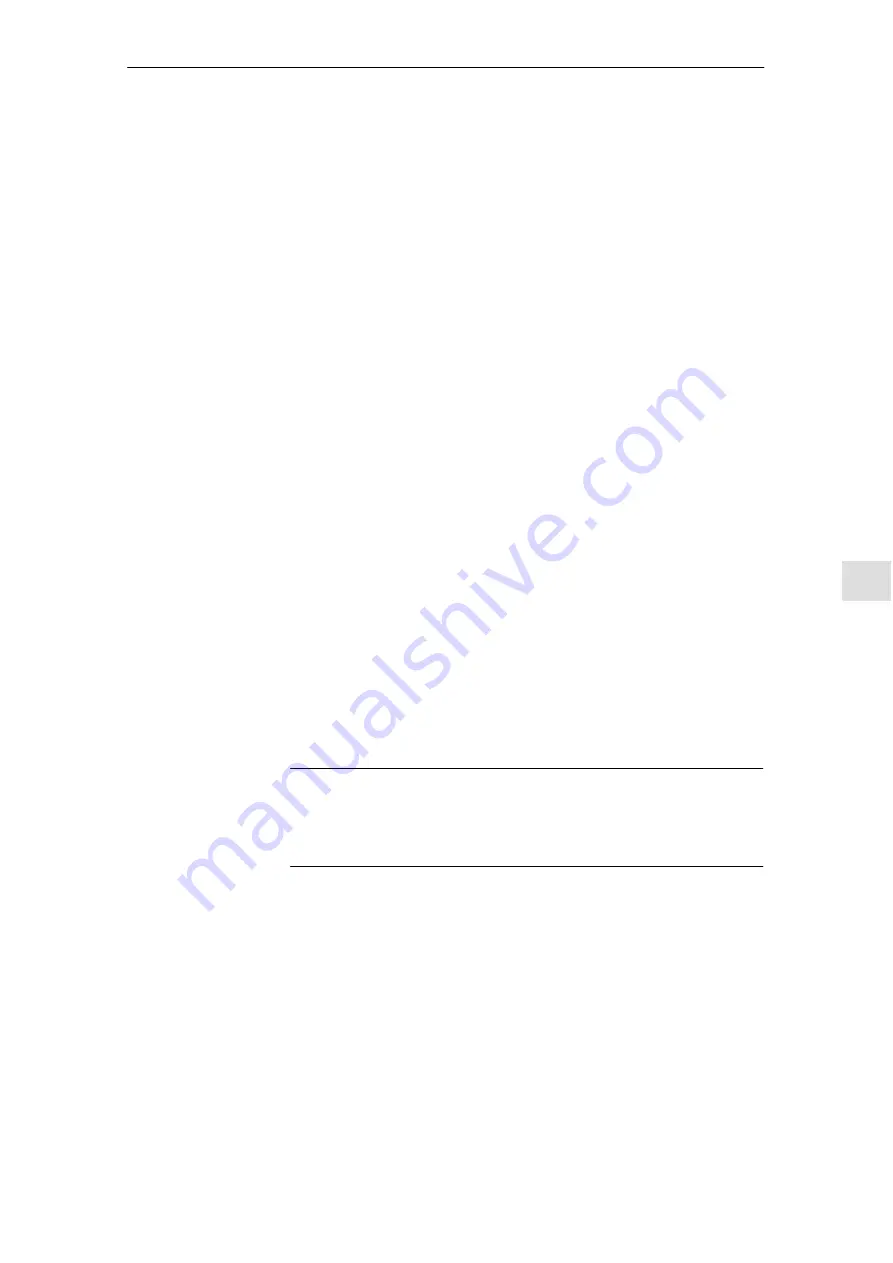
6
6.3
Axis couplings (from SW 3.3)
6-461
Siemens AG 2005 All Rights Reserved
SIMODRIVE 611 universal Description of Functions (FBU) – 04.05 Edition
6.3.3
Torque setpoint coupling (from SW 4.1)
A torque setpoint coupling (master/slave operation) between two rigidly
connected drives can be established via analog signals or PROFIBUS–
DP.
How is this function activated?
The master drive is changed–over into the closed–loop speed con-
trolled mode.
The torque setpoint at the speed controller output of the master
drive is provided via the process data ”Msoll” (number 50114).
The slave drive must be changed–over into the open–loop torque
controlled mode using process data ”STW1.14”.
The torque setpoint of the master drive should be read into the
slave drive using process data ”MsollExt” (number 50113).
P0882 determines the normalization of process data ”Msoll” and
”MsollExt”. The percentage value of the rated motor torque, entered
into P0882, corresponds to value 16384 in the PROFIBUS interface.
The polarity of the torque setpoint can be inverted by entering negative
values.
The torque, corresponding to 16384, is displayed in Nm in P1725
(P0882
rated motor torque).
The ”Msoll” process data is smoothed using the transition frequency set
in P1252. The pre–setting P1252 = 100 Hz can result in problems for me-
chanical couplings. If required, the smoothing (deadtime) should be disa-
bled using P1252 = 0.
Note
For torque setpoint couplings via PROFIBUS–DP, when compared to
coupling via analog signals (refer to Chapter 6.6), there is a longer
dead time (
1 ms instead of the speed controller clock cycle).
Description
Scaling
Smoothing and
clock cycle
6 Description of the Functions
01.99
08.01