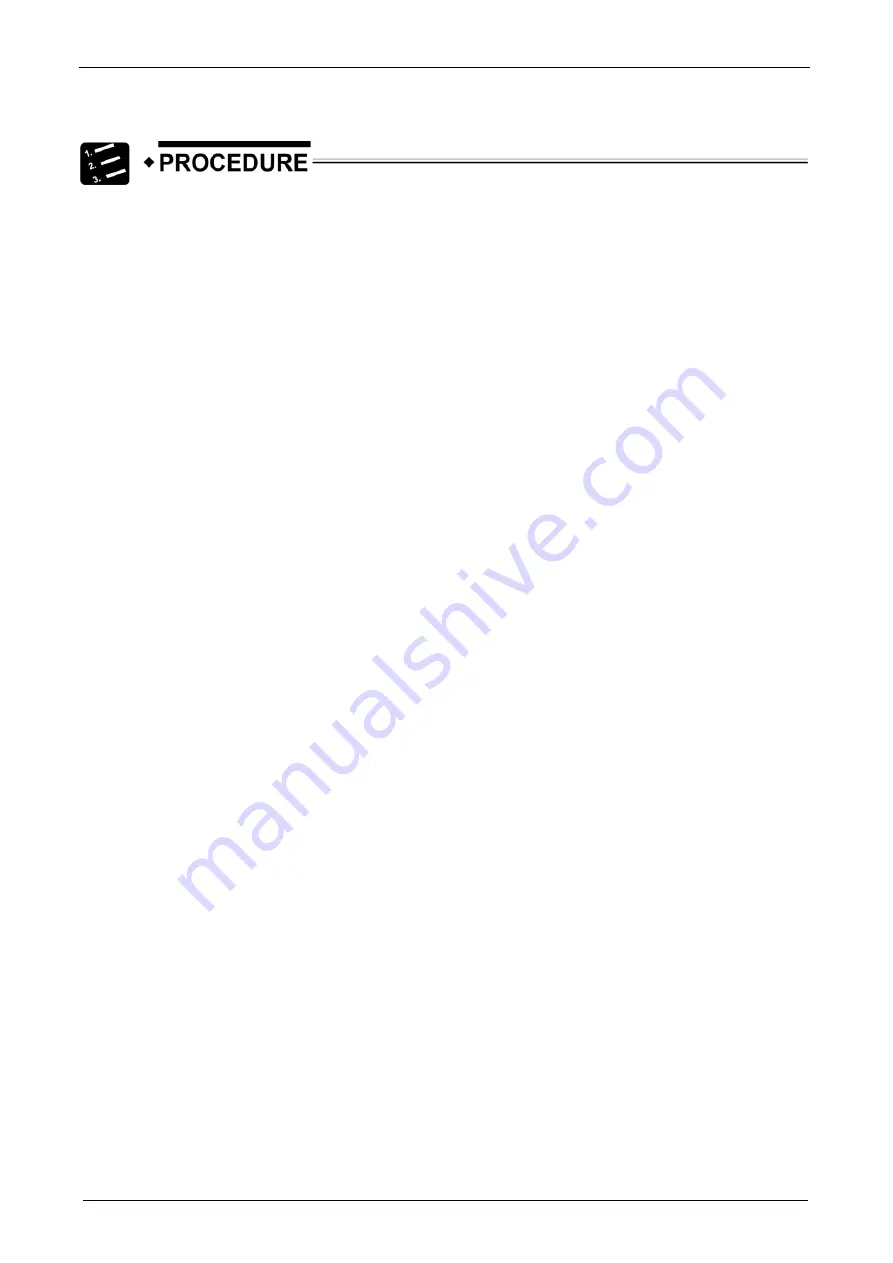
Auto Tuning Functions
5-50
Load variation stabilization setting (There is load inertia variation, assumed an articulated robot,
etc.)
1. Turn ON the control power in two-degree-of-freedom position control (synchronization
type) (Pr. 0.01=0, Pr. 6.47 bit0=1 bit3=1).
2. Set the command response filter (Pr. 2.22) to 10ms.
3. Set Real-time auto tuning to load variation support mode, and operate the motor in a
pattern as large as possible load variation occurs in this state. As a result, Pr6.10 bit1 and
bit2 becomes 1.
4. Set the stiffness setting (Pr. 0.03) as large as possible.
5. Set the command response filter to appropriate value to continue to derease while
checking response of the motor. In case of need to the multi-axis trajectory control, change
all axes Pr2.22 to the same value and adjust.
Summary of Contents for MINAS A6 Series
Page 10: ...Table of contents x Blank page...
Page 11: ...1 Introduction...
Page 26: ...Introduction 1 16 Blank page...
Page 27: ...2 Interface Specifications...
Page 46: ...Interface Specifications 2 20 Blank page...
Page 47: ...3 Front Panel Specifications...
Page 57: ...4 Basic Functions...
Page 85: ...5 Auto Tuning Functions...
Page 151: ...6 Application Functions...
Page 185: ...7 Protective Functions...
Page 224: ...Protective Functions 7 40 Blank page...
Page 225: ...8 Advanced Safety Functions...
Page 230: ...Advanced Safety Functions 8 6 When test pulse is used Duplex safety input Safety input...
Page 245: ...9 List of Parameters...
Page 281: ...10 Timing Chart...
Page 290: ...Timing Chart 10 10 Blank page...
Page 291: ...11 Power Supply Module...