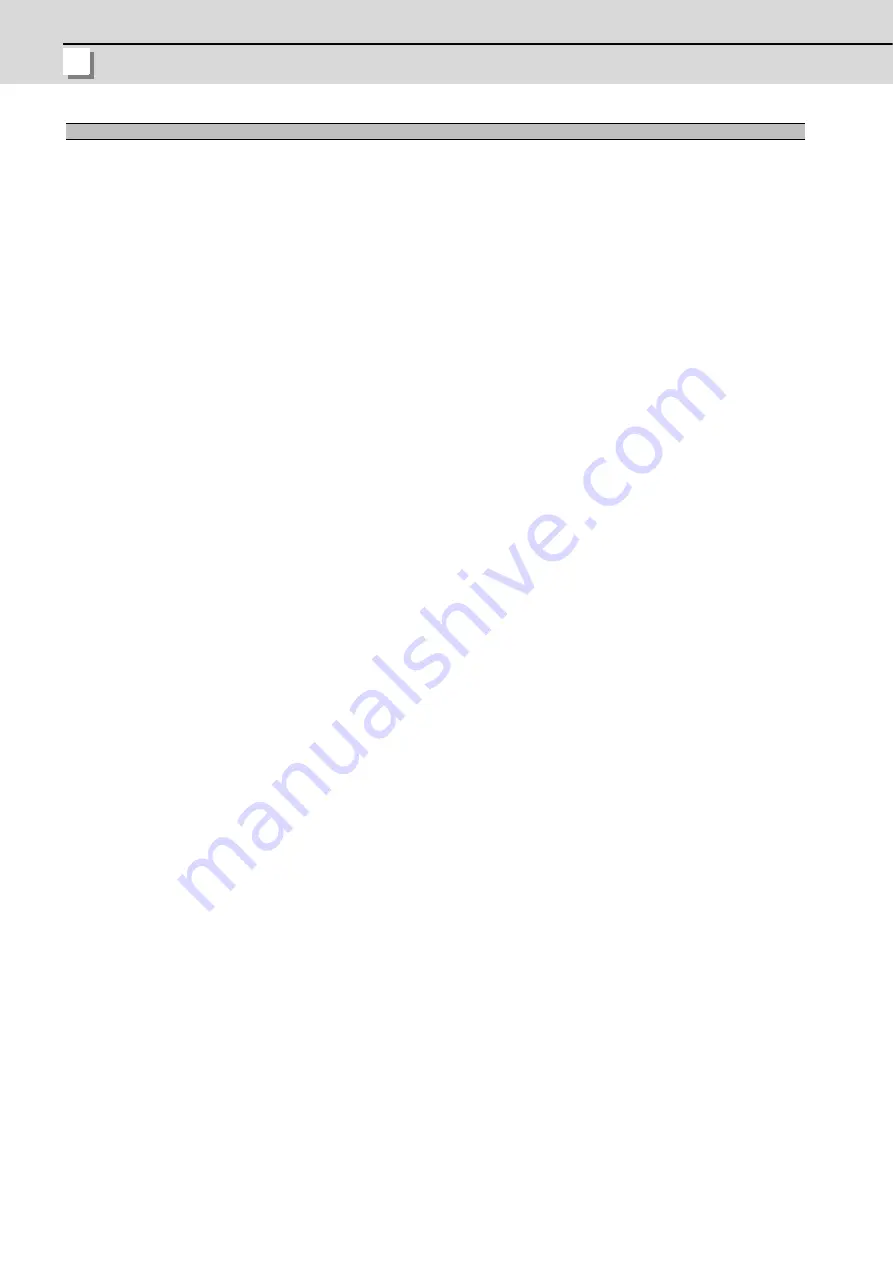
6 Maintenance Screens
MITSUBISHI CNC
I - 356
(1) Notes related to transferring in general
(a) Depending on the type of file, some data cannot be transferred during automatic operation. Do not transfer
during automatic operation.
(b) When the capacity of the transfer destination is reached during file transfer, only the data transferred up to that
point is registered as a file, and an error will result.
(c) During input to the NC memory or comparison, if the file format size on the NC memory side differs from the
other side file format size (when the maximum number of registrations differs between the NC memory and the
other side), processing is carried out matched to the smaller size.
(Ex. 1) If a format size of 200 files is input for a format size of 1000 NC files, 200 files are registered.
(Ex. 2) If a format size of1000 files is input for a format size of 200 NC files, the files up to the 200th file are
registered and an error message appears. (The remaining files are not registered.)
(2) Notes when transferring machining program files
(a) For the serial, always set feed (Null) at both ends of the "EOR" code at the head and end. If "EOB" etc., is
directly after "EOR", the operation may not execute normally due to the input buffer influence during the next
input operation.
(b) The transfer speed is slower if there are many registrations.
(c) The size of one block of the machining program should be 250 characters or less.
(d) The characters that can be used for the file name and directory path are 1-byte number, 1-byte capital
alphabetical letters, and 1-byte symbols recognized by the system.
Note that the following characters cannot be used.
|, /, :, "," (comma), *, ?, ", <, >, a to z (small letters), Space
Up to 32 characters are allowed for the file name to create in or transfer to NC memory.
