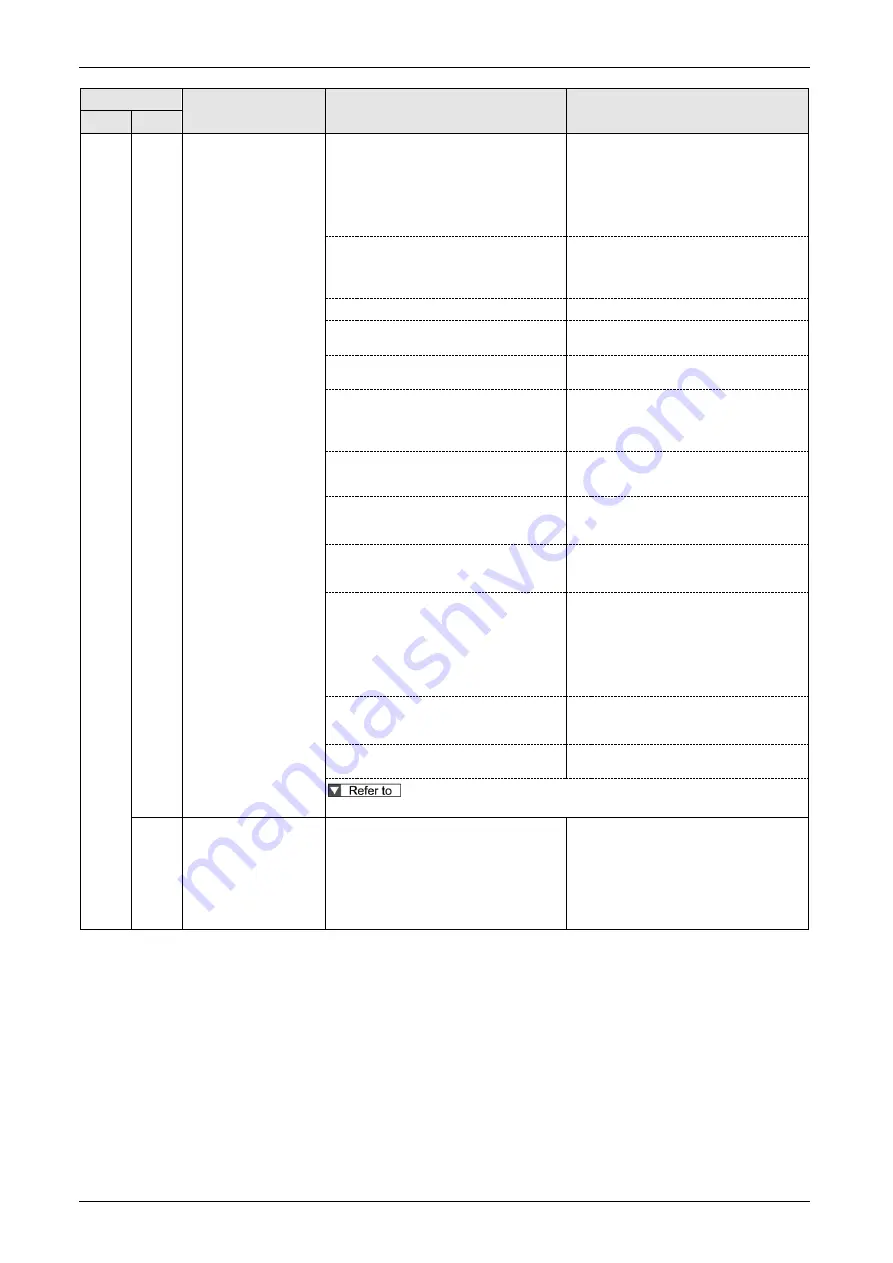
7.2Details of protective function
7-9
Error No.
Protective function
Causes
Measures
Main
Sub
16
0
Over-load protection
In the driver module, the overload load
factor calculated from the torque command
of each axis servo motor exceeded the
specified value.
Check if the torque (current) waveform is
oscillating with large variations in the
vertical direction in EtherCAT
communication or PANATERM for Multi.
Check the overload warning display and
load factor on the front panel or by
communication.
1)
Load was heavy and actual torque
has exceeded the rated torque and
kept running for a long time.
1) Increase the capacity of the driver
module and motor. Set up longer
acceleration/ deceleration time. Lower
the load.
2)
Gain adjustment failed.
2) Make a re-adjustment of gain.
3)
Oscillation and hunching action.
3) Make a wiring as per the wiring
diagram. Replace the cables.
4)
Motor vibration, abnormal noise.
4) If auto-tuning function is used, stiffness
Lower the setting.
5)
Pr 0.04 “Inertia ratio” setup error.
5) Manually set the appropriate value for
Pr 0.04 “Inertia ratio”
Set and disable the auto tuning
function.
6)
Miswiring, disconnection of the motor 6) Connect the motor wires as shown in
the wiring diagram. Replace the cable.
7)
Machine has collided or the load has
gotten heavy. Machine has been
distorted.
7) Remove machine distortion. Reduce
the load. Replace the machine.
8)
Operate the motor while the
electromagnetic brake is operating
8) Check the timing to release the brake.
Also check Pr4.59 “Mechanical brake
signal setup”. Replace the motor.
9)
In the wiring between the axes of the
same driver module or between a
plurality of servo motors connected to
a plurality of driver modules, the motor
line or encoder line is mistakenly
connected to another axis and
miswired.
9) Make a correct wiring by matching the
correct motor and encoder wires.
10) Pr5.12 "Over-load level setup" is too
low.
10) Set Pr5.12 "Over-load level setup" to 0
(Set the maximum value allowed for the
motor).
11) Failure of driver module.
(Failure of motor drive circuit)
11) Replace the driver module.
The over-load protection time characteristics are described on the end of this section.
1
Torque saturation error
protection
On the driver module, the torque limiting
(TLC) status of each axis has continued for
the time set in Pr7.16 “Torque saturation
error protection frequency” or Pr6.57
“Torque saturation error protection
detection time”.
Check the torque command of the driver
module with EtherCAT communication or
PANATERM for Multi, and check whether
it is restricted by the torque limit.
Take steps to reduce the load factor in the
same way as Err16.0 to reduce the
absolute value of the torque command.
(To be continued)
Summary of Contents for MINAS A6 Series
Page 10: ...Table of contents x Blank page...
Page 11: ...1 Introduction...
Page 26: ...Introduction 1 16 Blank page...
Page 27: ...2 Interface Specifications...
Page 46: ...Interface Specifications 2 20 Blank page...
Page 47: ...3 Front Panel Specifications...
Page 57: ...4 Basic Functions...
Page 85: ...5 Auto Tuning Functions...
Page 151: ...6 Application Functions...
Page 185: ...7 Protective Functions...
Page 224: ...Protective Functions 7 40 Blank page...
Page 225: ...8 Advanced Safety Functions...
Page 230: ...Advanced Safety Functions 8 6 When test pulse is used Duplex safety input Safety input...
Page 245: ...9 List of Parameters...
Page 281: ...10 Timing Chart...
Page 290: ...Timing Chart 10 10 Blank page...
Page 291: ...11 Power Supply Module...