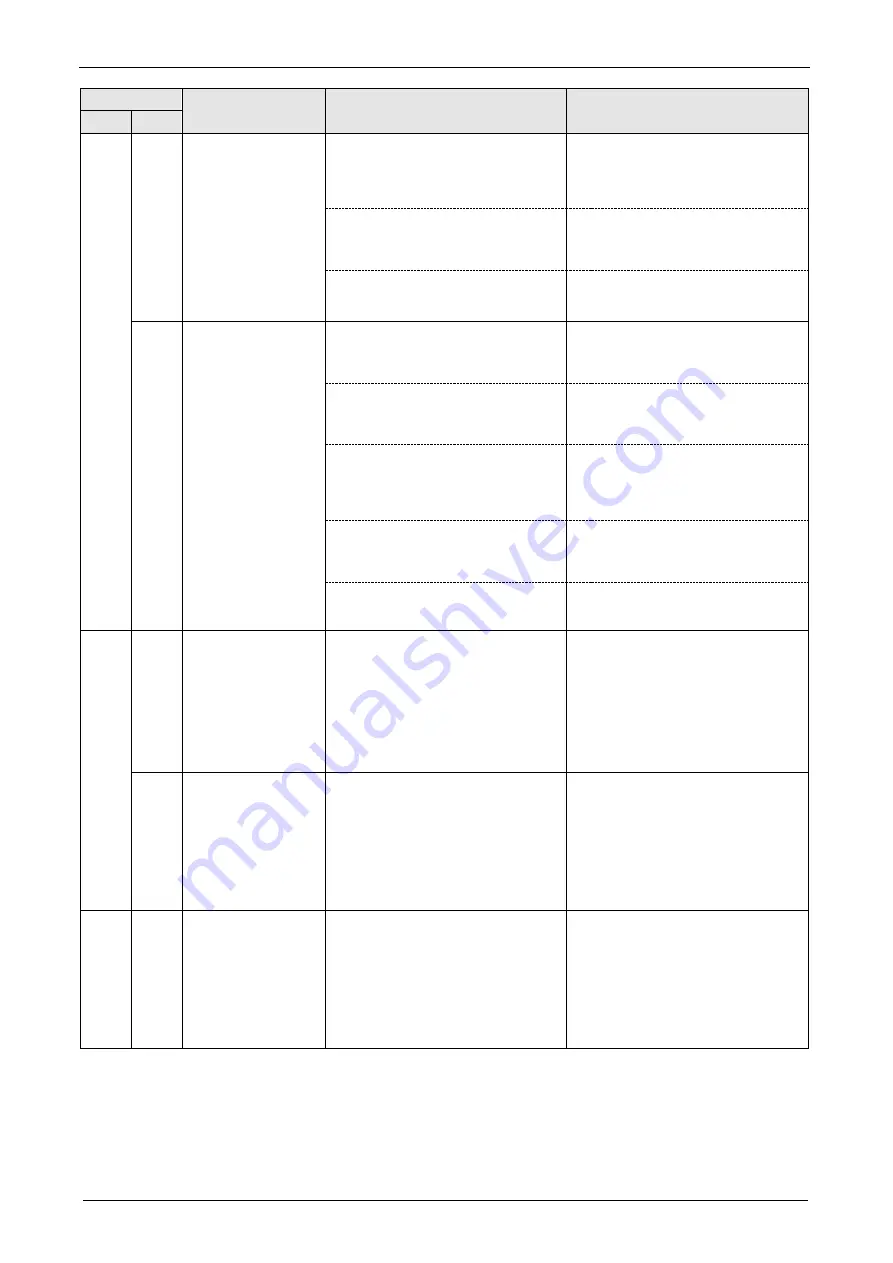
Protective Functions
7-10
Error No.
Protective function
Causes
Measures
Main
Sub
17
0
Mechanical brake circuit
voltage error protection
The power supply input voltage to the
mechanical brake output circuit of the motor
connector X105 of each axis built in the
driver module is smaller than the specified
value or larger than the specified value
When not using the mechanical brake, set
bit 0 (mechanical brake circuit voltage error
protection function) of Pr5.90 “ Function
extended shared setup 3
” to 1: Disabled.
1) The input voltage of the control power
supply exceeded the specified value.
1) Check the input voltage between the
terminals of the control power supply
and set it to the specified value. Then
clear the alarm.
2) Failure of driver module.
(Failure of mechanical brake output
circuit.)
2) Replace the driver module.
1
Mechanical brake circuit
overload protection
Excessive current flowed into the
mechanical brake output circuit of the motor
connector X105 of each axis built in the
driver module.
Check the wiring of the external mechanical
brake and mechanical brake output.
1) The BRK + and BRK- terminals of motor
connector X105 Short circuited.
1) Check the connector lead wires to see if
BRK + and BRK- of motor connector
X105 are short-circuited. Connect the
motor wires correctly.
2) BRK + and BRK- terminals of motor
connector X105 Ground fault.
2) Check the insulation resistance
between BRK + and BRK- of motor
connector X105 and the ground wire. If
insulation failure has occurred, replace
the driver module.
3) BRK + and BRK- terminals of motor
connector X105
Contact failure occurred.
3) Remove the BRK + and BRK- terminals
of motor connector X105.
Check and if it is loose or missing, fix it
securely.
4) Failure of driver module.
(Failure of mechanical brake output
circuit.)
4) Replace the driver module.
21
0
Encoder communication
disconnection error
protection
In the driver module, the data received from
the 1st encoder for each axis was
interrupted a certain number of times.
Check if the 1st encoder connector X9 is
connected correctly.
Correctly wire the 1st encoder cable.
Correct the connection error of the
connector pin.
To take measures against noise, take the
same measures as Err21.1 and Err23.0.
Replace the motor (failure of the encoder).
1
Encoder communication
error protection
The driver module received the data
received from the 1st encoder of each axis,
but an error was detected by the format
check.
Data error mainly due to noise. The 1st
encoder line is connected but the received
data is error.
Secure the power supply for the encoder
of 5 VDC ±5% (4.75 to 5.25 V) ... pay an
attention especially when the encoder
cables are long.
Separate the encoder cable and the motor
cable if they are bound together.
Connect the shield to FG.
Replace the motor (failure of the encoder).
23
0
Encoder communication
data error protection
The driver module received the data
received from the 1st encoder of each axis
and the format check was normal, but an
error was detected in the content of the
received data.
Data error mainly due to noise
Secure the power supply for the encoder
of 5 VDC ±5% (4.75 to 5.25 V) ... pay an
attention especially when the encoder
cables are long.
Separate the encoder cable and the motor
cable if they are bound together.
Connect the shield to FG.
Replace the motor (failure of the encoder).
(To be continued)
Summary of Contents for MINAS A6 Series
Page 10: ...Table of contents x Blank page...
Page 11: ...1 Introduction...
Page 26: ...Introduction 1 16 Blank page...
Page 27: ...2 Interface Specifications...
Page 46: ...Interface Specifications 2 20 Blank page...
Page 47: ...3 Front Panel Specifications...
Page 57: ...4 Basic Functions...
Page 85: ...5 Auto Tuning Functions...
Page 151: ...6 Application Functions...
Page 185: ...7 Protective Functions...
Page 224: ...Protective Functions 7 40 Blank page...
Page 225: ...8 Advanced Safety Functions...
Page 230: ...Advanced Safety Functions 8 6 When test pulse is used Duplex safety input Safety input...
Page 245: ...9 List of Parameters...
Page 281: ...10 Timing Chart...
Page 290: ...Timing Chart 10 10 Blank page...
Page 291: ...11 Power Supply Module...