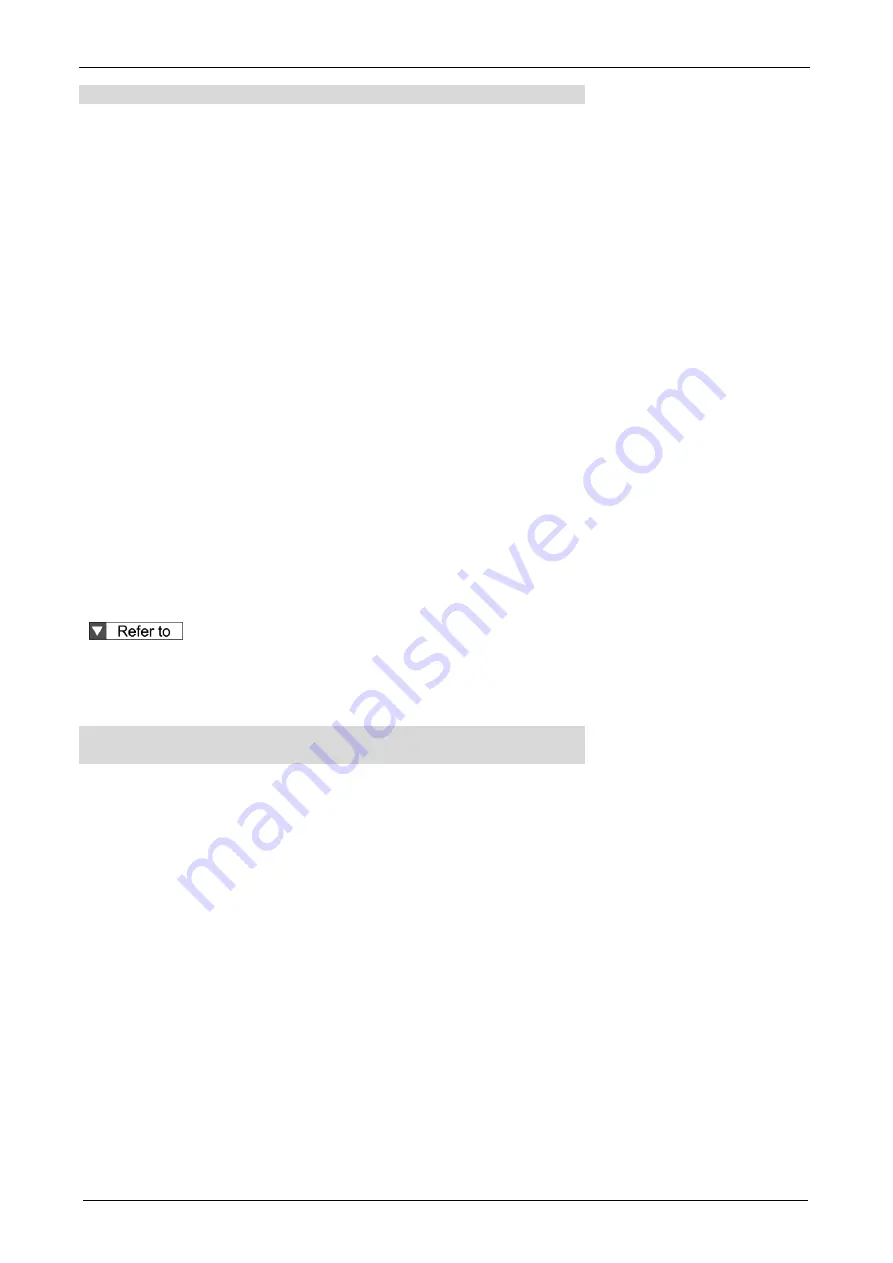
Interface Specifications
2-12
Cautions for input signal assignment
Do not setup to a value other than that specified in the table.
The same sign
al can’t be assigned to multiple pins. Otherwise, duplicated assignment will cause Err 33.0
"Input multiple assignment error 1 protection" or Err 33.1 "Input multiple assignment error 2 protection".
A signal used in multiple control modes should be assigned to the same pin and the logic should be matched.
