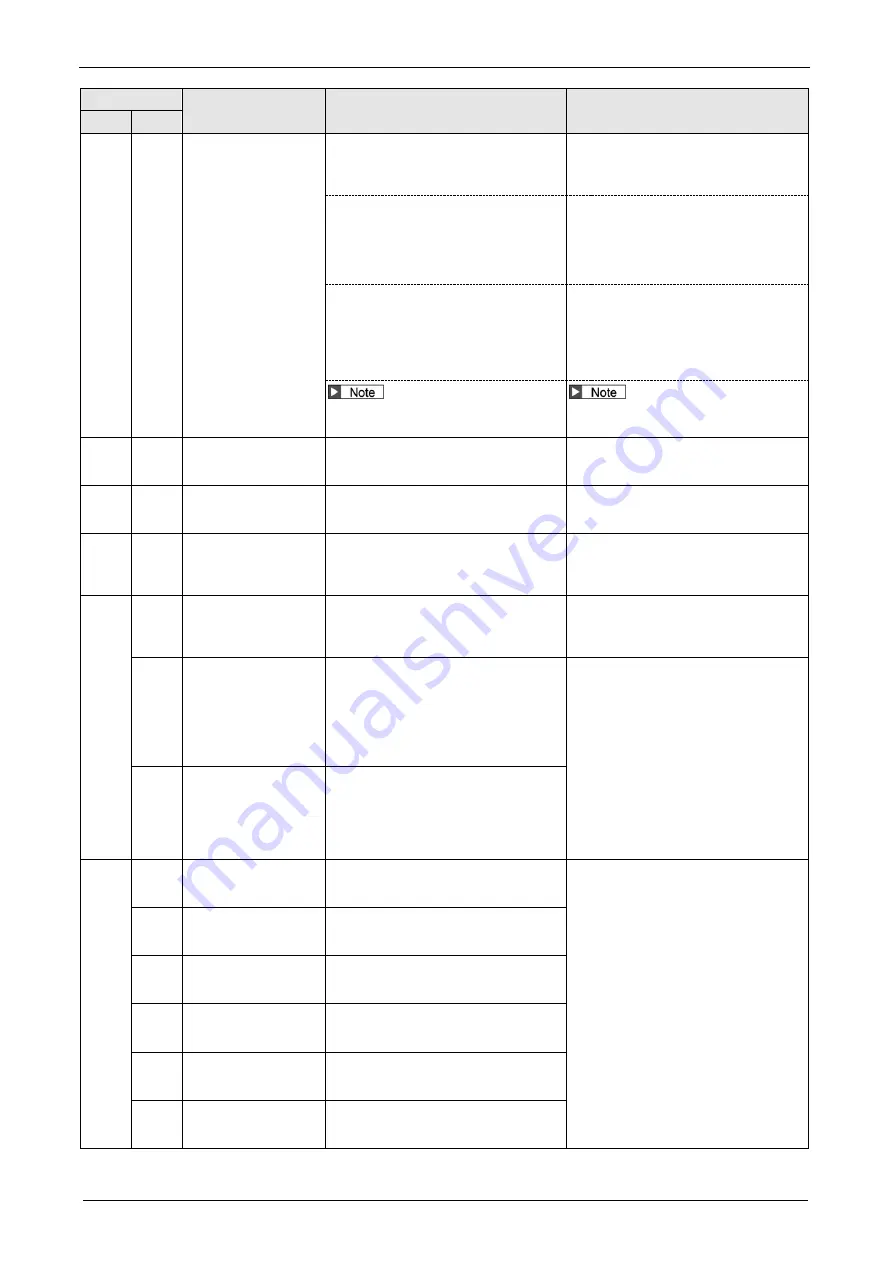
Protective Functions
7-16
Error No.
Protective function
Causes
Measures
Main
Sub
42
0
Absolute over-speed
error protection
In the driver module, the following situation
occurred when Pr0.15 “Absolute encoder
setting” = 0, 2, 6 for each axis.
Prevent the motor from moving at high
speed in the battery backup state. It was
shut off and the motor speed exceeded the
specified value.
1) The motor speed of the 1st encoder of
each axis is reduced when only the
battery power is supplied in the event of
a power failure while the driver module
control power is OFF.
