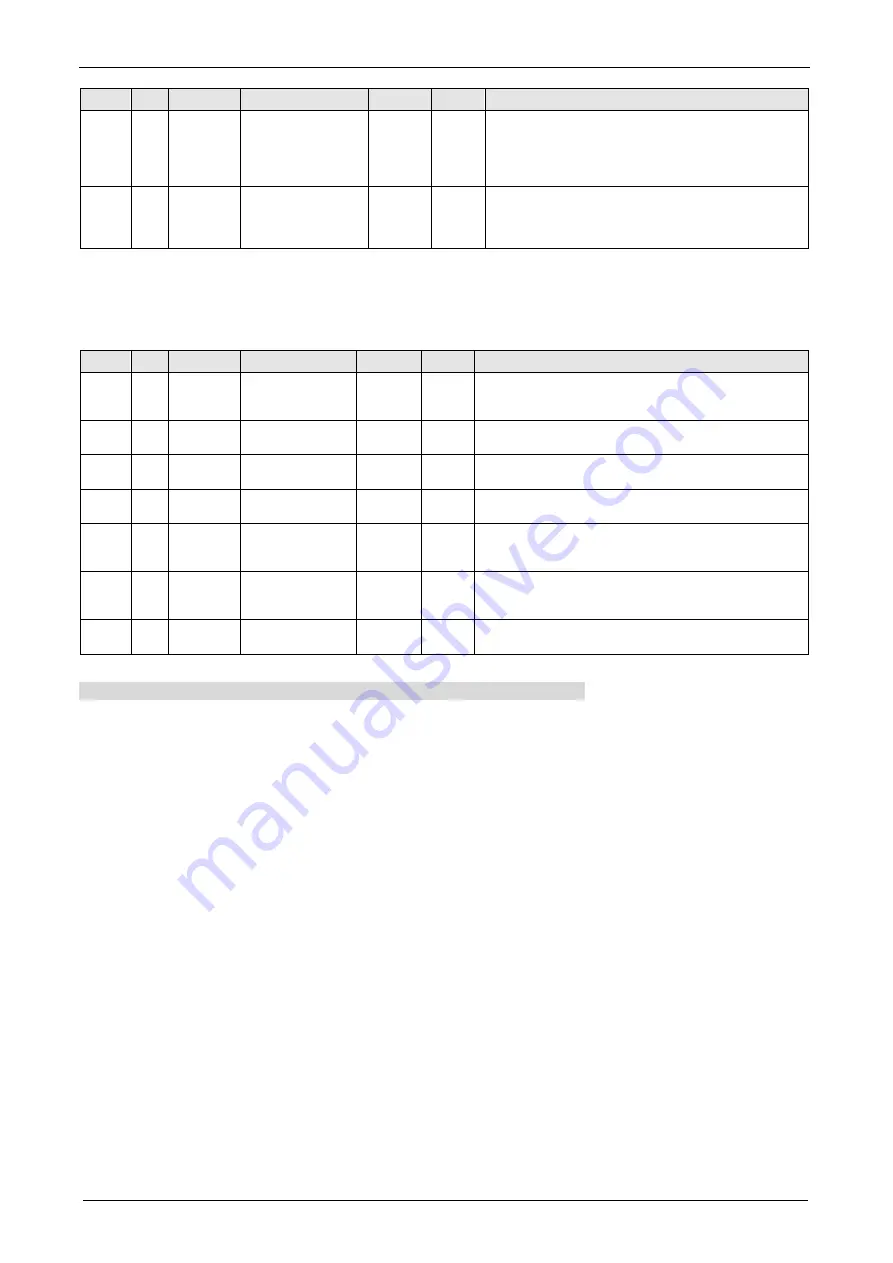
Auto Tuning Functions
5-16
Class No. Attribute Title
Range
Unit
Function
6
05
B
Position 3rd gain valid
time
0 to
10000
0.1 ms
For the standard response mode or high response mode 1
(Pr0.02=1, 2), set the parameter to 0 (invalid).
