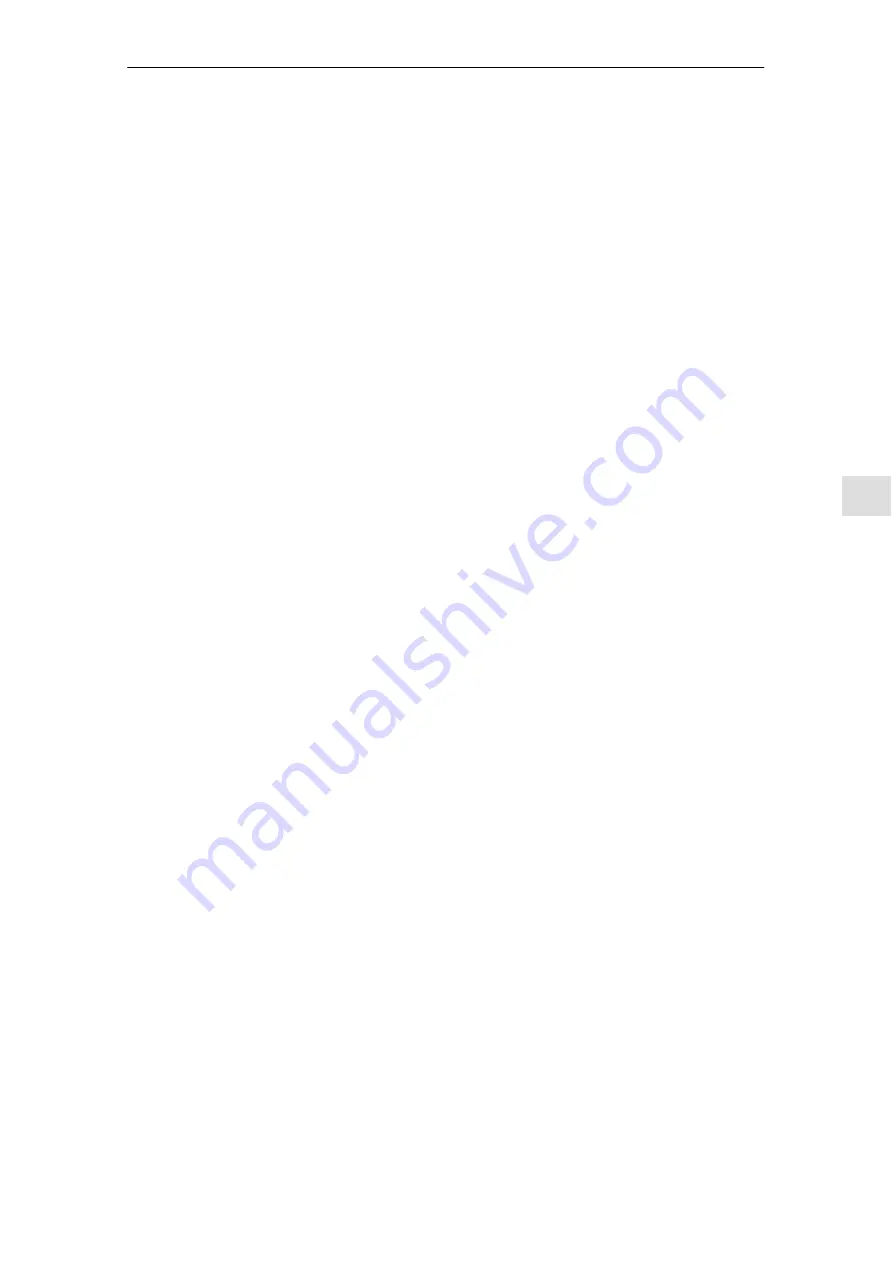
5
5.6
Net data (PKW and PZD area)
5-277
Siemens AG 2005 All Rights Reserved
SIMODRIVE 611 universal Description of Functions (FBU) – 04.05 Edition
When there is at least one fault, the drive fault buffer (P0945:1 to
P0945:8) should be read out via PROFIBUS, and buffered on the
master side.
Assumptions for the slave:
The drive has been completely commissioned is connected to
PROFIBUS–DP and is ready to run.
P0918 = 12 (PROFIBUS node address) has been set
Assumptions for the master:
The DP master is a SIMATIC S7 (CPU: S7–315–2–DP)
Hardware configuration
– 1–axis, PPO type 1, node address = 12
– Part
I address
O address
PKW
272 – 279
272 – 279
PZD
280 – 283
280 – 283 (not shown in the example)
If the input signal from the peripheral (I/O) area E281.3 (ZSW1.3, fault
present/no fault present) = ”1” signal, then the following must be execu-
ted on the master side (refer to Fig. 5-20):
1. Programming SFC14 and SFC15
The standard functions SFC14 ”Read slave data” and SFC15 ”write
slave data” are required in order to consistently transfer more than 4
bytes.
2. Request parameter value
– Write into the PKW output signals (PAB 272 –279)
with
AK = 6, PNU = 945, IND = 1, PWE = no significance
3. Read parameter value and save
– Evaluate the PKW input signals (PEB 272 –279)
– If AK = 4 or 5,
PNU = 945, IND = 1 and PWE = xx then OK
– Read and save P945:1 = xx
– If AK = 7,
then evaluate the fault number in PEW 278 (refer to Table 5-31)
4. Repeat points 1 and 2 to read the other sub–parameters of the fault
condition
P945:2
––> PNU = 945, IND = 2
to to
P945:8
––> PNU = 945, IND = 8
This repetitive procedure can be exited if a ”0” is in one of the sub–
parameters.
All of the faults of the last fault situation are then detected.
Example:
Reading
parameters via
PROFIBUS
What has to be
programmed
on the master side?
5 Communications via PROFIBUS DP
08.99
04.99