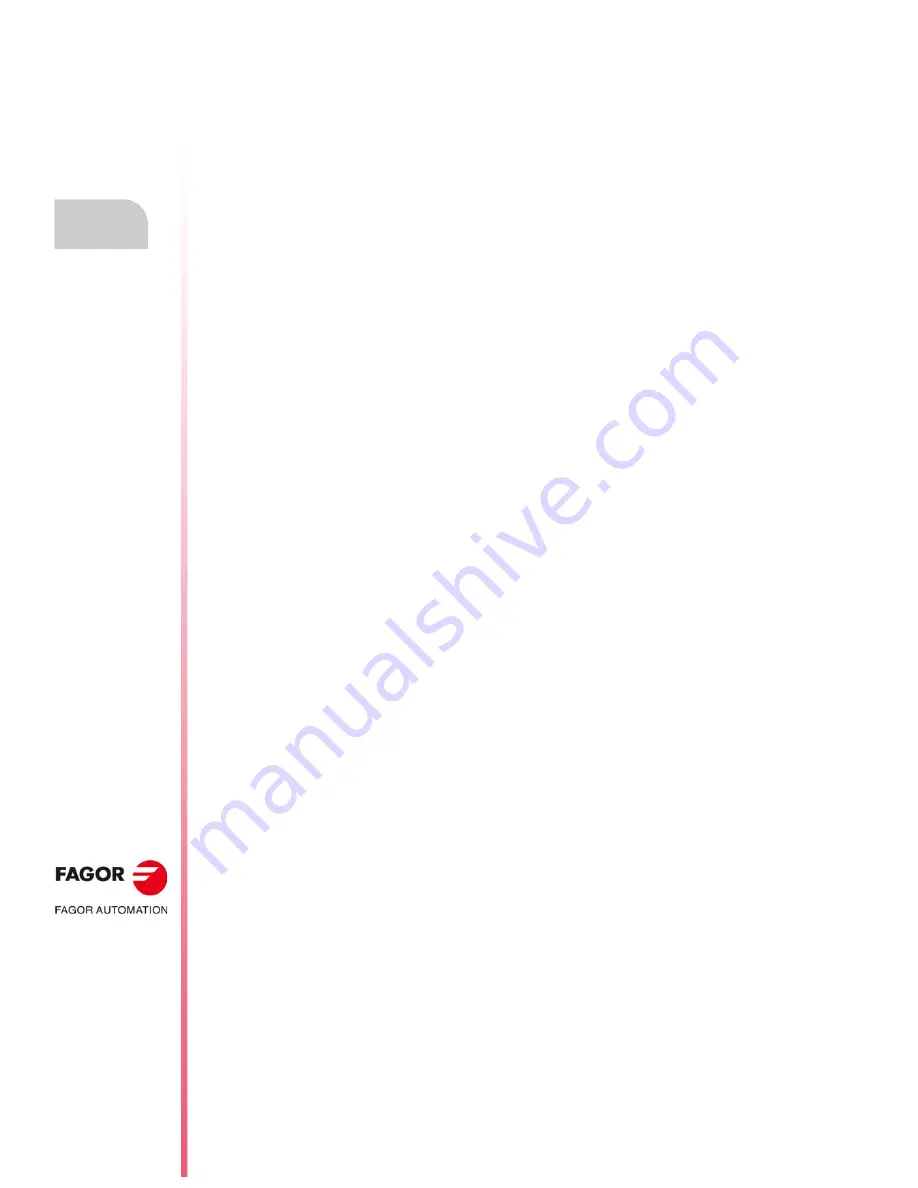
Error solving manual.
CNC 8060
CNC 8065
·74·
(R
EF
: 1709)
1647
'The gear does not exist in the TANDEM slave'
DETECTION
During execution.
CAUSE
A gear change has been programmed in a tandem axis or spindle. The gear exists
in the master axis or spindle, but not in the slave.
SOLUTION
Define the same gears on the master and slave axes and spindles of the tandem.
1649
'User reverse transformation function not found'
DETECTION
During execution.
CAUSE
The PcsToMcs coordinates function is missing when trying to do a transformation
from part coordinates to machine coordinates in a user kinematics.
SOLUTION
Check the user kinematics integration process.
1650
'User direct transformation function not found'
DETECTION
During execution.
CAUSE
The McsToPcs coordinates function is missing when trying to do a transformation
from machine coordinates to part coordinates in a user kinematics.
SOLUTION
Check the user kinematics integration process.
1651
'Maintained LINK not admitted with temporary axes of another channel'
DETECTION
During execution.
CAUSE
The CNC cannot couple axes with temporary exchange permission (parameter
AXISEXCH) if they belong to another channel and the couplings of the channel are
defined as maintained (parameter LINKCANCEL).
SOLUTION
Couple the axes in their channel.
1653
'An axis of the inclined plane transformation cannot be a slave'
DETECTION
During execution.
CAUSE
The CNC has tried to define as slave of a coupling an axis that belongs to the inclined
plane.
SOLUTION
Cancel the inclined plane to be able to activate the coupling. An axis that belongs to
the inclined plane cannot be the slave axis of a coupling; but the master of a coupling
can.
1654
'Digital bus (Sercos/Mechatrolink)not ready for reading the variable'
DETECTION
During execution.
CAUSE
With the Sercos bus, the ring is not in phase 4. With the Mechatrolink bus, the bus
has not reached phase 3.
The Sercos ring is not in phase 4.
SOLUTION
Condition the writing of the variable to the SERCOSRDY mark in Sercos or to the
MLINKRDY mark in Mechatrolink.
1655
'Digital bus (Sercos/Mechatrolink)not ready for writing the variable'
DETECTION
During execution.
CAUSE
With the Sercos bus, the ring is not in phase 4. With the Mechatrolink bus, the bus
has not reached phase 3.
SOLUTION
Condition the writing of the variable to the SERCOSRDY mark in Sercos or to the
MLINKRDY mark in Mechatrolink.
1656
'Some axis of the plane is set in diameters'
DETECTION
When simulating or executing on a lathe a milling canned cycle that contains
movements in the axes of the plane.
CAUSE
The coordinate data of the milling canned cycles will be considered in radius. If any
of the axes of the plane is in diameters, the CNC interprets its data as radius and
warns the user in case he was programming them in diameters.
CONSEQUENCE The cycle can execute a different geometry than expected.
SOLUTION
Program the data in radius.
1657
'Wrong variable for spindle that is not a C axis'
DETECTION
During execution.
CAUSE
The CNC has tried to read an axis variable, but the spindle is activated as C axis.
SOLUTION
The variable only exists for axes and spindles working as C axis.
Summary of Contents for 8065
Page 1: ...Ref 1709 8060 8065 CNC Error solving manual...
Page 4: ...BLANK PAGE 4...
Page 216: ...Error solving manual CNC 8060 CNC 8065 216 REF 1709...
Page 217: ...Error solving manual CNC 8060 CNC 8065 217 User notes REF 1709...
Page 218: ...Error solving manual CNC 8060 CNC 8065 218 User notes REF 1709...
Page 219: ...Error solving manual CNC 8060 CNC 8065 219 User notes REF 1709...