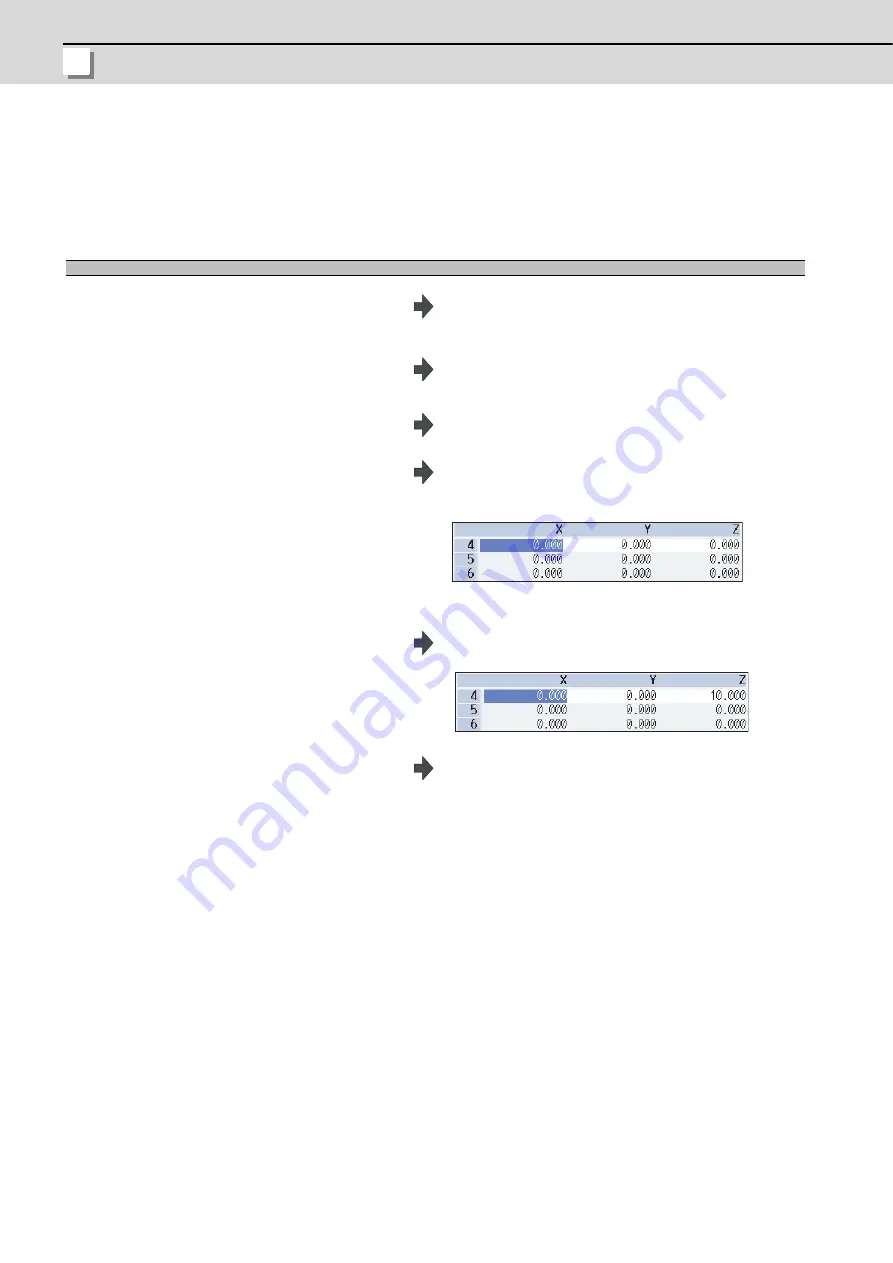
3 Setup Screens
MITSUBISHI CNC
I - 166
(Note 4) When the parameter "#1124 ofsfix" is "0", the cursor moves to the next offset No. However,when "#1124
ofsfix" is "1", the cursor does not move to the next offset No.
(Note 5) When the parameter "#11017 T-ofs set at run" is "1", the tool compensation amount data can be set even
during automatic operation or operation pause.
(Note 6) If the measurement result exceeds the setting range of the tool compensation amount, the operation message
"Setting error" will appear and the offset write cannot be executed.
(Note 1) When entering the sensor area, the axis can be moved only in one direction selected from +X, -X, +Z, -Z, (+Y,-
Y). If two axes are moved simultaneously, measurement will not be carried out. At this time, "TLM axis is
illegal" is displayed and the axis movement stops.
(Note 2) If the tool nose is contacting the sensor, the axis can be moved only in the direction moving away from the
sensor. Whether or not the tool nose is detached from the sensor can be judged by the following conditions.
