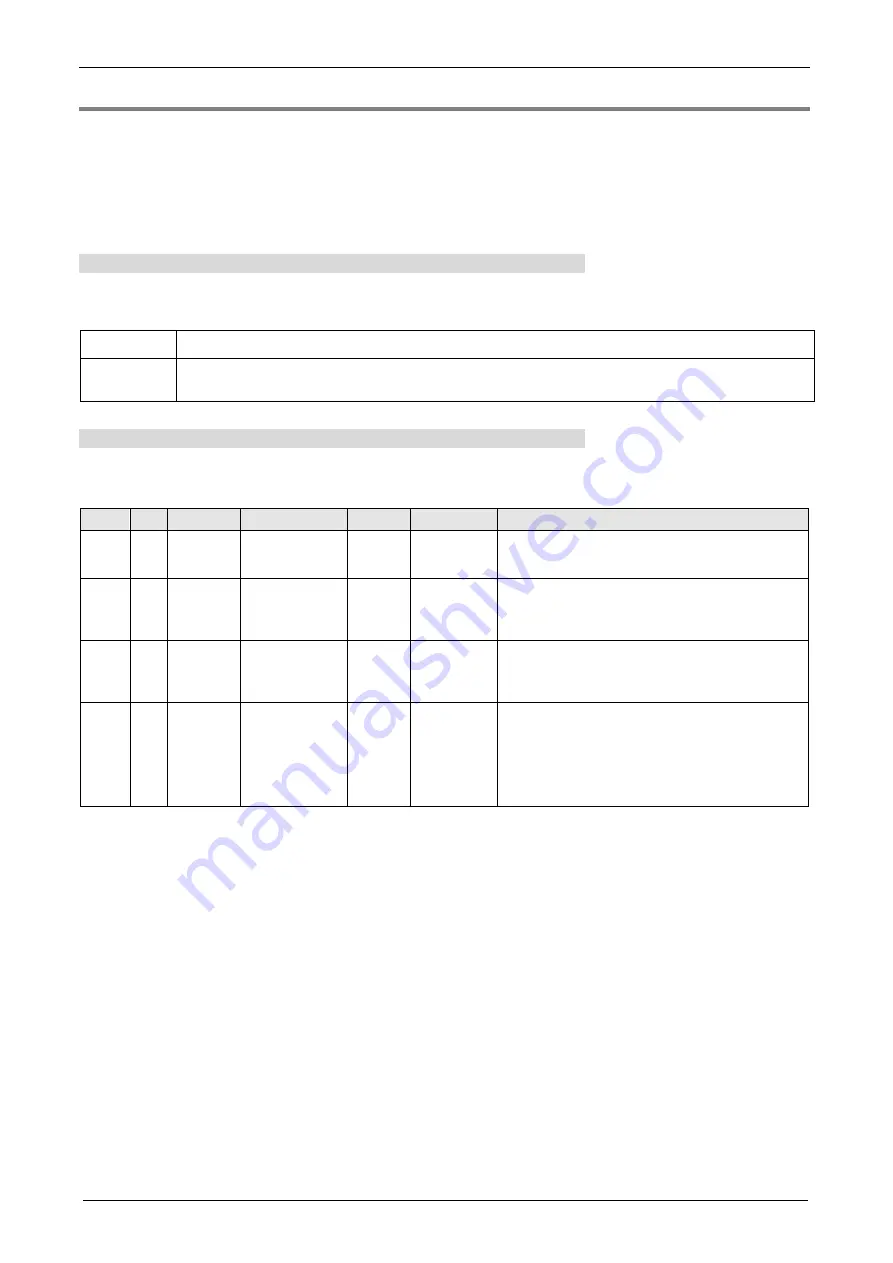
Auto Tuning Functions
5-52
5.2.12 Friction torque compensation
To reduce effect of friction represented by mechanical system, 3 types of friction torque compensation
can be applied:
Offset load compensation that cancels constant offset torque
The dynamic friction compensation that varies direction as the operating direction varies
Viscous friction torque correction amount that is varied by the command speed
Applicable range
This function can be applicable only when the following conditions are satisfied.
Conditions under which the Friction torque compensation is activated:
Control Mode
Specific to individual functions. Refer to “Relevant parameters” shown below.
Others
Should be in servo-on condition
Parameters except for controls such as torque limit setup, are correctly set, assuring that the motor can run smoothly.
Relevant parameters
Combine the following 3 parameters to setup appropriate friction torque compensation.
Relevant parameters
Class No. Attribute
Title
Range
Unit
Function
6
07
B
Torque command
additional value
-100 to
100
%
Set up the offset load compensation value usually added
to the torque command in a control mode except for the
torque control mode.
6
08
B
Positive direction
torque
compensation
value
-100 to
100
%
Dynamic friction compensation value to be added to the
torque command at the time of position control and
full-closed control and when forward direction position
command is entered.
6
09
B
Negative direction
torque
compensation
value
-100 to
100
%
Dynamic friction compensation value to be added to the
torque command at the time of position control and
full-closed control and when reverse direction position
command is entered.
6
50
B
Viscous friction
compensating
gain
0 to
10000
0.1%
(10000r/min)
When Two-degree-of-freedom control mode is effective,
the result multiplying the command speed by this setting
is added to the torque command as the viscous friction
torque correction amount. By setting the estimated
viscous friction coefficient of Real-time auto tuning, there
are cases in which the feedback scale position deviation
in the vicinity of steady state may be improved.
Summary of Contents for MINAS A6 Series
Page 10: ...Table of contents x Blank page...
Page 11: ...1 Introduction...
Page 26: ...Introduction 1 16 Blank page...
Page 27: ...2 Interface Specifications...
Page 46: ...Interface Specifications 2 20 Blank page...
Page 47: ...3 Front Panel Specifications...
Page 57: ...4 Basic Functions...
Page 85: ...5 Auto Tuning Functions...
Page 151: ...6 Application Functions...
Page 185: ...7 Protective Functions...
Page 224: ...Protective Functions 7 40 Blank page...
Page 225: ...8 Advanced Safety Functions...
Page 230: ...Advanced Safety Functions 8 6 When test pulse is used Duplex safety input Safety input...
Page 245: ...9 List of Parameters...
Page 281: ...10 Timing Chart...
Page 290: ...Timing Chart 10 10 Blank page...
Page 291: ...11 Power Supply Module...