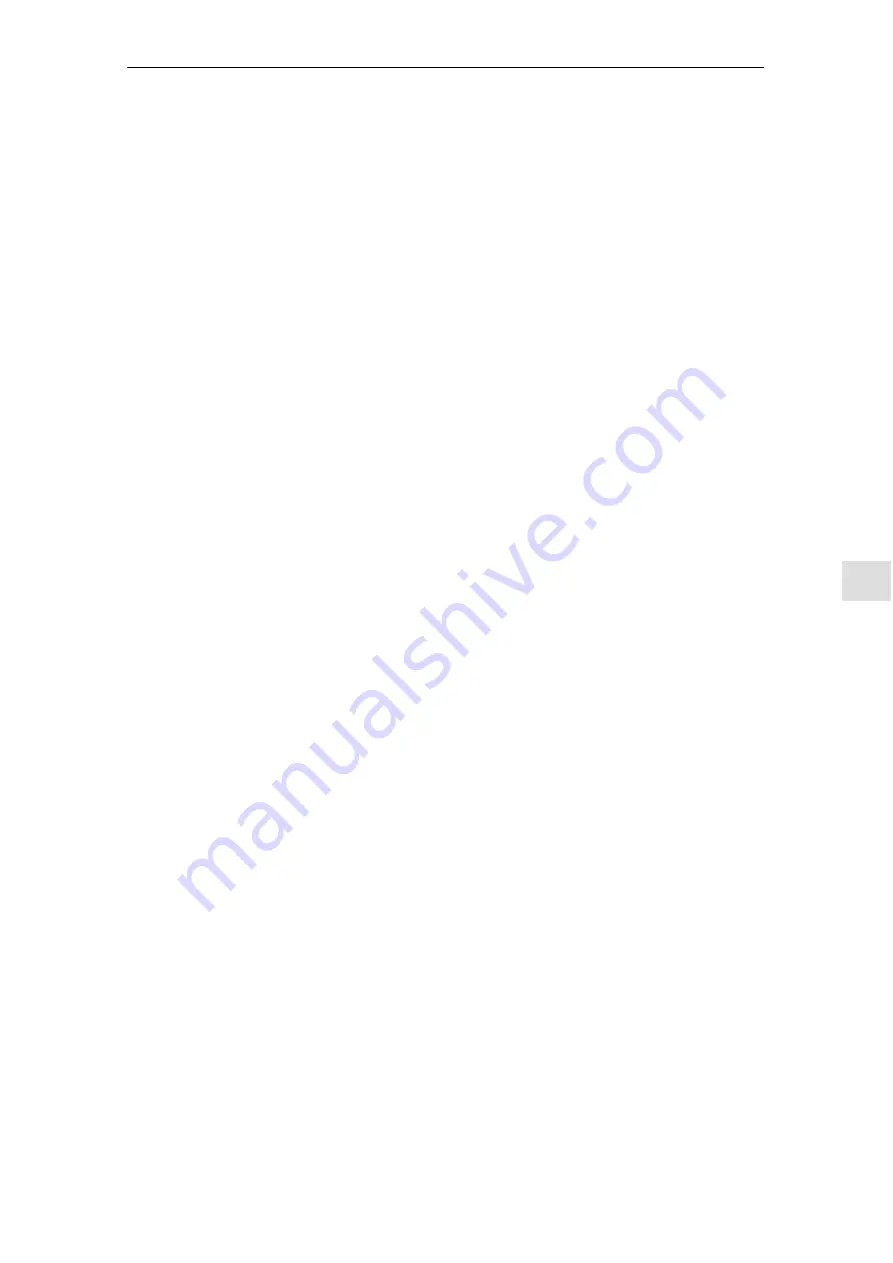
6
6.16 Rotor position synchronization/rotor position identification
6-617
Siemens AG 2005 All Rights Reserved
SIMODRIVE 611 universal Description of Functions (FBU) – 04.05 Edition
This has only been released for 1FN3 motors.
Due to the different mechanical designs, for the motion–based rotor
position identification technique, the result must be checked once
when the drive system is first commissioned. The deviation of mea-
sured rotor position should be < 10
°
electrical.
The measuring system must stiffly mounted.
The axis stiction must be low in comparison to the rated motor
torque. An excessively high stiction can have a significant negative
impact on the accuracy of the rotor position identification and, under
certain circumstances, make it impossible to execute the rotor posi-
tion identification with motion.
The technique may only be used for horizontal axes which can
freely move and which do not have a brake.
During the rotor position identification run, it is not permissible that
external forces are applied to the motor.
If the previous secondary conditions/limitations are not fulfilled, then
1FN3 motors can only be operated with Hall sensor boxes or with
absolute measuring systems.
When using an absolute motor measuring system, the rotor position
identification can only be used to determine the commutation angle
offset (P1016).
The technique can only be started when the controller and pulses
are enabled as current must flow through the motor.
When this technique is used, under worst case condition, movement
in the range of
±
10 mm can occur.
Until the identification has been completed, the axis to be identified
must be set in the tracking mode in order to suppress fault 135 dur-
ing the identification routine (standstill monitoring).
When starting the rotor position identification routine via P1736 as a
test:
– For a test start, fault 135 (standstill monitoring) can be output,
which must be acknowledged with RESET.
– For coupled axes, the test start for rotor position identification is
not permitted
For the parameterization of the rotor position identification for the mo-
tion–based technique, initially, a rotor position identification run must be
made with a standard parameterization.
The noise which is generated should be heard as a sequence of soft
surges.
For the technique
based
on motion
(P1075=3,
from SW 6.1)
Parameterization for
the motion–based
technique (from SW
6.1)
6 Description of the Functions
08.02