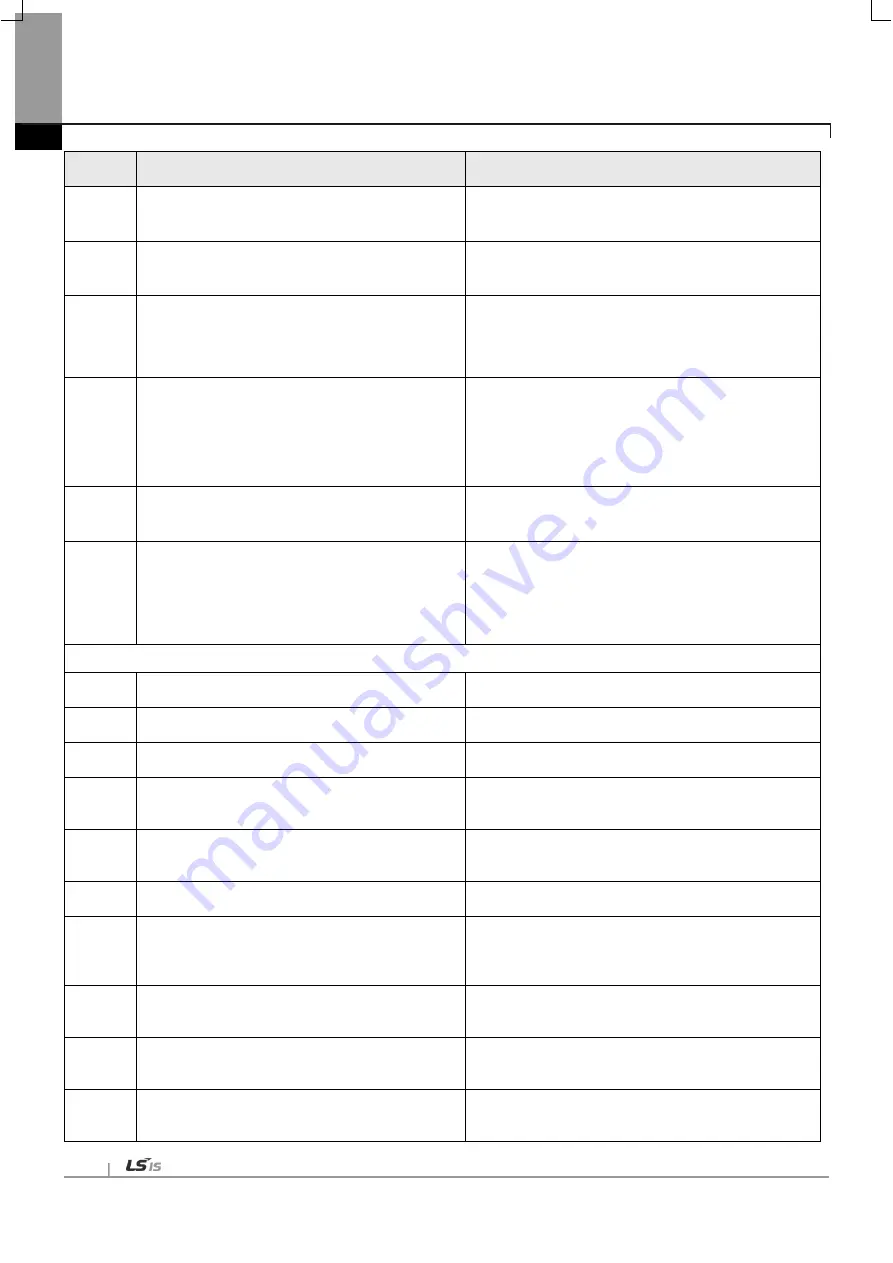
Appendix 1 Positioning Error Information & Solutions
Error
Code
Error Description
Solutions
597
There is no r esponse of the servo driver on
“servo parameter EEPROM save” command.
Check if servo driver is normal or not.
598
The axis for
“
Servo parameter EEPROM
save
”
is not connected now.
It can execute “Servo parameter EEPROM save”
command only for currently connected axis.
599
Unable to carry out other commands during
“Servo parameter write” or “Servo parameter
EEPRO save”
Execute other commands after completing “Servo
parameter write” or “Servo parameter EEPROM
save”.
600
“Abort” arises during “servo parameter read”
command
Check if parameter is readable or parameter
number and setting data is within range.
Sometimes you can’t read parameter according to
servo driver status.
601
There is no r esponse of the servo driver on
“servo parameter read” command.
Check if servo driver is normal or not.
602
It is not possible to execute the “Servo
parameter read/write” or “Servo parameter
save” command in the state that servo
parameter read command is executing.
Execute command when servo parameter read
command is completed.
701
Not possible to carry out CAM command in the
state of in operation.
Execute CAM command when main axis is not
operating.
702
Not possible to carry out CAM command in the
state of M Code ON
Execute CAM command after set M Code OFF
from commanding axis with MOF.
703
Not possible to carry out CAM command in the
state that servo is OFF.
Execute CAM command when Servo On signal is
“ON.”
704
Error of setting main/subordinate axis from
CAM command.
Set main axis for CAM command as other axis
besides its command axis from connecting axis.
Set parameters are 1axis through 8axis.
706
Error of CAM block setting from CAM
command.
Execute CAM command after set a CAM block
from CAM command as bigger than 1 and
smaller than 8.
707
Error for CAM data of appointed block from
CAM command.
Execute CAM command after set right data for
appointed block from CAM command.
708
The speed of subordinate axis from CAM
command cannot exceed its speed limit.
Set lower speed for main axis so that speed
of subordinate axis from CAM data which is
calculated by subordinate position would not
exceed its speed limit.
709
For CAM command, in case main axis is
encoder, main axis unit f CAM data should be
pulse.
When you set the main axis of CAM data as
encoder, set the unit of main axis of CAM block as
pulse.
710
Movement position per control cycle is out of
main axis range of CAM data because high
speed of main axis of CAM command.
Operate with lower speed of main axis.
711
Data area setting value (block size and no. of
block) of Variable Data Read/Write command
is out of range.
Set the block size and no. of block for [block size X
no. of block] to be 1~128.
A1-14
Summary of Contents for XBF-PN04B
Page 1: ...Programmable Logic Controller Positioning Module EtherCAT XGB Series XBF PN04B XBF PN08B ...
Page 626: ...Chapter 9 Functions BPS37 setup RS232 and PC connection BPS37 option board LED 9 193 ...
Page 796: ...Appendix3 Dimension A3 1 Appendix 3 Dimension Appendix 3 1 Dimension of XBF PN04B PN08B ...