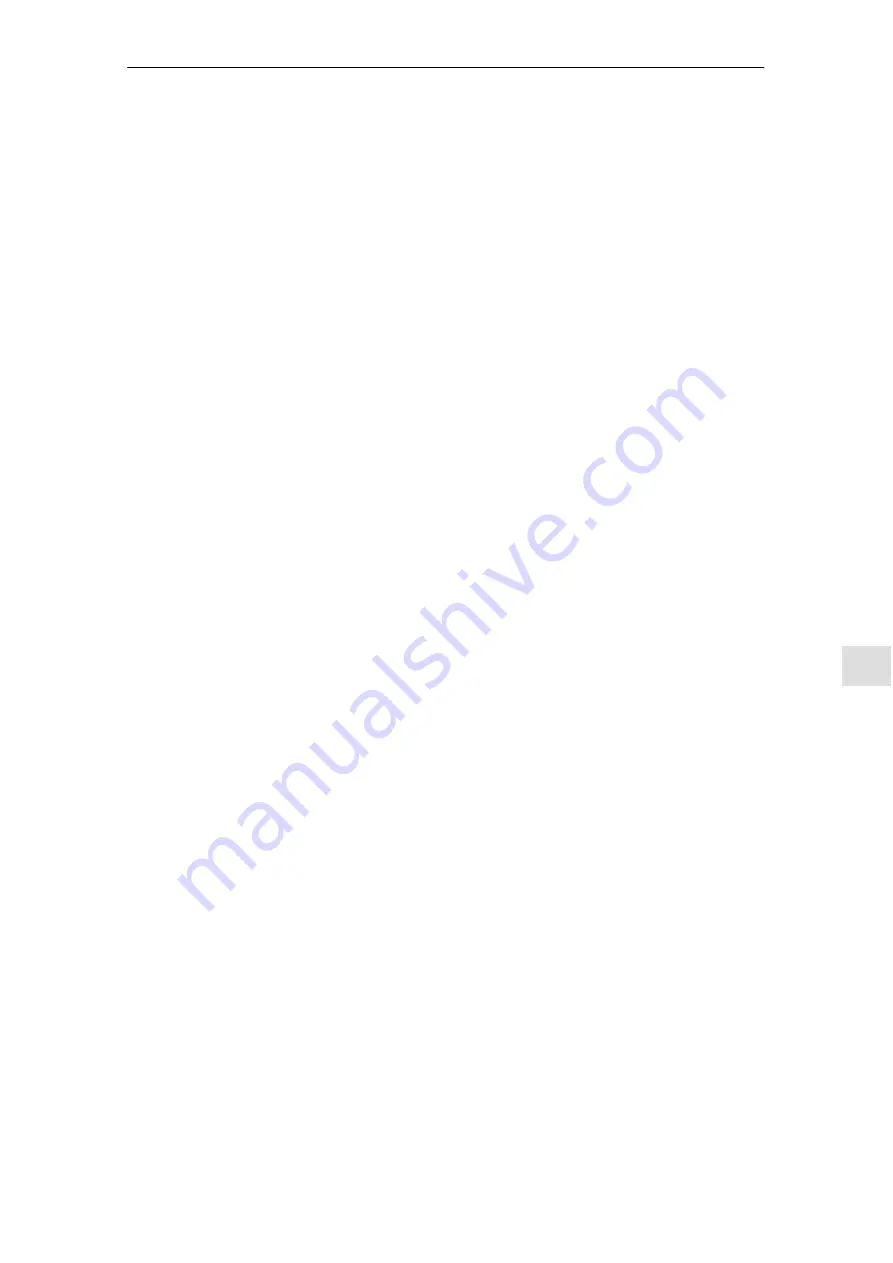
7
7.3
List of faults and warnings
7-681
Siemens AG 2005 All Rights Reserved
SIMODRIVE 611 universal Description of Functions (FBU) – 04.05 Edition
727
Invalid combination of power section and synchron-
ous motor
Cause
The power module has not been released for synchronous motors.
Remedy
– Check configuring
– Use a valid power section
Acknowledgement POWER ON
Stop response
STOP II (SRM, SLM) STOP I (ARM)
728
Torque/current adaptation factor too high
Cause
The adaptation factor between the setpoint torque and the torque gen-
erating current (Iq) in the speed controller is too high.
Remedy
Check P1103, P1107 and P1113 and if required, enter correct values.
Third-party motor:
The values should be determined from a motor data sheet.
Siemens motor:
The values are determined from the motor code (P1102).
Acknowledgement POWER ON
Stop response
STOP II (SRM, SLM) STOP I (ARM)
729
Invalid motor stall current
Cause
The motor stall current (P1118) is less than or equal to zero.
Remedy
Determine the stall current of the motor used and enter in P1118.
Third-party motor:
The stall current should be determined from a motor data sheet.
Siemens motor:
The stall current is determined from the motor code (P1102).
Acknowledgement POWER ON
Stop response
STOP II (SRM, SLM) STOP I (ARM)
731
Invalid rated output
Cause
The rated motor output (P1130) of the motor is less than or equal to
zero.
Remedy
Determine the rated motor output of the motor used and enter in
P1130.
Third-party motor:
The rated motor output should be determined from a motor data sheet.
Siemens motor:
The rated motor output is determined from the motor code (P1102).
Acknowledgement POWER ON
Stop response
STOP II (SRM, SLM) STOP I (ARM)
7 Fault Handling/Diagnostics
01.99
04.05