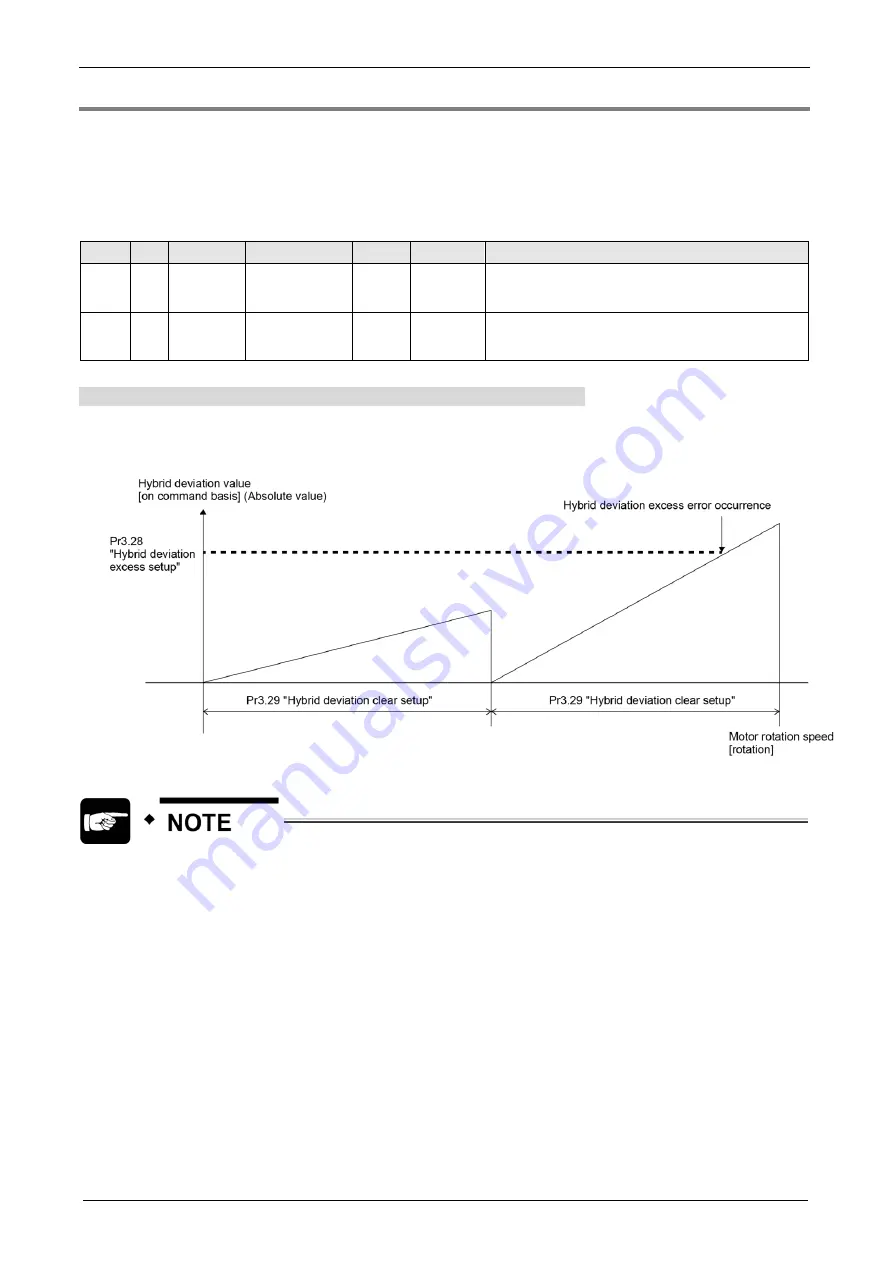
Basic Functions
4-22
4.5.3 Setting of hybrid deviation excess
The difference between the motor (encoder) position and load (external scale) position is detected, and
when the difference exceeds Pr3.28 "Hybrid deviation excess setup", the hybrid deviation excess error
protection is activated.
The hybrid deviation excess occurs mainly when there is an external scale error, external scale
connection fault, and motor-load connection looseness.
Relevant parameters
Class No. Attribute
Title
Range
Unit
Function
3
28
C
Hybrid deviation
excess setup
1 to 2
27
Command
unit
Sets the allowance (hybrid deviation) between the motor
(encoder) position and load (external scale) position on a
command basis.
3
29
C
Hybrid deviation
clear setup
0 to 100
Rotation
Each time the motor rotates for the amount of this set value,
the hybrid deviation is cleared to zero. When the set value
is zero, the hybrid deviation is not cleared.
Regarding hybrid deviation clear specification
Each time the motor rotates for the amount set with Pr3.29 "Hybrid deviation clear setup", the hybrid
deviation is cleared to zero. By this function, operation becomes possible even with uses with which an
accumulation of hybrid deviation occurs due to slippage or other reasons.
(Note) The rotation speed for hybrid deviation clear setting is detected by the use of encoder feedback pulse.
When using the hybrid deviation clear, make sure to set the Pr3.29 "Hybrid deviation clear
setup" to an appropriate value. If set to a significantly smaller value compared with the set
value of Pr3.28 "Hybrid deviation excess setup", this function may not work correctly as a
protection against an abnormal operation caused by improper connection of external scale
or others. When using, pay close attention to safety, and install a limit sensor or implement
other means.
Other than the above, hybrid deviation is cleared when the following position information is initialized:
When turning on the power of the absolute system
When establishing communication (when changing ESM state from Init to PreOP)
When completing returning to home
When completing the execution of the functions below by the setup support software (PANATERM for Multi
)
Test run function, Z phase search function, frequency response analyzing function (FFT), fit gain function, pin
assignment setting, multi-turn clearing of the absolute encoder
When Err27.4 (Command error protection) occurs
Summary of Contents for MINAS A6 Series
Page 10: ...Table of contents x Blank page...
Page 11: ...1 Introduction...
Page 26: ...Introduction 1 16 Blank page...
Page 27: ...2 Interface Specifications...
Page 46: ...Interface Specifications 2 20 Blank page...
Page 47: ...3 Front Panel Specifications...
Page 57: ...4 Basic Functions...
Page 85: ...5 Auto Tuning Functions...
Page 151: ...6 Application Functions...
Page 185: ...7 Protective Functions...
Page 224: ...Protective Functions 7 40 Blank page...
Page 225: ...8 Advanced Safety Functions...
Page 230: ...Advanced Safety Functions 8 6 When test pulse is used Duplex safety input Safety input...
Page 245: ...9 List of Parameters...
Page 281: ...10 Timing Chart...
Page 290: ...Timing Chart 10 10 Blank page...
Page 291: ...11 Power Supply Module...