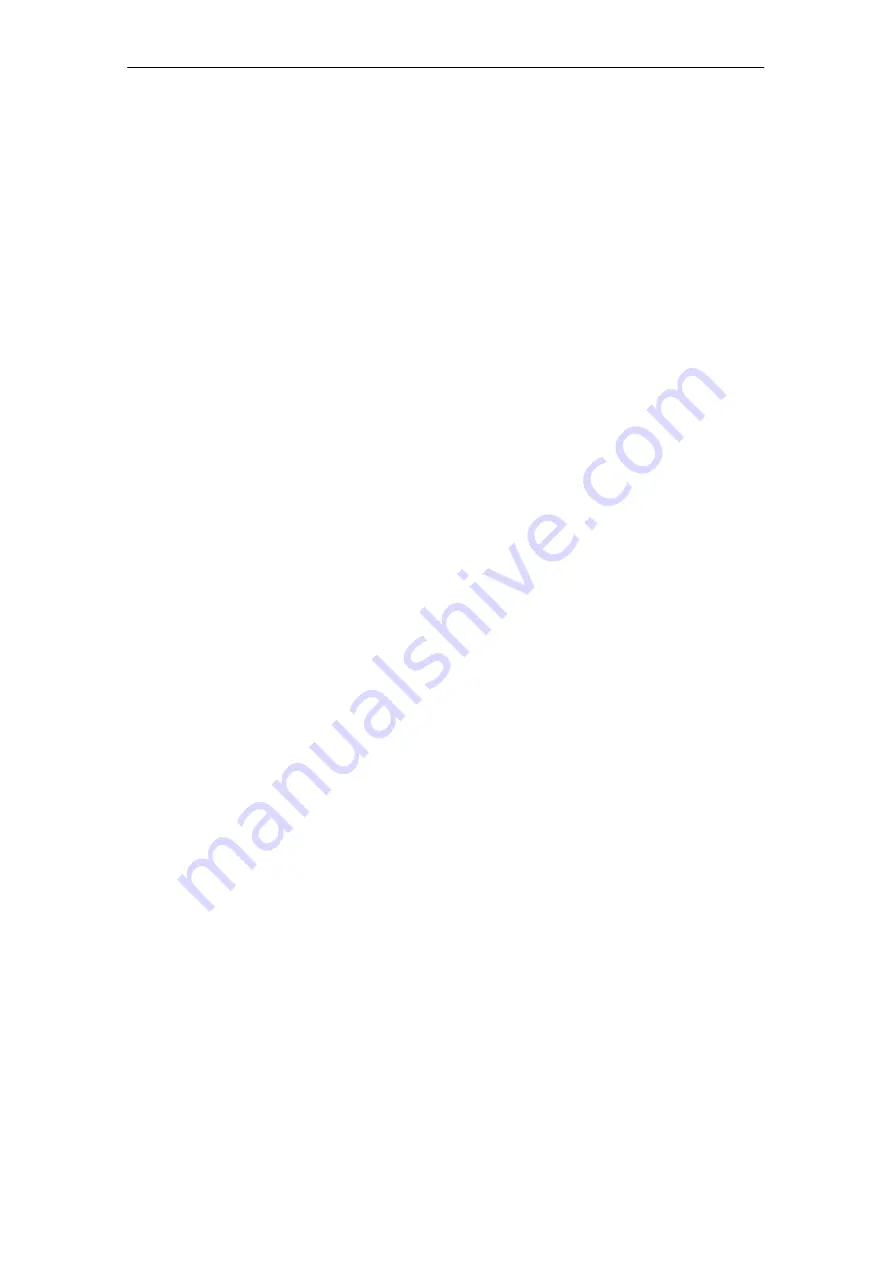
7
7.3
List of faults and warnings
7-690
Siemens AG 2005 All Rights Reserved
SIMODRIVE 611 universal Description of Functions (FBU) – 04.05 Edition
777
Current for the rotor position identification too high
Cause
A current was parameterized in P1019, which is greater than the cur-
rent which is permissible for the motor and the power section used.
Remedy
Reduce the current via P1019.
Acknowledgement POWER ON
Stop response
STOP II (SRM, SLM) STOP I (ARM)
778
Impermissible converter frequency for rotor position ID
Cause
When selecting the rotor position identification (P1019), drive converter
frequencies (P1100) of 4 or 8 kHz are permissible.
Remedy
Change the drive converter frequency or cancel the rotor position iden-
tification.
Acknowledgement POWER ON
Stop response
STOP II (SRM, SLM) STOP I (ARM)
779
Motor moment of inertia, motor \%d invalid
Cause
The motor moment of inertia (P1117) is incorrect (less than/equal to
zero).
Remedy
Enter the valid motor moment of inertia for the motor used, in P1117.
Third-party motor:
The motor moment of inertia should be determined from a motor data
sheet.
Siemens motor:
The characteristic motor data should be determined from the motor
code (P1102).
Acknowledgement RESET FAULT MEMORY
Stop response
STOP II (SRM, SLM) STOP I (ARM)
780
No-load current, motor > rated motor current (motor
\%d)
Cause
The motor no-load current (P1136) has been parameterized greater
than the rated motor current (P1103).
Remedy
Enter the valid currents for the motor used in P1136 and P1103.
Third-party motor:
The required currents should be determined using a motor data sheet.
Siemens motor:
The currents are determined using the motor code (P1102).
Acknowledgement RESET FAULT MEMORY
Stop response
STOP II (SRM, SLM) STOP I (ARM)
7 Fault Handling/Diagnostics
01.99
04.05