If not assigned to the same pin, the Err33.0 "Input duplicate assignment error 1 protection" or Err33.1 "Input
duplicate assignment error 2 protection" occurs. In case that the logics do not match, Err33.2 "Input function
number error 1 protection" or Err33.3 "Input function number error 2 protection" will occur.
The duplicated assignment of SI-MON1 and EXT1, SI-MON2 and EXT2, SI-MON3 and EXT3, and SI-MON5
and E-STOP is not allowed. Duplicate assignment will cause Err33.0 "Input duplicate assignment error 1
protection" or Err33.1 "Input duplicate assignment error 2 protection".
A-CLR can only be set at a-connect. If set at b-connect, then Err33.2 "Input function number assignment
error 1 protection" or Err33.3 "Input function number assignment error 2 protection" will occur.
Depending on the operating status of the driver module, the control mode may be forcibly switched inside the
driver module regardless of commands from the host device. This operation has an effect on input signal
processing. Basically, assign the same function to one terminal in all control modes.
[Conditions that the control mode is switched forcibly inside the driver]
-
When the frequency characteristic is measured by setup support software PANATERM for Multi.
(Position loop characteristics mode is position control, the speed closed loop characteristic mode and
torque speed (vertical) mode are speed control, torque speed (normal) mode is torque control.)
-
Test run of the setup support software (Forcibly position control).
-
The states that are written "Forcibly position control" in Section "6.3 Deceleration stop sequence".
-
During retracting operation function (Forcibly position control) (Not supported)
Setting is required for all control modes after setting Pr6.36 "Dynamic brake operation input setup" to 1, in
case of using dynamic brake switching input (DB-SEL). In case only one or two control modes are set, either
Err33.2 "Input function number error 1" or Err33.3 "Input function number error 2" will occur.
Please refer to "6.3.3 Sequence at main power OFF" for details.
Inputs to the axis which is set as invalid in Pr0.20
“ Axis limit setting” will be fixed to OFF regardless of the
assignment setting.
Cautions for latch correction pins
(Axis A: SI5/SI6/SI7, Axis B: SI1/SI2/SI3)
External latch inputs EXT1 and EXT2 can be assigned only to SI5 and SI6 for Axis A, and to SI1 and SI2 for
Axis B as shown in the figure below. Wrong allocation will cause Err33.8 "Latch input allocation error
protection". For this reason, Err33.8 occurs even if EXT1 or EXT2 are set to input to both Axis A and Axis B.
When HOME/POT/NOT is used as the home reference trigger in the return to home position operation, it can
only be assigned to SI5, SI6, or SI7 for Axis A, and to SI1, SI2, or SI3 for Axis B as shown in the figure below.
Err33.8 "Latch input allocation error protection" will occur if it is assigned to any other input.
When using POT/NOT as the home reference trigger in the return to home position operation, set Pr5.04 to
1. If Pr5.04 is not 1, Err38.2 "Over-travel inhibit input protection 3" occurs.
*) When using POT/NOT with Pr 5.04 not = 1, set SI2, SI3 and SI6, SI7 from the factory setting as shown in
the table below. Also, connect the sensors to SI2 and SI3 on Axis A and SI6 and SI7 to Axis B.
Summary of Contents for MINAS A6 Series
Page 10: ...Table of contents x Blank page...
Page 11: ...1 Introduction...
Page 26: ...Introduction 1 16 Blank page...
Page 27: ...2 Interface Specifications...
Page 46: ...Interface Specifications 2 20 Blank page...
Page 47: ...3 Front Panel Specifications...
Page 57: ...4 Basic Functions...
Page 85: ...5 Auto Tuning Functions...
Page 151: ...6 Application Functions...
Page 185: ...7 Protective Functions...
Page 224: ...Protective Functions 7 40 Blank page...
Page 225: ...8 Advanced Safety Functions...
Page 230: ...Advanced Safety Functions 8 6 When test pulse is used Duplex safety input Safety input...
Page 245: ...9 List of Parameters...
Page 281: ...10 Timing Chart...
Page 290: ...Timing Chart 10 10 Blank page...
Page 291: ...11 Power Supply Module...