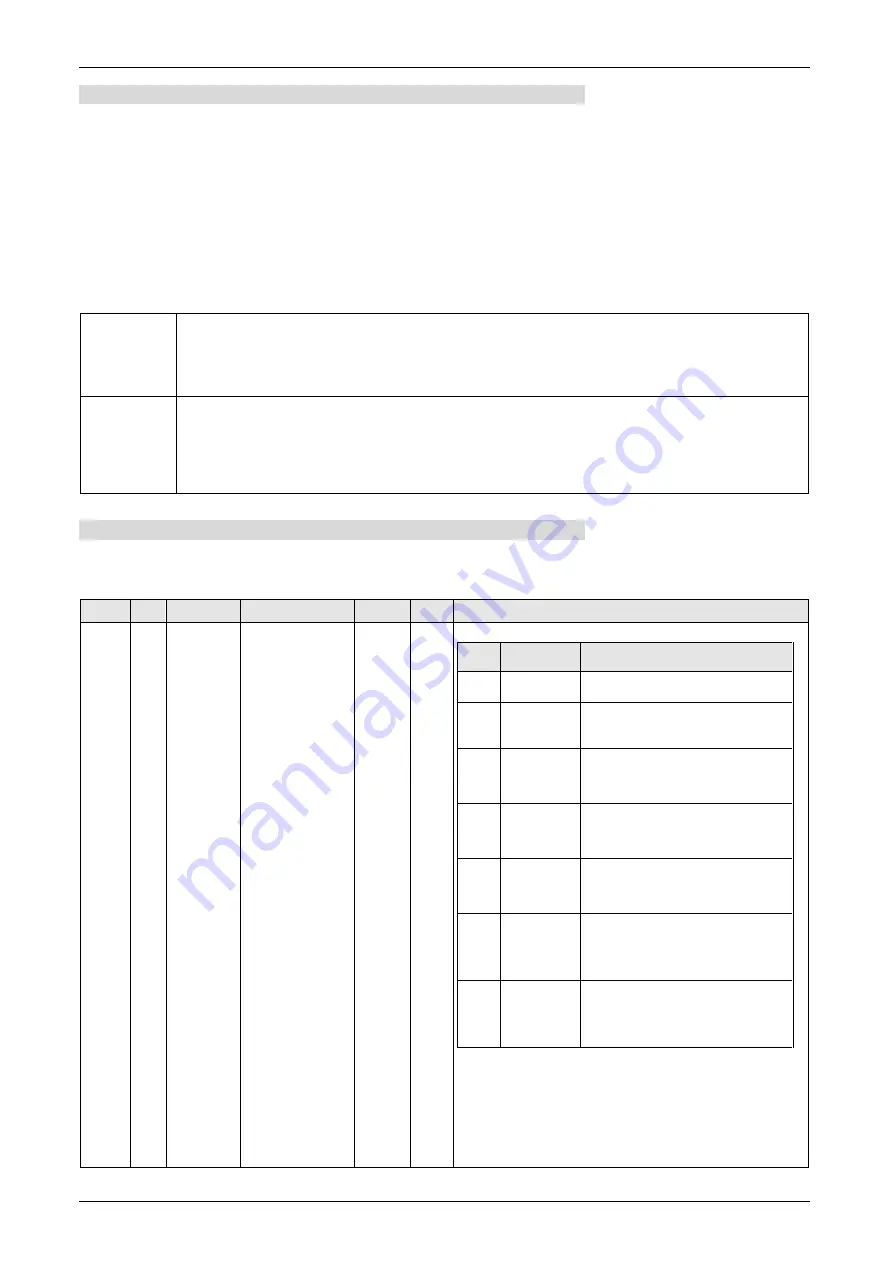
5.1Automatic adjusting function
5-3
Caution
After the power is turned on, estimate value following may become quicker regardless of Pr6.31 "Real time
auto tuning estimation speed" until operation data effective for the estimation of load characteristics is
sufficiently accumulated.
When real-time auto-gain tuning is effective, an estimate value may become abnormal due to disturbance. If
you want to obtain stable operation from when the power is turned on, it is recommended to disable the
real-time auto-gain tuning.
Real-time auto-gain tuning may not be executed properly under the conditions described below. If not
properly executed, change the loading condition or operating pattern, or manually set up the relevant
parameters by referring to the manual adjustment function description.
Conditions which obstruct Real-time auto-gain tuning action:
Load inertia
The load inertia is too small or large compared to the rotor inertia. (less than 3 times or more than 20 times).
The load inertia changes too quickly.
The machine stiffness is extremely low.
Nonlinear characteristics such as backlash exist.
Action pattern
The motor is running continuously at low speed of 100 [r/min] or lower.
Acceleration/deceleration is slow (2,000 [r/min] per 1 [s] or low).
When the speed condition of 100 [r/min] or more and acceleration/deceleration condition of 2,000 [r/min] per 1 [s]
are not maintained for 50 [ms].
Acceleration/deceleration torque is smaller than unbalanced weighted/viscous friction torque.
Real-time auto tuning control parameters
Use the following parameters to set up the operation of Real-time auto tuning.
Relevant parameters
Class No. Attribute
Title
Range Unit Function
0
02
B
Real-time auto-gain
tuning setup
0 to 6
-
You can set up the action mode of the real-time auto-gain tuning.
Setup
value
Mode
Description
0
Invalid
Real-time auto-gain tuning function is
disabled.
1
Standard
Stability-sensitive mode.
Do not use unbalanced load, friction
compensation or gain switching.
2
Positioning *1
Position-sensitive mode. Use this mode for
machine using horizontal axis without offset
load or ball screw driven machine with small
friction.
3
Vertical axis *2 This mode adds the following features to
those of positioning mode: compensates for
offset load in vertical axis and minimizes
positioning settling time variations.
4
Friction
compensation
*3
This mode adds the following features to
those of vertical axis mode: shortens
positioning settling time on large friction
system such as belt driven axis.
5
Load
characteristic
measurement
This mode only estimates the load
characteristics without changing the basic
gain setting or friction compensation setting.
Use these features in conjunction with the
setup support software.
6
Customize *4
By precisely setting combination of real-time
auto tuning functions through Pr 6.32 Real
time auto tuning custom setup,
customization to fit the application can be
made.
*1 Velocity and torque controls are the same as in the standard
mode.
*2 Torque control is the same as in the standard mode.
*3 Velocity control is the same as in the vertical axis mode.
Torque control is the same as in the standard mode.
*4 Certain function(s) is not available in a specific control mode.
Refer to description in Pr 6.32.
(To be continued)
Summary of Contents for MINAS A6 Series
Page 10: ...Table of contents x Blank page...
Page 11: ...1 Introduction...
Page 26: ...Introduction 1 16 Blank page...
Page 27: ...2 Interface Specifications...
Page 46: ...Interface Specifications 2 20 Blank page...
Page 47: ...3 Front Panel Specifications...
Page 57: ...4 Basic Functions...
Page 85: ...5 Auto Tuning Functions...
Page 151: ...6 Application Functions...
Page 185: ...7 Protective Functions...
Page 224: ...Protective Functions 7 40 Blank page...
Page 225: ...8 Advanced Safety Functions...
Page 230: ...Advanced Safety Functions 8 6 When test pulse is used Duplex safety input Safety input...
Page 245: ...9 List of Parameters...
Page 281: ...10 Timing Chart...
Page 290: ...Timing Chart 10 10 Blank page...
Page 291: ...11 Power Supply Module...