(e) If the file whose name includes lower case alphabet is transferred to NC memory, the lower case letter will be
converted into the capital letter.
(f)
When using tape, carry out parity V adjustment to improve the reliability of the tape format. Then use with the
input/output parameter "Parity V" validated.
(g) When the machine tool builder macro and fixed cycle program are input to NC memory, change the program
type with the parameter "#1166 fixpro". Also, set in the Input/Output screen as follows.
Device: Memory, Directory: Program
(h) Transferring or verifying the multiple files between the external device connected serially and that other than
the serial connection.
(i)
With machining program created before the MELDAS500 Series, "EOB" is registered as "LF".
However, when these programs are stored in the E70 Series NC memory, "EOB" will be converted to "CR LF",
and the number of characters will increase. Thus, when all of the machining programs output from an
MELDAS500 Series or earlier NC, having the same specifications as the maximum memory capacity, are
stored in the E70 Series NC memory, the memory capacity may be exceeded.
(j)
When the file to be transferred (input) is running or in "program restarting" mode, "program checking", the
operation message "Executing automatic operation" or "Program restarting" or "Program checking" is
displayed and file will not be transferred (input).
(k) If the file to be transferred (input) is being edited in the custom screen, the operation message "Can't write into
being edited file" appears and may not be transferred (input).
(l)
When "#8936 Delete leading 0" is set to "1", the file consisting only of numerical figures will be transferred with
the "0" at the head deleted. Refer to "4.5.16 Leading Zero" for details.
(m) The transfer range from the external device other than serial to NC memory will change depending on the
value set in the user parameter "#19006 EOR Disable".
- When the user parameter "#19006 EOR Disable" is set to "0", the head line will not be transferred.
Up to "%" in the second line onward will be transferred, and data after "%" will not be transferred.
If there is no "%", all data will be transferred.
- When the user parameter "#19006 EOR Disable" is set to "1", all file contents will be transferred.
Notes
Summary of Contents for E70 Series
Page 1: ......
Page 3: ......
Page 9: ......
Page 11: ......
Page 13: ......
Page 15: ......
Page 24: ...I SCREEN OPERATIONS ...
Page 25: ......
Page 26: ...I 1 1 Operating the Setting and Display Unit ...
Page 57: ...1 Operating the Setting and Display Unit MITSUBISHI CNC I 32 ...
Page 58: ...I 33 2 Monitor Screens ...
Page 139: ...2 Monitor Screens MITSUBISHI CNC I 114 ...
Page 140: ...I 115 3 Setup Screens ...
Page 232: ...I 207 4 Edit Screens ...
Page 314: ...I 289 5 Diagnosis Screens ...
Page 355: ...5 Diagnosis Screens MITSUBISHI CNC I 330 ...
Page 356: ...I 331 6 Maintenance Screens ...
Page 436: ...II MACHINE OPERATIONS ...
Page 437: ......
Page 439: ...MITSUBISHI CNC II 2 ...
Page 440: ...II 3 1 Operation State ...
Page 444: ...II 7 2 Indicator Lamps ...
Page 446: ...II 9 3 Reset Switch and Emergency Stop Button ...
Page 448: ...II 11 4 Operation Mode ...
Page 456: ...II 19 5 Operation Panel Switches in Operation Mode ...
Page 460: ...II 23 6 Operation Panel Switch Functions ...
Page 495: ...6 Operation Panel Switch Functions MITSUBISHI CNC II 58 ...
Page 496: ...II 59 7 Other Functions ...
Page 509: ...7 Other Functions MITSUBISHI CNC II 72 ...
Page 510: ...III MAINTENANCE ...
Page 511: ......
Page 512: ...III 1 1 Daily Maintenance and Periodic Inspection and Maintenance ...
Page 515: ...1 Daily Maintenance and Periodic Inspection and Maintenance MITSUBISHI CNC III 4 ...
Page 516: ...III 5 2 Hardware Replacement Methods ...
Page 531: ...2 Hardware Replacement Methods MITSUBISHI CNC III 20 ...
Page 532: ...IV APPENDIXES ...
Page 533: ......
Page 534: ...IV 1 Appendix 1 List of Function Codes ...
Page 536: ...IV 3 Appendix 2 Table of Command Value Ranges ...
Page 543: ...Appendix 2 Table of Command Value Ranges MITSUBISHI CNC IV 10 ...
Page 544: ...IV 11 Appendix 3 Circular Cutting Radius Error ...
Page 546: ...IV 13 Appendix 4 Registering Editing the Fixed Cycle Program ...
Page 561: ...Appendix 4 Registering Editing the Fixed Cycle Program MITSUBISHI CNC IV 28 ...
Page 562: ...IV 29 Appendix 5 RS 232C I O Device Parameter Setting Examples ...
Page 564: ...IV 31 Appendix 6 Explanation of Alarms ...
Page 678: ...IV 145 Appendix 7 Operation Messages ...
Page 699: ...Appendix 7 Operation Messages MITSUBISHI CNC IV 166 ...
Page 700: ...IV 167 Appendix 8 User Parameters ...
Page 777: ...Appendix 8 User Parameters MITSUBISHI CNC IV 244 ...
Page 782: ......