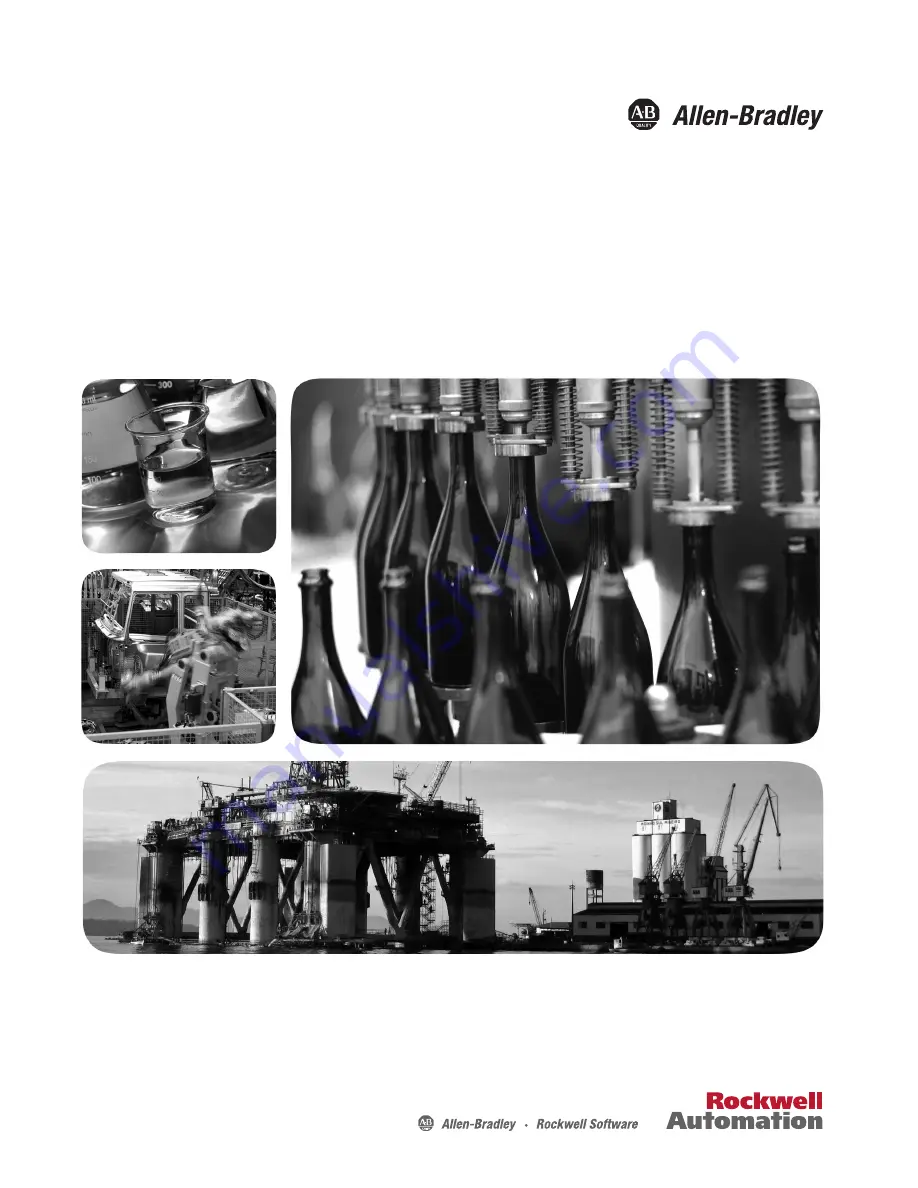
Kinetix 5700 Servo Drives
Catalog Numbers 2198-P031, 2198-P070, 2198-P141, 2198-P208, 2198-S086-ERS3, 2198-S130-ERS3, 2198-S160-ERS3,
2198-D006-ERS3, 2198-D012-ERS3, 2198-D020-ERS3, 2198-D032-ERS3, 2198-D057-ERS3, 2198-S086-ERS4,
2198-S130-ERS4, 2198-S160-ERS4, 2198-D006-ERS4, 2198-D012-ERS4, 2198-D020-ERS4, 2198-D032-ERS4,
2198-D057-ERS4, 2198T-W25K-ER, 2198-CAPMOD-2240, 2198-CAPMOD-DCBUS-IO
User Manual
Original Instructions