The specified value was exceeded.
1) Check if there is any external drive
during a power failure and the motor
speed at that time, and operate so as to
be less than the specified value.
2) After turning on the driver module
control power, the 1st encoder power
was OFF during normal operation, and
the rotation speed exceeded the
specified value.
2) Do not switch to power failure mode
during normal operation.
Check the power supply voltage (5V ±
5%) on the encoder side.
Check the connection status of the 1st
encoder connector X9.
This does not occur with a batteryless
absolute encoder.
The alarm of driver module cannot be
cleared until the absolute encoder is reset..
44
0
Absolute single turn
counter error protection
In the driver module, single turn counter
error of each axis 1st encoder has been
detected.
Replace the motor.
45
0
Absolute multi-turn
counter error protection
In the driver module, multi turn counter error
of each axis 1st encoder has been
detected.
Replace the motor.
47
0
Absolute status error
protection
When the driver module control power was
power on, each axis 1st encoder has been
running at faster speed than the specified
value.
Arrange so as the motor does not run at
power-on.
50
0
External scale
connection error
protection
Communication between the external scale
and the driver module has been interrupted
in certain times, and disconnection
detecting function has been triggered.
Make a wiring connection of the external
scale as per the wiring diagram.
Correct the miswiring of the connector pins.
1
External scale
communication error
protection
The driver module received communication
data from the 2nd encoder of each axis
(external scale, etc.), but an error was
detected by the format check.
The data error mainly due to noise.
The 2nd encoder line is connected but the
communication data had some error.
Secure the power supply for the 2nd
encoder (the external scale) of 5 VDC
±5% (4.75 to 5.25 V) ... pay attention
especially when the external scale cables
are long.
Separate the external scale cable and the
motor cable if they are bound together.
Connect the shield to FG...refer to wiring
diagram of external scale in
"REFERENCE SPECIFICATIONS Driver
module section (SX-DSV03454)".
Replace the external scale.
2
External scale
communication data
error protection
The driver module received communication
data from the 2nd encoder of each axis
(external scale, etc.), and the format check
was not error, but an error was detected in
the contents of the communication data.
The data error mainly due to noise.
51
0
External scale status
error protection 0
In the driver module, Bit 0 of each axis 2nd
encoder (external scale, etc.) error code
(ALMC) has been turned to 1.
Check the external scale specifications, and
after removing the cause of the error, clear
the 2nd encoder (external scale, etc.) error.
And then, shut off the power to reset.
1
External scale status
error protection 1
In the driver module, Bit 1 of each axis 2nd
encoder (external scale, etc.) error code
(ALMC) has been turned to 1.
2
External scale status
error protection 2
In the driver module, Bit 2 of each axis 2nd
encoder (external scale, etc.) error code
(ALMC) has been turned to 1.
3
External scale status
error protection 3
In the driver module, Bit 3 of each axis 2nd
encoder (external scale, etc.) error code
(ALMC) has been turned to 1.
4
External scale status
error protection 4
In the driver module, Bit 4 of each axis 2nd
encoder (external scale, etc.) error code
(ALMC) has been turned to 1.
5
External scale status
error protection 5
In the driver module, Bit 5 of each axis 2nd
encoder (external scale, etc.) error code
(ALMC) has been turned to 1.
(To be continued)
Summary of Contents for MINAS A6 Series
Page 10: ...Table of contents x Blank page...
Page 11: ...1 Introduction...
Page 26: ...Introduction 1 16 Blank page...
Page 27: ...2 Interface Specifications...
Page 46: ...Interface Specifications 2 20 Blank page...
Page 47: ...3 Front Panel Specifications...
Page 57: ...4 Basic Functions...
Page 85: ...5 Auto Tuning Functions...
Page 151: ...6 Application Functions...
Page 185: ...7 Protective Functions...
Page 224: ...Protective Functions 7 40 Blank page...
Page 225: ...8 Advanced Safety Functions...
Page 230: ...Advanced Safety Functions 8 6 When test pulse is used Duplex safety input Safety input...
Page 245: ...9 List of Parameters...
Page 281: ...10 Timing Chart...
Page 290: ...Timing Chart 10 10 Blank page...
Page 291: ...11 Power Supply Module...