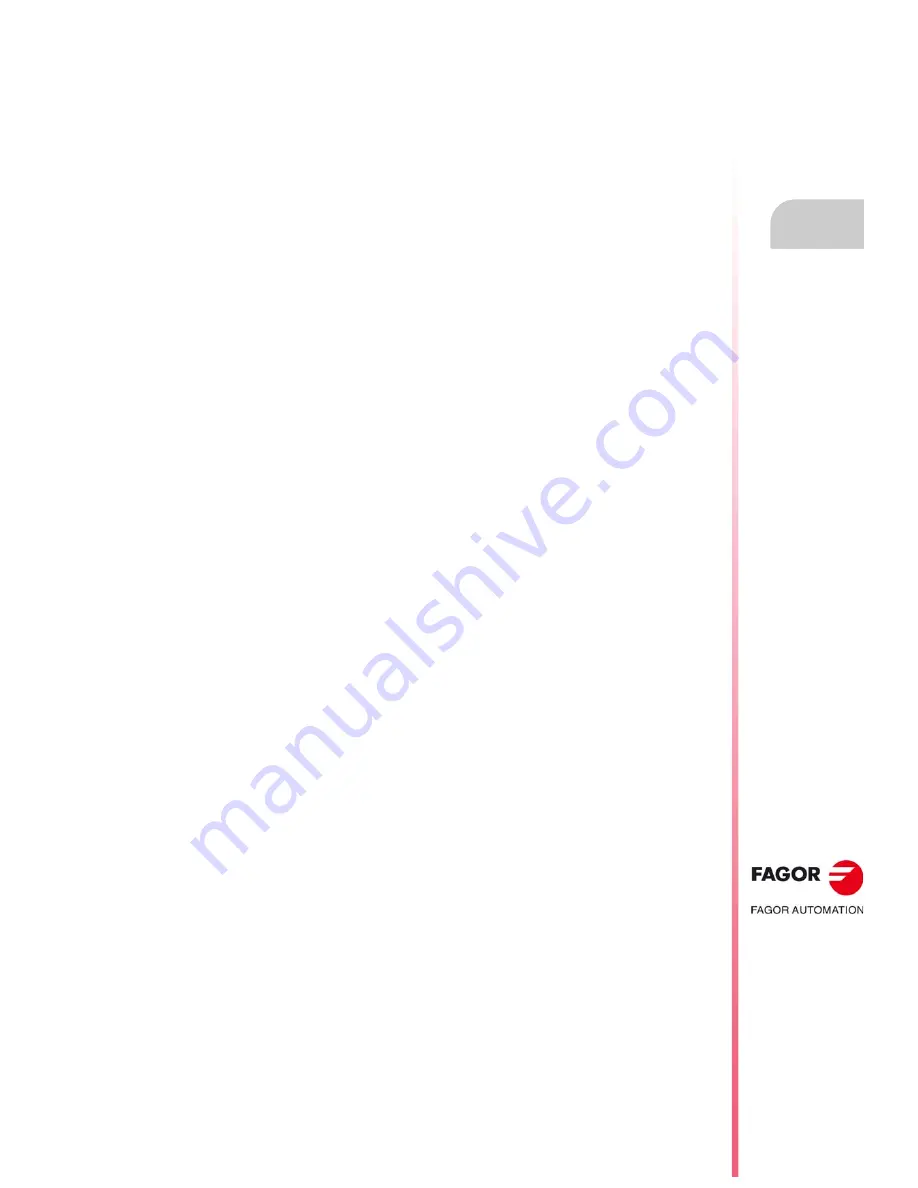
Error solving manual.
CNC 8060
CNC 8065
·53·
(R
EF
: 1709)
1429
'Too many subroutines in the same block'
DETECTION
During execution.
CAUSE
The maximum number of subroutines that may be executed in the same block has
been exceeded.
SOLUTION
The maximum number of subroutines that may be executed in the same block is 5.
Program the subroutines in different blocks or use subroutine nesting as necessary.
1430
'Numeric format exceeded'
DETECTION
During execution.
CAUSE
The value assigned to a data, variable or parameter exceeds the established format.
SOLUTION
Check the program.
1431
'Wrong spindle position in M19'
DETECTION
During execution.
CAUSE
The value programmed for the spindle position in M19 is too high.
SOLUTION
Program a smaller value.
1432
'A slave axis of a Gantry or coupling cannot be programmed'
DETECTION
During execution.
CAUSE
In instruction contains the slave axis of an active coupling or of Gantry pair.
SOLUTION
In order to operate with the axis in those instructions, deactivate the active coupling
(#UNLINK) or undo the Gantry pair (by machine parameter).
1433
'A parked axis cannot be part of the main plane'
DETECTION
During execution.
CAUSE
The CNC has tried to include (#CALL / #SET) a parked axis between the first three
axes of the channel.
SOLUTION
A parked axis cannot be part of the first of three axes of the channel; unpark the axis
(#UNPARK).
1434
'An associated slave axis could not be included in the configuration'
DETECTION
During execution.
CAUSE
The CNC has tried to include the master axis of an active coupling or that of a Gantry
pair in the channel configuration (#CALL or #SET). When including the master axis,
the CNC also includes the slave axis which can never occupy one of the main three
positions of the channel. The CNC issues an error because there is no free position
other than the main three axis.
SOLUTION
In order to only include the master axis, the active coupling must be deactivated first
(#UNLINK) or undo the Gantry pair. In order to include both the master and the slave
axis, first eliminate another axis from the channel or increase the number of axes of
the channel.
1435
'An associated slave axis could not be assigned a name because it was repeated'
DETECTION
During execution.
CAUSE
The CNC has tried to include the master axis of an active coupling or that of a Gantry
pair in the channel configuration (#CALL or #SET). When including the master axis,
the CNC also includes the slave axis which can never occupy one of the main three
positions of the channel. The CNC issues an error because the name of the slave
axis is already occupied by another axis of the current configuration of the channel.
SOLUTION
Rename either the slave axis to be included or the one that already exists in the
configuration.
1436
'The stop block has not been programmed in the block search'
DETECTION
During execution.
CAUSE
The stop block of the block search is missing.
SOLUTION
Once the block search option has been selected, the softkey menu shows the option
to select the stop block. Select the block where the block search will end.
1439
'The axes of the active transformation cannot be Hirth'
DETECTION
During execution.
CAUSE
The CNC has tried to activate a coordinate transformation (#TLC, #RTCP, #TOOL
ORI, #CS or #ACS), but one of the axes involved in the transformation is a Hirth axis.
SOLUTION
A hirth axis must not be part of the coordinate transformation. An axis involved in the
transformation must not be a Hirth axis (G170).
Summary of Contents for 8065
Page 1: ...Ref 1709 8060 8065 CNC Error solving manual...
Page 4: ...BLANK PAGE 4...
Page 216: ...Error solving manual CNC 8060 CNC 8065 216 REF 1709...
Page 217: ...Error solving manual CNC 8060 CNC 8065 217 User notes REF 1709...
Page 218: ...Error solving manual CNC 8060 CNC 8065 218 User notes REF 1709...
Page 219: ...Error solving manual CNC 8060 CNC 8065 219 User notes REF 1709...