- The sensor signal has been turned OFF for 500ms or more.
- The tool nose is moved 100
μ
m or more after the sensor signal has turned OFF.
The above conditions are set with parameter "#1227 aux11/bit2".
Carrying out tool measurement (Manual tool length measurement II)
(1)
Select the tool to be measured with manual
numerical value command. (Refer to "3.10 Manual
Numerical Value Command" for details.)
The tool to be measured is selected.
(2)
Set the offset No. of the compensation data to be set
in "Tool No. (Tool length measurement 2)" (PLC
device).
The offset No. of the compensation data to be set is selected.
(3)
Set the offset No. of the wear data to be cleared in
"wear offset No. (tool presetter)" (PLC device).
The offset No. of the wear data to be cleared is selected.
(4)
Turn the measurement switch ON.
"On meas" is displayed. Guide drawing for manual tool length
measurement II is displayed. Tool compensation data is
displayed, placing the offset No. set in "Tool No. (Tool length
measurement 2)" (PLC device) at the top.
(Note) The row at the cursor position will not be changed.
(5)
Move the additional axis in the minus direction by
manual feed and have the tool nose contact with the
touch sensor.
Measurement value is set for the additional axis of the offset
No. set in "Tool No. (Tool length measurement2)" (PLC device)
(6)
Turn the measurement switch OFF.
"On meas" disappears.
Summary of Contents for E70 Series
Page 1: ......
Page 3: ......
Page 9: ......
Page 11: ......
Page 13: ......
Page 15: ......
Page 24: ...I SCREEN OPERATIONS ...
Page 25: ......
Page 26: ...I 1 1 Operating the Setting and Display Unit ...
Page 57: ...1 Operating the Setting and Display Unit MITSUBISHI CNC I 32 ...
Page 58: ...I 33 2 Monitor Screens ...
Page 139: ...2 Monitor Screens MITSUBISHI CNC I 114 ...
Page 140: ...I 115 3 Setup Screens ...
Page 232: ...I 207 4 Edit Screens ...
Page 314: ...I 289 5 Diagnosis Screens ...
Page 355: ...5 Diagnosis Screens MITSUBISHI CNC I 330 ...
Page 356: ...I 331 6 Maintenance Screens ...
Page 436: ...II MACHINE OPERATIONS ...
Page 437: ......
Page 439: ...MITSUBISHI CNC II 2 ...
Page 440: ...II 3 1 Operation State ...
Page 444: ...II 7 2 Indicator Lamps ...
Page 446: ...II 9 3 Reset Switch and Emergency Stop Button ...
Page 448: ...II 11 4 Operation Mode ...
Page 456: ...II 19 5 Operation Panel Switches in Operation Mode ...
Page 460: ...II 23 6 Operation Panel Switch Functions ...
Page 495: ...6 Operation Panel Switch Functions MITSUBISHI CNC II 58 ...
Page 496: ...II 59 7 Other Functions ...
Page 509: ...7 Other Functions MITSUBISHI CNC II 72 ...
Page 510: ...III MAINTENANCE ...
Page 511: ......
Page 512: ...III 1 1 Daily Maintenance and Periodic Inspection and Maintenance ...
Page 515: ...1 Daily Maintenance and Periodic Inspection and Maintenance MITSUBISHI CNC III 4 ...
Page 516: ...III 5 2 Hardware Replacement Methods ...
Page 531: ...2 Hardware Replacement Methods MITSUBISHI CNC III 20 ...
Page 532: ...IV APPENDIXES ...
Page 533: ......
Page 534: ...IV 1 Appendix 1 List of Function Codes ...
Page 536: ...IV 3 Appendix 2 Table of Command Value Ranges ...
Page 543: ...Appendix 2 Table of Command Value Ranges MITSUBISHI CNC IV 10 ...
Page 544: ...IV 11 Appendix 3 Circular Cutting Radius Error ...
Page 546: ...IV 13 Appendix 4 Registering Editing the Fixed Cycle Program ...
Page 561: ...Appendix 4 Registering Editing the Fixed Cycle Program MITSUBISHI CNC IV 28 ...
Page 562: ...IV 29 Appendix 5 RS 232C I O Device Parameter Setting Examples ...
Page 564: ...IV 31 Appendix 6 Explanation of Alarms ...
Page 678: ...IV 145 Appendix 7 Operation Messages ...
Page 699: ...Appendix 7 Operation Messages MITSUBISHI CNC IV 166 ...
Page 700: ...IV 167 Appendix 8 User Parameters ...
Page 777: ...Appendix 8 User Parameters MITSUBISHI CNC IV 244 ...
Page 782: ......