chapter 7
Table 94 - Fault Code Summary
Fault Code Type
(1)
(2)
(1) S
xx
refers to Standard exceptions.
(2) M
xx
refers to Manufacturer-specific exceptions.
Description
FLT S
xx
Standard runtime axis exceptions. The exception can apply to an individual axis or to
all axes.
FLT M
xx
Manufacturer-specific runtime axis exception. The exception can apply to an individual
axis or to all axes.
INIT FLT S
xx
Exceptions that prevent normal operation and occur during the initialization process.
INIT FLT M
xx
NODE FLT
xx
Exceptions that can prevent normal operation of the drive module and apply to the
entire module and affect all axes.
NODE ALARM
xx
Exceptions that can prevent normal operation of the drive module, but do not result in
any action other than reporting the alarm to the controller.
INHIBIT S
xx
Conditions that prevent normal operation and indicate the drive module is prevented
from being enabled.
INHIBIT M
xx
ALARM S
xx
An underlying exception condition that does not result in any action other than
reporting the alarm to the controller.
ALARM M
xx
SAFE FLT
xx
(3)
(3) For troubleshooting 2198-
xxxx
-ERS3 inverter SAFE FLT fault codes, refer to
on
(hardwired safety) or
(integrated safety). For troubleshooting 2198-
xxxx
-ERS4 inverter SAFE FLT fault codes, refer to the Kinetix 5700 Safe
Monitor Functions Safety Reference Manual, publication
Exception generated by a fault condition detected in the safety function.
TIP
Fault codes triggered by conditions that fall outside factory set limits are identified by
FL at the end of the display message. For example, FLT S07 – MTR OVERLOAD FL.
Fault codes triggered by conditions that fall outside user set limits are identified by UL
at the end of the display message. For example, FLT S08 – MTR OVERLOAD UL.
Table 95 - FLT S
xx
Fault Codes
Exception Code on Display
Exception Text
Problem
Possible Solutions
Module
FLT S02 – MTR COMMUTATION
Motor Commutation Fault
An illegal state transition of the motor
hall-commutation feedback signals has
been detected.
• Verify the motor hall feedback wiring is not open/shorted/
missing
• Use shielded cables, route feedback away from potential noise
sources
• Check system grounds, replace the motor
Inverters
FLT S03 – MTR OVERSPEED FL - 0
Motor Overspeed
Factory Limit Fault
Motor speed has exceeded 125% of its
maximum speed.
Check control loop tuning.
Inverters
FLT S03 – MTR OVERSPEED FL - 1
The output frequency has exceeded 590
Hz.
• Check control loop tuning
• Reduce the velocity command
FLT S04 – MTR OVERSPEED UL
Motor Overspeed
User Limit Fault
Motor speed has exceeded motor
overspeed user limit.
• Check control loop tuning
• Increase the Motor Overspeed UL attribute value
Inverters
FLT S05 – MTR OVERTEMP FL nn
Motor Overtemperature
Factory Limit Fault
Calculations based on the motor
thermistor indicate that the motor
factory temperature limit has been
exceeded.
The nn sub-code is defined as follows:
01: Motor Thermostat or Thermistor
02: Encoder Temperature Sensor
• Operate motor within continuous torque rating
• Reduce motor ambient temperature
• Add motor cooling
Available only on Kinetix VP and MP-Series™ motors. Not supported
on induction motors.
Inverters
FLT S07 – MTR OVERLOAD FL
Motor Thermal Overload
Factory Limit Fault
The motor thermal model has exceeded
its factory set thermal capacity limit.
Modify the command profile to reduce speed or increase time.
Inverters
FLT S08 – MTR OVERLOAD UL
Motor Thermal Overload
User Limit Fault
The motor thermal model has exceeded
the thermal capacity limit given by Motor
Thermal Overload User Limit.
• Modify the command profile
• Increase the Motor Thermal Overload UL attribute value
Inverters