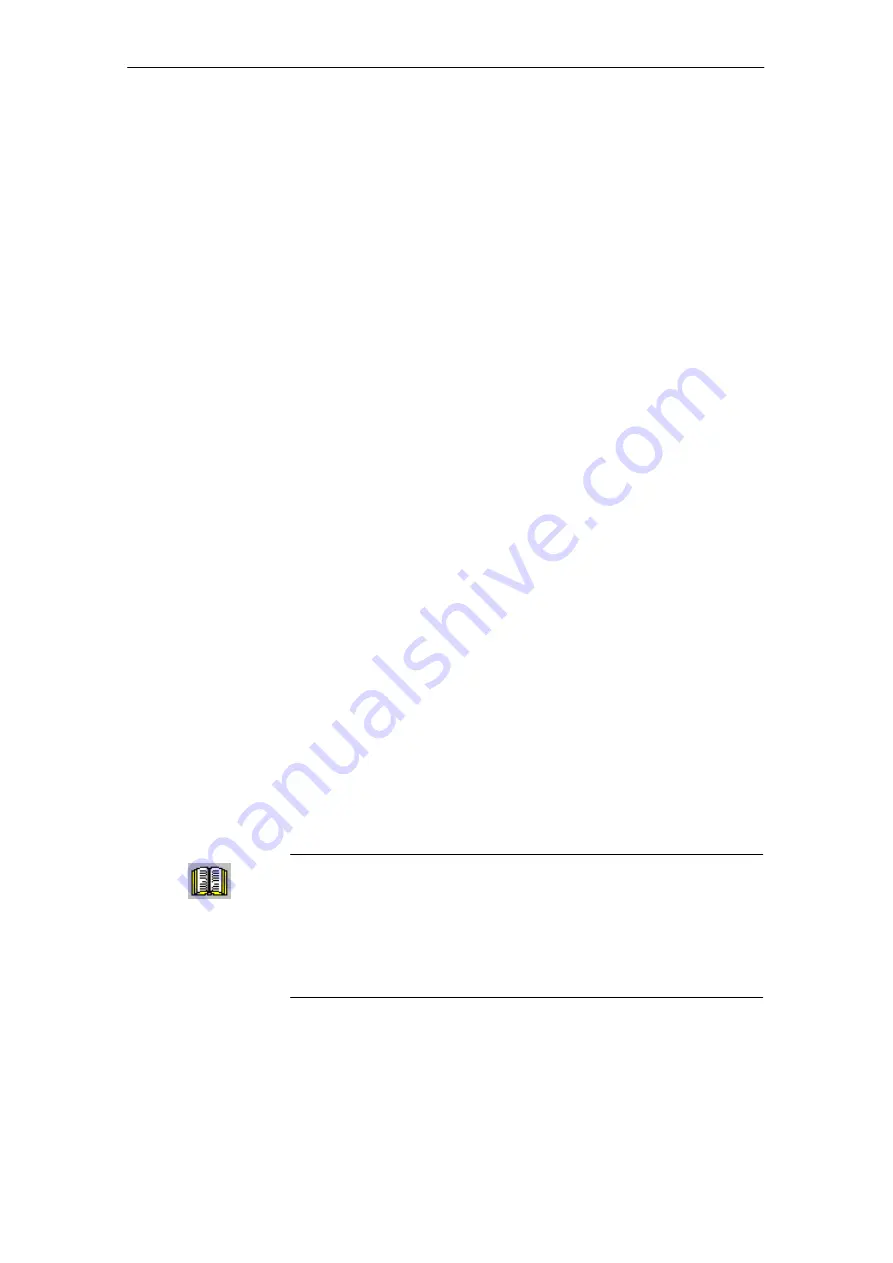
4
01.99
4.9
1FW6 build–in torque motors (from SW 6.1)
4-168
Siemens AG 2005 All Rights Reserved
SIMODRIVE 611 universal Description of Functions (FBU) – 04.05 Edition
For 1FW6 torque motors, the commutation required for synchronous
motors can be automatically set using the software–based rotor posi-
tion identification technique.
The following two techniques can be applied for all frame sizes of
1FW6 torque motors:
Saturation–based technique (from SW 5.1)
– This technique can also be used to determine the angular com-
mutation offset once in conjunction with an absolute measuring
system (e.g. RCN 723 from Heidenhain).
– This technique may only be used for horizontal axes that are free
to move and are not braked (stiction < 10 % of the rated motor
torque).
– When this technique is applied, under worst case condition, the
rotor can move in the range of
±
5 degrees.
Motion–based technique (from SW 6.1)
– This technique does not cause the rotor to move which means
that it can also be used for axes which are locked (e.g. using a
brake).
– Depending on the actual mechanical design, this can result in a
higher noise level when the axis is powered–up during the identi-
fication routine.
The measuring system must be very stiffly mounted if this technique is
used.
4.9.3
Thermal motor protection
1FW6 stators are equipped with the two following temperature monitor-
ing circuits to protect the stator against inadmissibly high thermal
stressing as well as to monitor the temperature during the commission-
ing phase and in operation:
2 x Temp–S (one switching threshold at 130
°
C and another at 150
°
C)
1 x Temp–F
Reader’s note
Detailed information on how to connect and evaluate the temperature
monitoring circuits is provided in:
Reference:
/PJTM/ Configuration Manual
1FW6 Build–in Torque Motors
Manufacturers documentation
Additional
commissioning
information/
instructions to
optimize the motor
4 Commissioning
02.03