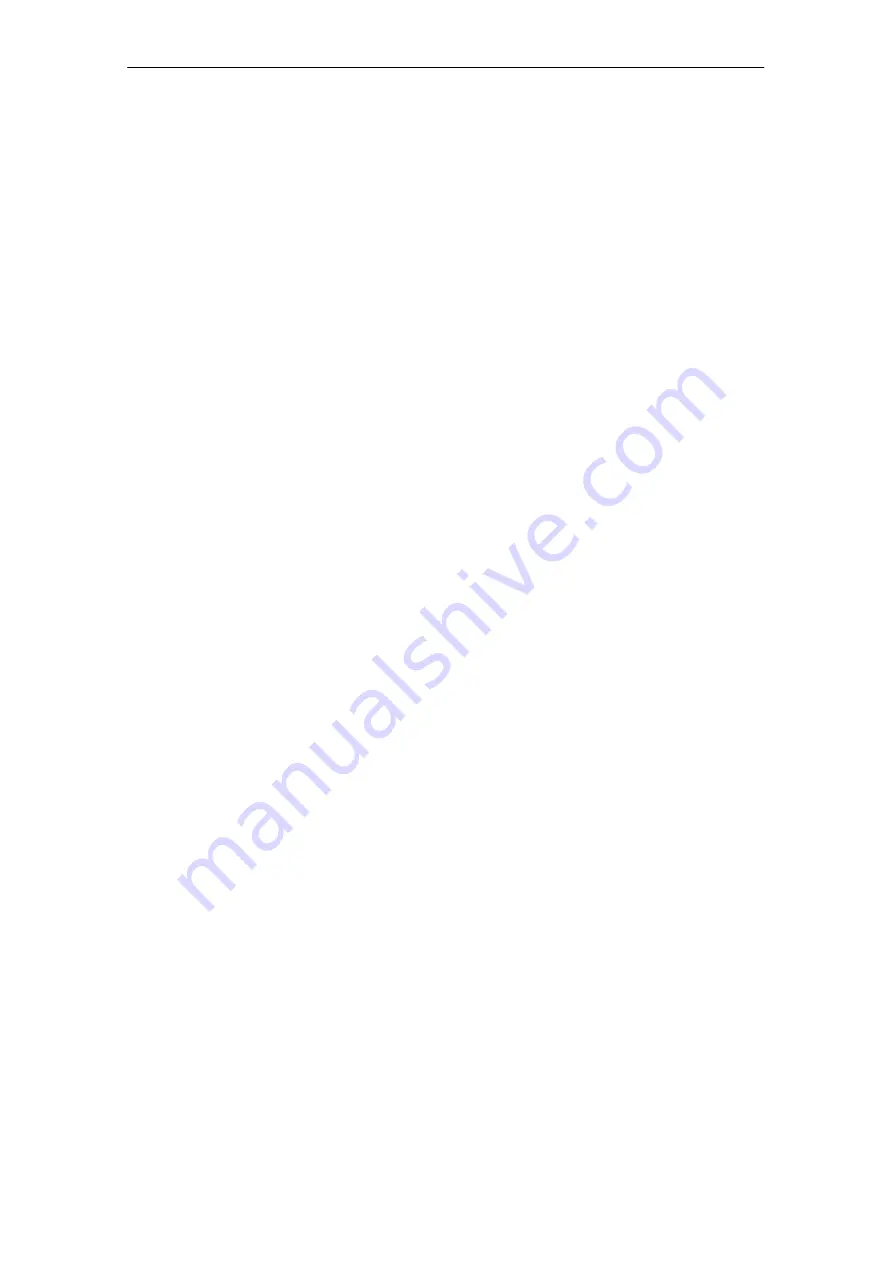
7
7.3
List of faults and warnings
7-630
Siemens AG 2005 All Rights Reserved
SIMODRIVE 611 universal Description of Functions (FBU) – 04.05 Edition
002
Computation time overflow. Suppl. info: \%X
Cause
The computation time of the drive processor is no longer sufficient for
the selected functions in the specified cycle times.
Supplementary information: only for siemens-internal error diagnostics
Remedy
Disable functions which take up a lot of computation time, e.g.:
– Variable signaling function (P1620)
– Trace function
– Start-up with FFT or analyzing the step response
– Speed feedforward control (P0203)
– Min/Max memory (P1650.0)
– DAC output (max. 1 channel)
Increase cycle times:
– Current controller cycle (P1000)
– Speed controller cycle (P1001)
– Position controller cycle (P1009)
– Interpolation cycle (P1010)
Acknowledgement POWER ON
Stop response
STOP II (SRM, SLM) STOP I (ARM)
003
NMI due to watchdog. Suppl. info: \%X
Cause
The watchdog timer on the control module has expired. The cause is a
hardware fault in the time basis on the control module.
Supplementary information: only for siemens-internal error diagnostics
Remedy
– Replace control module
Acknowledgement POWER ON
Stop response
STOP II (SRM, SLM) STOP I (ARM)
004
Stack overflow. Suppl. info: \%X
Cause
The limits of the internal processor hardware stack or the software
stack in the data memory have been violated. The cause is probably a
hardware fault on the control module.
Supplementary information: only for siemens-internal error diagnostics
Remedy
– Power down/power up drive module
– Replace control module
Acknowledgement POWER ON
Stop response
STOP II (SRM, SLM) STOP I (ARM)
005
Illegal Opcode, Trace, SWI, NMI (DSP). Suppl. info: \%X
Cause
The processor has detected an illegal command in the program
memory.
Supplementary information: only for siemens-internal error diagnostics
Remedy
– Replace control module
Acknowledgement POWER ON
Stop response
STOP II (SRM, SLM) STOP I (ARM)
7 Fault Handling/Diagnostics
01.99
04.05