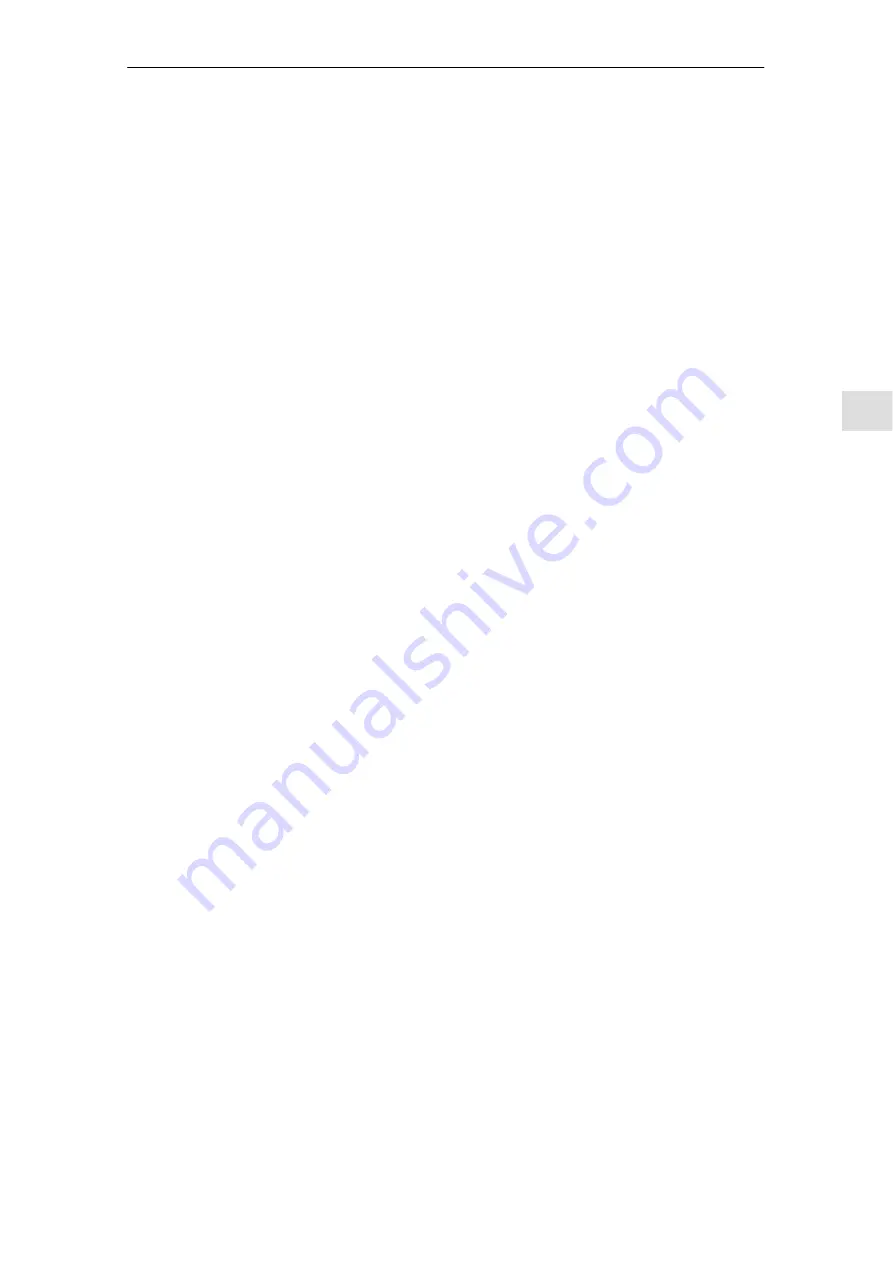
4
01.99
4.7
Induction motor operation with induction motor
4-141
Siemens AG 2005 All Rights Reserved
SIMODRIVE 611 universal Description of Functions (FBU) – 04.05 Edition
4.7
Induction motor operation with induction motor
4.7.1
Description
The IM function permits pure encoderless operation (IM operation) or
mixed operation (encoderless operation/operation with encoder).
The induction motor operation for a ”SIMODRIVE 611 universal” drive
is used for 4–quadrant closed–loop speed control of induction motors
without speed or rotor position encoder.
Induction motor operation permits higher demands to be fulfilled re-
garding the dynamic control performance and the stall immunity of con-
ventional converter drives with V/Hz characteristic control. Compared
to drives with rotor position encoder, the speed accuracy is somewhat
lower and therefore it must be taken into account, that in the lower
speed range, the dynamic response and smooth running characteristics
will deteriorate.
IM (Induction Motor) operation is used, e.g. in the area of special high–
speed motors, for grinding applications and for drives for punches and
presses.
As the dynamic performance in IM operation is less than MSD oper-
ation with encoder, a speed–torque–frequency pre–control is imple-
mented to improve the control dynamic performance.
This pre–control is only active in induction motor operation. It pre–con-
trols, with information about the drive torque, taking into account the
existing torque and current limits and the load (motor – P1117 + load –
P1123:8 (from SW 2.4)), the torque required for a particular speed
change, in the fastest possible time.
This means, that when correctly parameterized, overshoot is prevented
and the controlled dynamic performance is enhanced.
For the torque pre–control, a smoothing time can be parameterized via
P1459.
The speed controller is parameterized for induction motor operation
using P1451 and P1453 due to the low dynamic performance.
In the low speed range, for pure induction motor operation, the actual
speed, the orientation and the actual flux can no longer be calculated.
This is due to the accuracy of the measured values and the parameter
sensitivity of the technique. Thus, an open–loop current/frequency con-
trol is selected.
The changeover threshold is parameterized using P1466
, whereby a 5
% hysteresis is implemented.
In order to be able to accept a high load torque, even in the open–loop
controlled range, the motor current can be increased via P1458.
IM operation
Applications
Closed–loop
control
4 Commissioning
04.99