For high response mode 2 or 3 (Pr0.02=3,4), set the
parameter to "Pr2.22 x 20".
(However, the maximum value is limited to 10000.)
6
06
B
Position 3rd gain
scale factor
50 to
1000
%
For the standard response mode or high response mode 1
(Pr0.02=1,2), set the parameter to 100 (100%).
For high response mode 2 or 3 ((Pr0.02=3,4), set the
parameter to 200 (200%).
When Pr0.02 "Real-time auto-gain tuning setup" = 1 to 4 or 6, the following settings and parameters are
set automatic for enable/disable state of Pr 6.10 "Function expansion setup" load variation suppression
function automatic adjustment.
Relevant parameters
Class No. Attribute Title
Range
Unit
Function
6
10
B
Function expansion
setup
-32768 to
32767
-
When set to Pr 6.10 bit14=1, load variation suppression
function will become enabled (bit1 = 1).
When set to Pr 6.10 bit14=0,it is disabled(bit1 = 0).
6
23
B
Disturbance torque
compensating gain
-100 to
100
%
When set to Pr 6.10 bit14=1, sets to 90 %.
When set to Pr 6.10 bit14=0, sets to 0 %.
6
24
B
Disturbance
observer filter
10 to
2500
0.01 ms When set to Pr 6.10 bit14=1, updates to match rigidity.
When set to Pr 6.10 bit14=0, value is held.
6
73
B
Load estimation
filter
0 to 2500 0.01 ms When set to Pr 6.10 bit14=1, sets to 0.13 ms.
When set to Pr 6.10 bit14=0, sets to 0 ms.
6
74
B
Torque
compensation
frequency 1
0 to 5000 0.1 Hz
Regardless value of the Pr 6.10 bit 14, sets to 0.
6
75
B
Torque
compensation
frequency 2
0 to 5000 0.1 Hz
Regardless value of the Pr 6.10 bit 14, sets to 0.
6
76
B
Load estimation
count
0 to 8
-
When set to Pr 6.10 bit14=1, sets to 4.
When set to Pr 6.10 bit14=0, sets to 0.
How to use
When Pr 0.02 (Setup of real-time auto-gain tuning mode) is set to a value other than 0, control
parameter is automatically set according to Pr0.03 "Real-time auto tuning machine stiffness setup".
When the servo is ON, enter operation command after about 100ms. When the load characteristic is
correctly estimated, Pr 0.04 "Inertia ratio" is updated. With certain mode settings, Pr 6.07 "Torque
command addition value", Pr 6.08 "Positive direction compensation value", Pr6.09 "Negative direction
torque compensation value", and Pr6.50 "Viscous friction compensating gain." will be changed.
When value of Pr0.03 "Real-time auto tuning machine stiffness setup" is increased, the motor
responsiveness will be improved. Determine the most appropriate stiffness in relation to the positioning
setup time and vibration condition.
Summary of Contents for MINAS A6 Series
Page 10: ...Table of contents x Blank page...
Page 11: ...1 Introduction...
Page 26: ...Introduction 1 16 Blank page...
Page 27: ...2 Interface Specifications...
Page 46: ...Interface Specifications 2 20 Blank page...
Page 47: ...3 Front Panel Specifications...
Page 57: ...4 Basic Functions...
Page 85: ...5 Auto Tuning Functions...
Page 151: ...6 Application Functions...
Page 185: ...7 Protective Functions...
Page 224: ...Protective Functions 7 40 Blank page...
Page 225: ...8 Advanced Safety Functions...
Page 230: ...Advanced Safety Functions 8 6 When test pulse is used Duplex safety input Safety input...
Page 245: ...9 List of Parameters...
Page 281: ...10 Timing Chart...
Page 290: ...Timing Chart 10 10 Blank page...
Page 291: ...11 Power Supply Module...