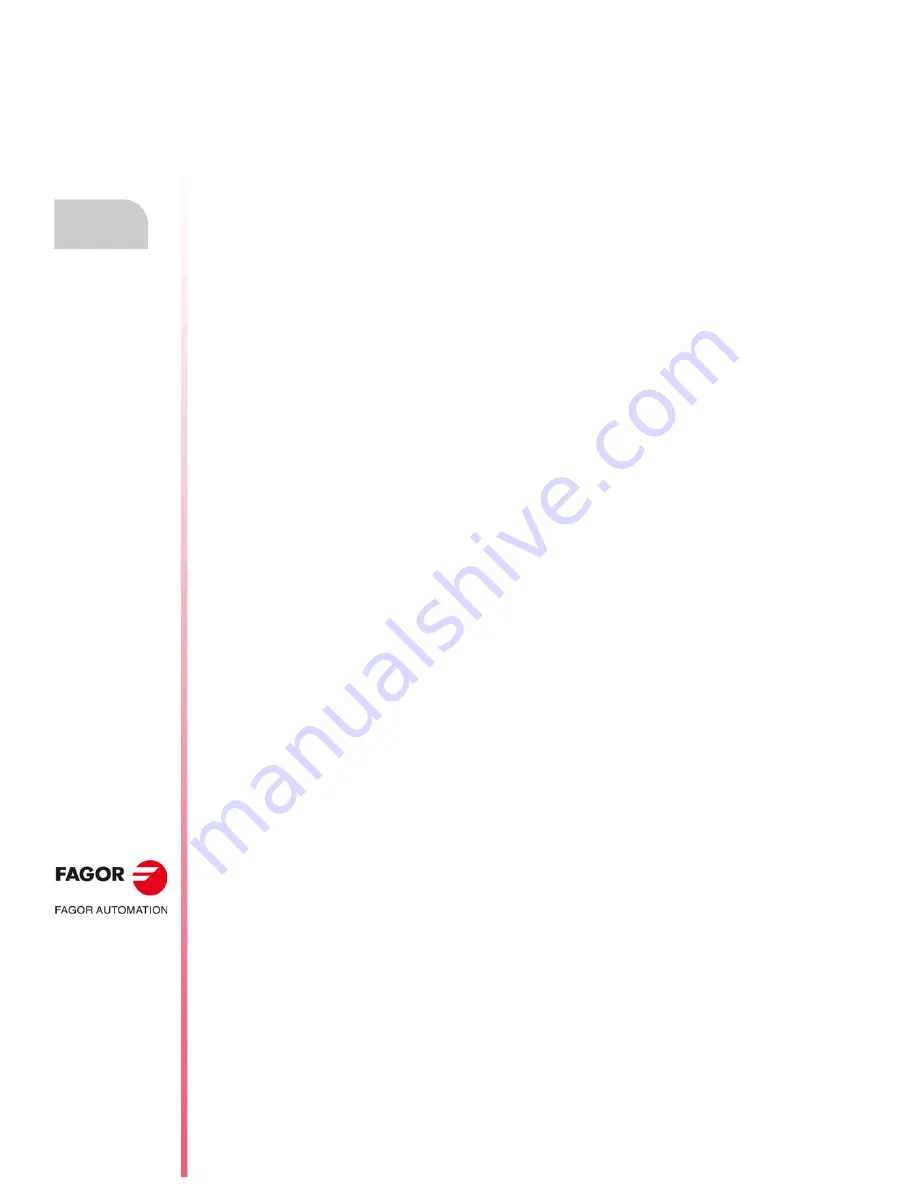
Error solving manual.
CNC 8060
CNC 8065
·40·
(R
EF
: 1709)
1266
'The TLC feature is deactivated using the instruction #TLC OFF'
DETECTION
During execution.
CAUSE
The CNC has tried to modify the TLC function while it was active.
SOLUTION
The CNC does not allow modifying the TLC function while it is active. To modify the
TLC function, first deactivate it and then activated again.
1267
'The RTCP functionality is canceled with the instruction #RTCP OFF'
DETECTION
During execution.
CAUSE
While RTCP is active, a #RTCP instruction other than #RTCP OFF has been
programmed.
SOLUTION
To cancel the RTCP function, program #RTCP OFF. To change the values of the
RTCP, it must be canceled first.
1268
'#CS ON/#ACS ON: syntax error'
DETECTION
During execution.
CAUSE
The syntax of the instruction is wrong.
SOLUTION
Check the program.
1269
'#CS ON/#ACS ON: the programmed angle is not valid'
DETECTION
During execution.
CAUSE
The programmed angle is wrong.
SOLUTION
Program an angle within ±360º.
1270
'The coordinate transformation cannot be calculated'
DETECTION
During execution.
CAUSE
The CNC has not been able to solve a transformation from part-coordinates to
machine coordinates or vice versa.
SOLUTION
Cancel the transformation, change the position of the axes and activate the
transformation again.
1271
'The axes of the active kinematics can neither be excluded nor modified'
DETECTION
During execution.
CAUSE
The CNC has tried to modify the configuration of the axes of a kinematics while it was
active.
SOLUTION
Cancel the kinematics before modifying the configuration of the axes of the channel.
1272
'The axes of the active transformation can neither be excluded nor modified'
DETECTION
During execution.
CAUSE
The CNC has tried to modify the configuration of the axes of an inclined plane while
it was active.
SOLUTION
Cancel the inclined plane transformation to modify the configuration of the axes of
the channel.
1275
'Position calculated by the inverted kinematics transformation out of range'
DETECTION
During execution.
CAUSE
The CNC has tried to do an unsolved transformation from machine coordinates to
part coordinates.
SOLUTION
Cancel the transformation, change the position to be accessed and activate the
transformation again. Check the transformation if it is a user transformation.
1277
'The resulting zero offset exceeds the data range'
DETECTION
During execution.
CAUSE
The zero offset calculated from the coordinates programmed in function G92 is too
large.
SOLUTION
Check the program.
1278
'G131/G133: wrong value'
DETECTION
During execution.
CAUSE
In function G131 or G133, the programmed percentage of acceleration or jerk is not
valid.
SOLUTION
Program a percentage of acceleration or jerk that is positive and less than or equal
to 100.
Summary of Contents for 8065
Page 1: ...Ref 1709 8060 8065 CNC Error solving manual...
Page 4: ...BLANK PAGE 4...
Page 216: ...Error solving manual CNC 8060 CNC 8065 216 REF 1709...
Page 217: ...Error solving manual CNC 8060 CNC 8065 217 User notes REF 1709...
Page 218: ...Error solving manual CNC 8060 CNC 8065 218 User notes REF 1709...
Page 219: ...Error solving manual CNC 8060 CNC 8065 219 User notes REF 1709...