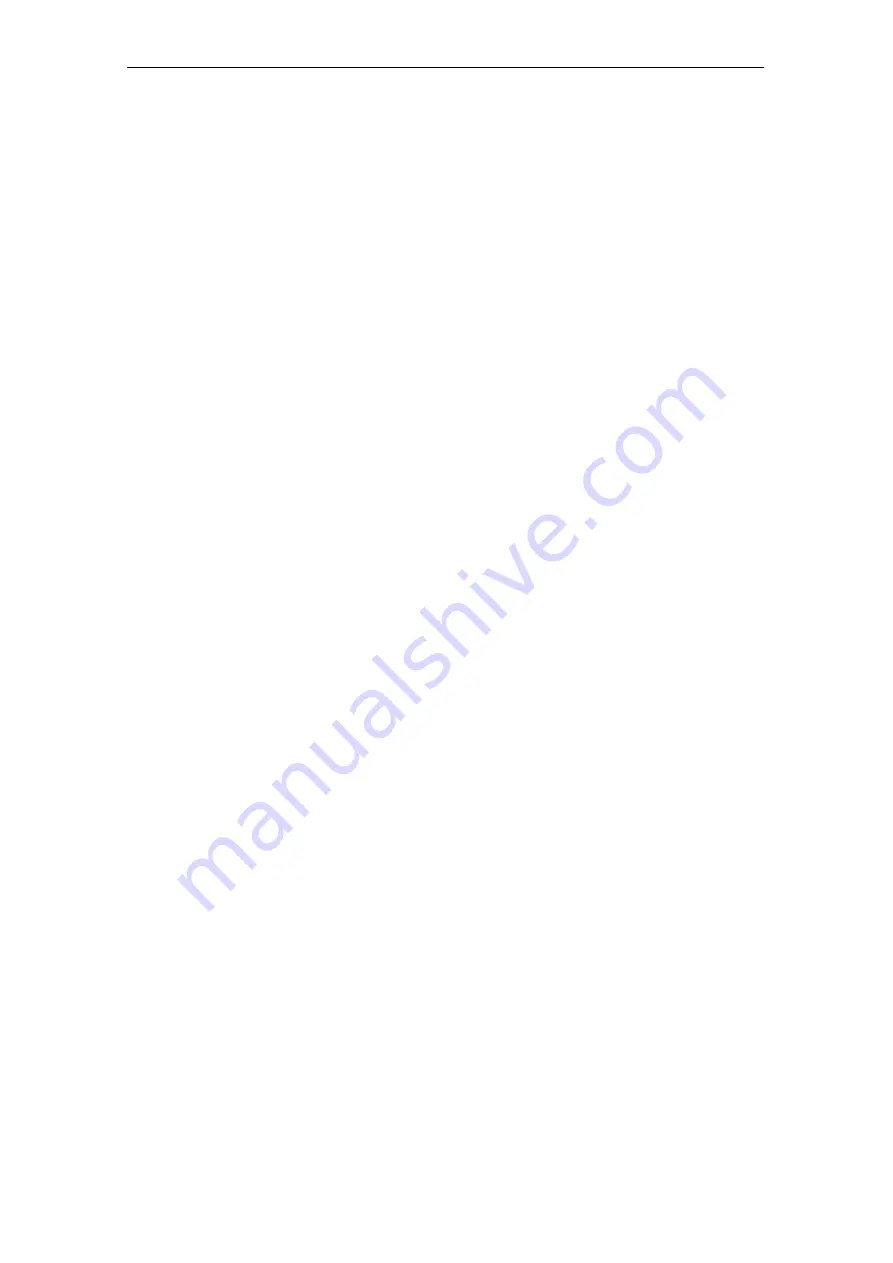
7
7.3
List of faults and warnings
7-696
Siemens AG 2005 All Rights Reserved
SIMODRIVE 611 universal Description of Functions (FBU) – 04.05 Edition
795
Ang. encoder, pos. ref. value normalization factor too
large. Suppl. info: \%u
Cause
The position reference value normalization for the angular encoder in-
terface is not permissible.
Supplementary info
= 1 ––> Condition P0401 * P0895 < 8388608 violated
= 2 ––> Condition P0402 * P0896 < 8388608 violated
Remedy
Check parameterization via P0401, P0402, P0895 and P0896. It may
be possible to achieve the conditions above by shortening the numera-
tor P0401 * P0895 with the denominator P0402 * P0896.
Acknowledgement POWER ON
Stop response
STOP II
797
Error in center frequency measurement
Cause
The speed was too high during the center frequency measurement
(current calibration). The center frequency is measured automatically at
run-up, or when the pulses are inhibited.
Remedy
Power up the drive converter if the motor runs at a reduced speed.
Acknowledgement POWER ON
Stop response
STOP I
798
Measured value memory active
Cause
The measured-value memory was active during power-up.
Remedy
Run up again.
Acknowledgement POWER ON
Stop response
STOP I
799
FEPROM backup and HW Reset required
Cause
Parameters were re-calculated. Parameters must be saved and the
module run up again after this new calculation.
Remedy
The newly calculated data should be saved in the FEPROM. The new
parameters become effective the next time that the module runs up!
Acknowledgement POWER ON
Stop response
STOP II (SRM, SLM) STOP I (ARM)
800
Minus hardware limit switch
Cause
A 1/0 edge was identified at the ”Minus hardware limit switch” input signal.
Remedy
– In the pos mode: Return the drive to the traversing range using jog
key 1 or 2.
– In the n-set mode: Enter a setpoint that opposes the approach direction.
Acknowledgement not required
Stop response
STOP VII
7 Fault Handling/Diagnostics
01.99
04.05