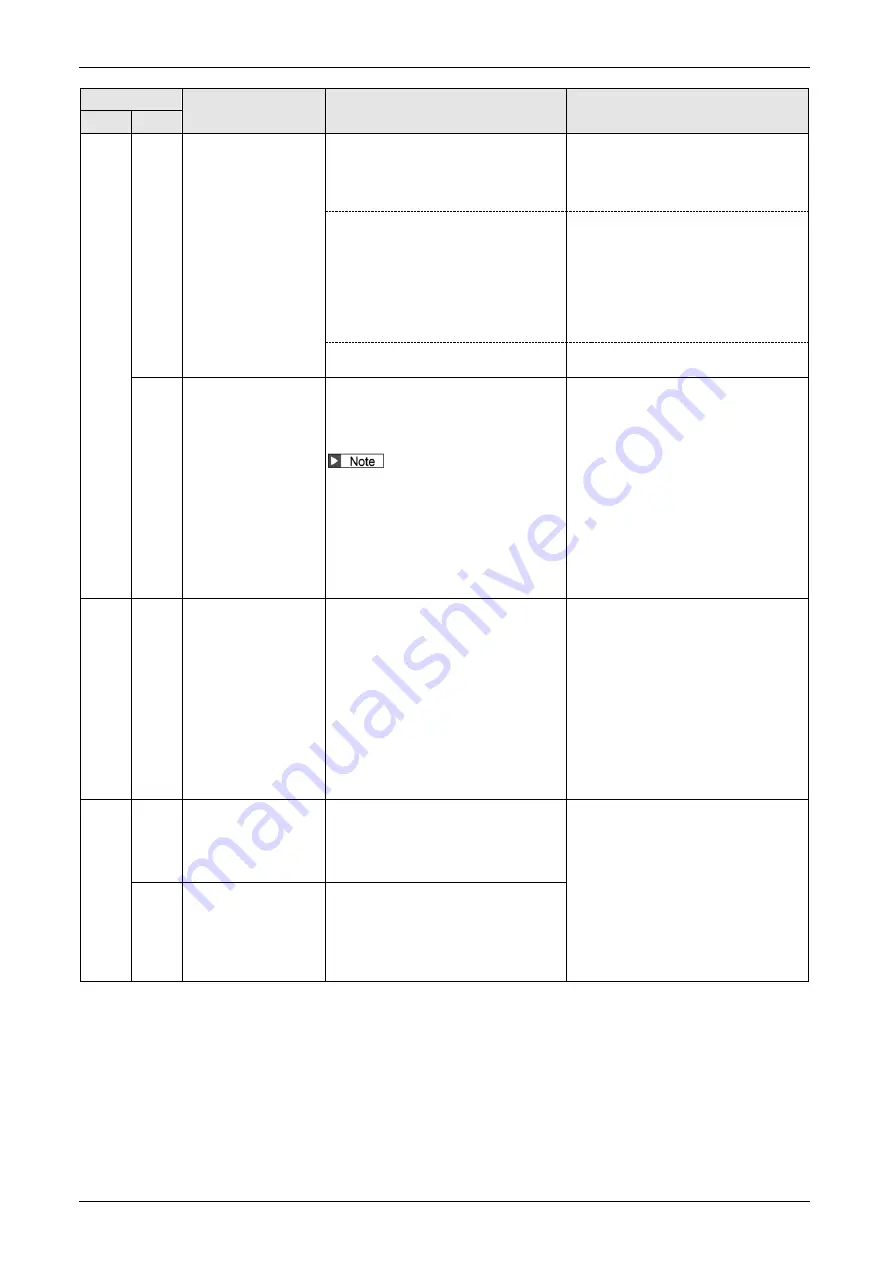
7.2Details of protective function
7-11
Error No.
Protective function
Causes
Measures
Main
Sub
24
0
Position deviation excess
protection
In the driver module, the position deviation
pulse of each axis exceeds the setting of Pr
0.14 “Position deviation excess setup”.
Remove the cause of excessive position
deviation.
Alternatively, the positional deviation
excess determination threshold value is
increased.
1) The motor movement has not followed
the command.
1) Check that the motor follows to the
position command pulses. Check that
the output toque has not saturated in
torque monitor. Make a gain
adjustment. Set up maximum value to
Pr 0.13 and Pr 5.22. Make a encoder
wiring as per the wiring diagram. Set
up the longer acceleration/deceleration
time. Lower the load and speed.
2)
Setup value of Pr 0.14 “Position
deviation excess setu
p) is small”.
2) Set up a larger value to Pr 0.14.
1
Speed deviation excess
protection
In the driver module, the difference between
the internal positional command speed and
actual speed (speed deviation) exceeds the
setup vale of Pr 6.02 ”Speed deviation
excess setup”.
If the internal positional command speed is
forcibly set to 0 due to instantaneous stop
caused by the positive/negative over-travel
inhibit input, the speed deviation rapidly
increases at this moment. Pr 6.02 setup
value should have sufficient margin
because the speed deviation also largely
increases on the rising edge of the internal
positional command speed.
Remove the cause of excessive speed
deviation.
Alternatively, the speed deviation excess
determination threshold is increased.
Increase the setup value of Pr 6.02.
Lengthen the acceleration/deceleration
time of internal positional command
speed, or improve the follow-up
characteristic by adjusting the gain.
Disable the excess speed deviation
detection (Pr 6.02 = 0).
25
0
Hybrid deviation excess
error protection
In the driver module, the load position of the
external scale and the motor position of the
encoder on the full-closed control axis
deviated by more than the number of pulses
set in Pr 3.28 “Hybrid deviation excess
setup”.
Check the connection between the motor
and the load.
Check the connection between the
external scale and the driver module.
Check that the variation of the motor
position (encoder feedback value) and the
load position (external scale feedback
value) is the same sign when you move
the load.
Check that the numerator and
denominator of the external scale division
(Pr 3.24 and 3.25) and reversal of external
scale direction (Pr 3.26) are correctly set.
26
0
Over-speed protection
In the driver module, each motor rotational
speed has exceeded the setup value of Pr
5.13 ” Over-speed level setup”.
Reduce motor speed.
Do not give an excessive speed
command.
Check the electronic gear ratio.
Make a gain adjustment when an
overshoot has occurred due to a poor gain
adjustment.
To take measures against noise for the
1st encoder communication, the same
measures as Er21.1 and Err23.0 are
taken.
1
2nd over-speed
protection
In the driver module, each motor rotational
speed has exceeded the setup value of Pr
6.15 ” 2nd over-speed level setup”.
(To be continued)
Summary of Contents for MINAS A6 Series
Page 10: ...Table of contents x Blank page...
Page 11: ...1 Introduction...
Page 26: ...Introduction 1 16 Blank page...
Page 27: ...2 Interface Specifications...
Page 46: ...Interface Specifications 2 20 Blank page...
Page 47: ...3 Front Panel Specifications...
Page 57: ...4 Basic Functions...
Page 85: ...5 Auto Tuning Functions...
Page 151: ...6 Application Functions...
Page 185: ...7 Protective Functions...
Page 224: ...Protective Functions 7 40 Blank page...
Page 225: ...8 Advanced Safety Functions...
Page 230: ...Advanced Safety Functions 8 6 When test pulse is used Duplex safety input Safety input...
Page 245: ...9 List of Parameters...
Page 281: ...10 Timing Chart...
Page 290: ...Timing Chart 10 10 Blank page...
Page 291: ...11 Power Supply Module...