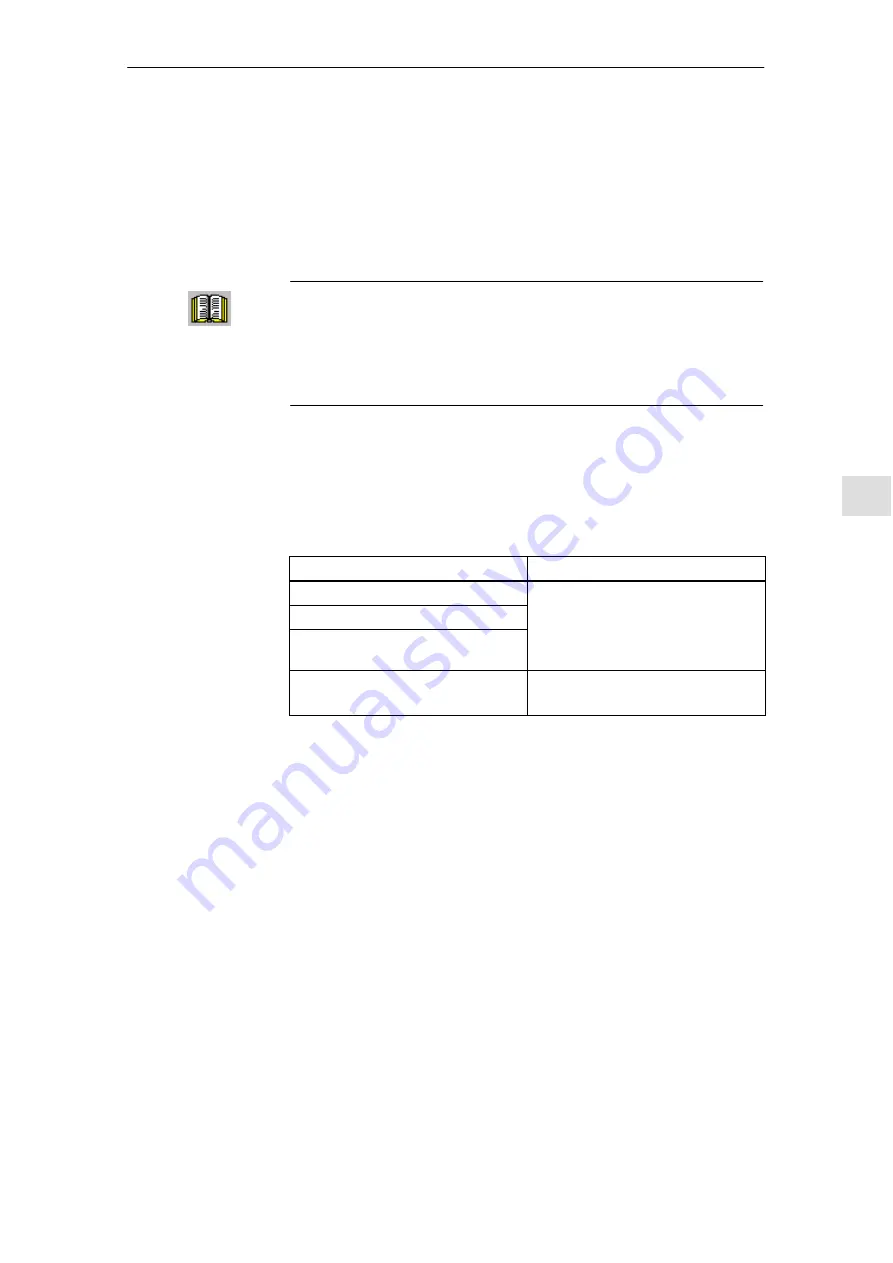
5
5.8
Motion Control with PROFIBUS–DP (from SW 3.1)
5-293
Siemens AG 2005 All Rights Reserved
SIMODRIVE 611 universal Description of Functions (FBU) – 04.05 Edition
5.8
Motion Control with PROFIBUS–DP (from SW 3.1)
Using the ”Motion Control with PROFIBUS DP” function, a clock–cycle
synchronous drive coupling can be established between a DP master
and one or several slaves via the PROFIBUS fieldbus.
Reader’s note
The clock–synchronous drive coupling is defined in the following
documentation:
Reference:
/PPA/, PROFIdrive Profile for Drive Technology,
Version 3.1 July 2002
Clock–synchronous operation can be implemented using the following
DP masters:
Table 5-36
Examples for clock–synchronous masters
DP–MASTER
DP slave 611U
SINUMERIK 802D
SINUMERIK 840Di
In the ”speed/torque setpoint” mode
(n–set mode)
Positioning and path control board
FM 357–2
(n–set mode)
SIMATIC S7–300
6ES7315–2AF03–xxxx
In the ”positioning” operating mode
(pos mode)
The clock–cycle synchronous drive coupling can be activated if all of
the prerequisites of the DP master and DP slave have been fulfilled
and the function has been selected in the DP master by appropriately
parameterizing/configuring it.
The parameters for equidistant operation are included in the slave–spe-
cific master device file SIEM808F.GSD. Parameterization is also possi-
ble via Drive ES.
The master configuring ensures, that all of the DP slaves in the applica-
tion use the same clock cycle times and processing instants.
When PROFIBUS runs–up, the information required by the DP slaves,
is transferred from the master to all of the slaves via the parameterizing
telegram.
General
information
Which clock–
synchronous
masters are there?
Activation
Parameterizing
equidistant
operation
5 Communications via PROFIBUS DP
08.99
08.01