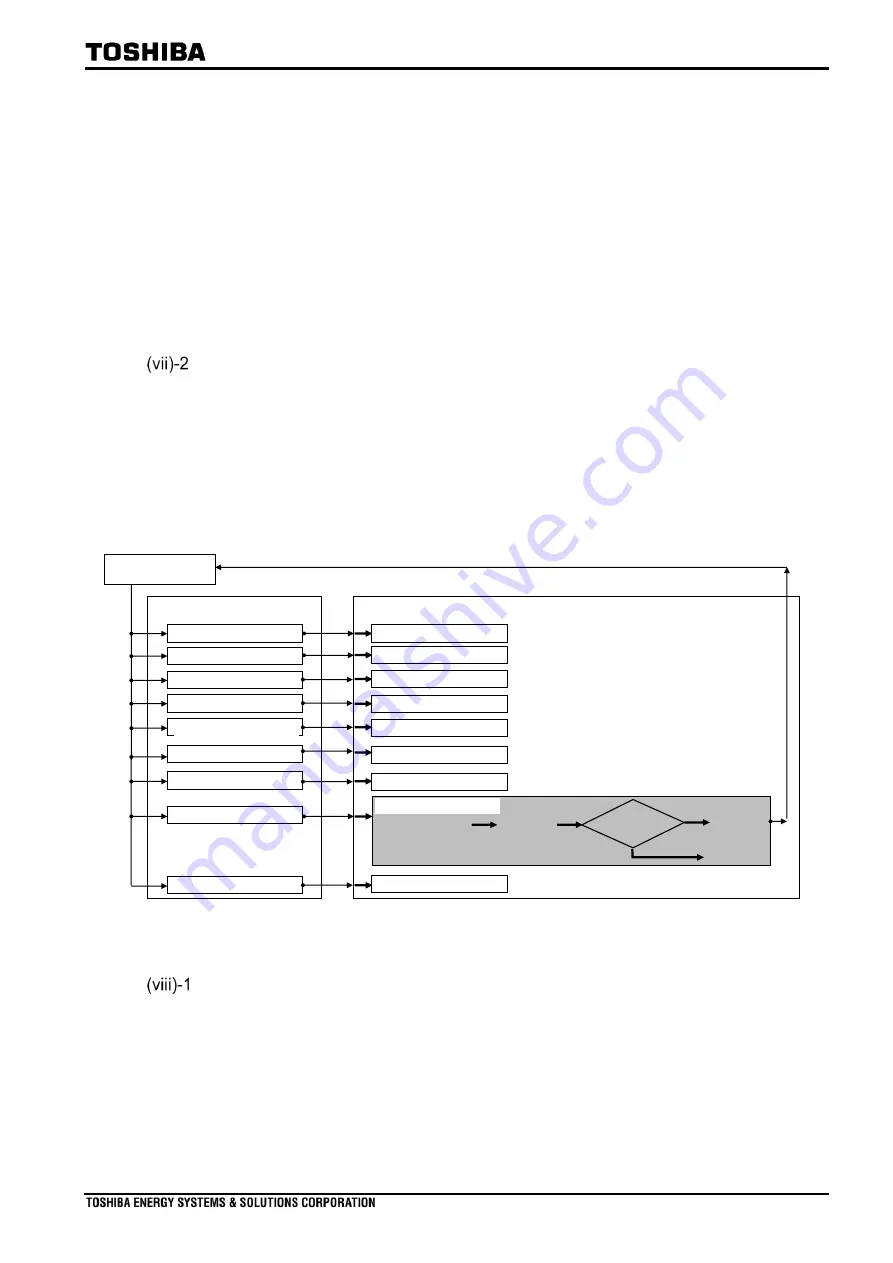
6F2S1915 (0.46)
GRZ200 (Soft 031 & 032)
- 825 -
‡‡Note: The “Operate failed” signal is issued when a state-change remains undetected
failing expiration of the setting applied to timer [
TPOS01-RST
]
§§Note: The “TPOS01-PIEX-BO” signal is issued when
Fixlogic
is set the scheme switch
[
TPOS01-LGP1EXOT
]. If the signal to be issued from the logic programmed by the
user instead of the logic shown in Figure 4.9-26, connect the “operate completed”
signal generated in the user-programmed logic to connection point#2 “User
configurable condition”. That is, set
PLC
to the scheme switch [
TPOS01-
LGP1EXOT
] and use “TPOS01IN_TMP_38”.
Output signal to BO
The TPOS01 function, in Figure 4.9-39, can issue a “Operate P1-control” signal at output point
“TPOS01_P1EX_BO”, when the TPOS01 function determines that the signal “PLC-P1-Control”
is true.
(viii)
Receiving “operate command P2-control” using the PLC function
Figure 4.9-40 depicts the reception of the operate command “P2-control’ using the PLC function.
Signal generation by the
PLC function
P2 control by the PLC function
Do nothing
Operation
decision
Success
Failed
Operate logic
P1 control from the remote-end
P2 control from the remote-end
P3 control from the remote end
P1 control from the local-end
P3 control from the local-end
P2 control from the local-end
P1 control by the PLC function
Wait for a command
P2 control by the PLC function
P3 control by the PLC function
Select logics
Signal output
P3 control from the remote end
P1 control from the local-end
P1 control from the remote-end
P2 control from the remote-end
P2 control from the local-end
P3 control from the local-end
P1 control by the PLC function
P3 control by the PLC function
Wait for a next command
Figure 4.9-40 Outline of Operate command ‘P2-control’ function
Input signal from the PLC function
Figure 4.9-41 depicts the operation logic when an “Operate command P2 (PLC-P2-Control)”
signal is generated by the PLC function. There are two input points for the reception of this
command signal, like in the “Operate command P2 (PLC-P2-Control)” signal. That is, if an
interlock check is required, apply the signal at connection point (PLC#3:i.e.,
DEV01_P2_INTERLOCK). On the other hand, if an interlock check is not required, apply the
signal at connection point (PLC#4:i.e., DEV01_P2_COMMAND). PLC#3 and PLC#4 here are
Summary of Contents for GR 200 Series
Page 1047: ...6F2S1915 0 46 GRZ200 Soft 031 032 1026 Figure 8 3 4 Screen shot from GR TIEMS ...
Page 1354: ...6F2S1915 0 46 GRZ200 Soft 031 032 1333 Appendix 1 Signal list for common function ...
Page 1410: ...6F2S1915 0 46 GRZ200 Soft 031 032 1389 This page is intentionally blank ...
Page 1480: ...6F2S1915 0 46 GRZ200 Soft 031 032 1459 Appendix 6 Ordering ...
Page 1497: ...6F2S1915 0 46 GRZ200 Soft 031 032 1476 Appendix 7 Technical data ...
Page 1518: ...6F2S1915 0 46 GRZ200 Soft 031 032 1497 Appendix 8 Manufacture setting ...
Page 1523: ...6F2S1915 0 46 GRZ200 Soft 031 032 1502 Appendix 10 CT requirement ...
Page 1531: ...6F2S1915 0 46 GRZ200 Soft 031 032 1510 Appendix 12 Engineering exercise ...
Page 1563: ......