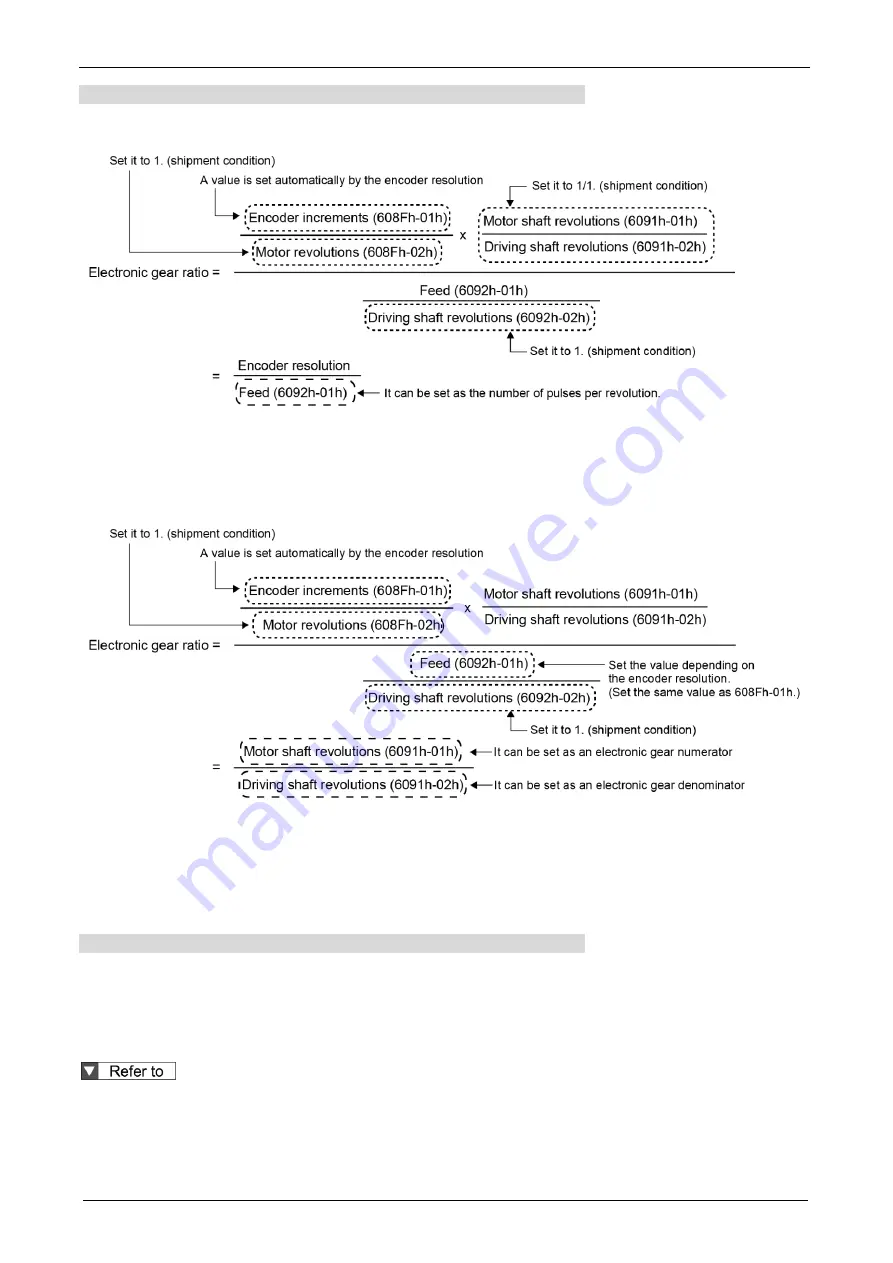
Basic Functions
4-6
Electronic gear setting example
Under semi-closed control, When setting the electronic gear ratio of axis A by setting the number
of command pulses per motor revolution
608Fh-01h (Encoder increments) is set automatically from the connected encoder resolution.
By setting 608Fh-02h (Motor revolutions), 6091h-01h (Motor shaft revolutions), 6091h-02h (Driving shaft
revolutions) and 6092h-02h (Driving shaft revolutions) to 1 (shipment condition), it is possible to set
6092h-01h (Feed) as the "number of command pulses per motor revolution".
Under semi-closed control or full-closed control, When setting the electronic gear ratio of axis A by
setting the electronic gear numerator/denominator
608Fh-01h (Encoder increments) is set automatically from the connected encoder resolution.
By setting 6092h-01h (Feed) to the encoder resolution (the same value as 608F-01h (Encoder increments),
and in the case of the 23bit/r encoder, the shipment condition) and setting 608Fh-02h (Motor revolutions) and
6092h-02h (Driving shaft revolutions) to 1 (shipment condition), it is possible to set 6091h-01h (Motor shaft
revolutions) to the "electronic gear numerator" and 6091h-02h (Driving shaft revolutions) to the "electronic
gear denominator".
Backup of electronic gear set value
The electronic-gear-related objects (6091h/6891h-01h, 6091h/6891h-02h, 6092h/6892h-01h and
6092h/6892h-02h) are backup target objects.
It is recommended to execute a backup (writing into EEPROM) after a change.
By executing a backup, it will be unnecessary to change setting each time when the control power is turned
on.
As for the backup method, refer to "TECHNICAL REFERENCE EtherCAT Communication Specification
(SX-DSV03456)".
Summary of Contents for MINAS A6 Series
Page 10: ...Table of contents x Blank page...
Page 11: ...1 Introduction...
Page 26: ...Introduction 1 16 Blank page...
Page 27: ...2 Interface Specifications...
Page 46: ...Interface Specifications 2 20 Blank page...
Page 47: ...3 Front Panel Specifications...
Page 57: ...4 Basic Functions...
Page 85: ...5 Auto Tuning Functions...
Page 151: ...6 Application Functions...
Page 185: ...7 Protective Functions...
Page 224: ...Protective Functions 7 40 Blank page...
Page 225: ...8 Advanced Safety Functions...
Page 230: ...Advanced Safety Functions 8 6 When test pulse is used Duplex safety input Safety input...
Page 245: ...9 List of Parameters...
Page 281: ...10 Timing Chart...
Page 290: ...Timing Chart 10 10 Blank page...
Page 291: ...11 Power Supply Module...