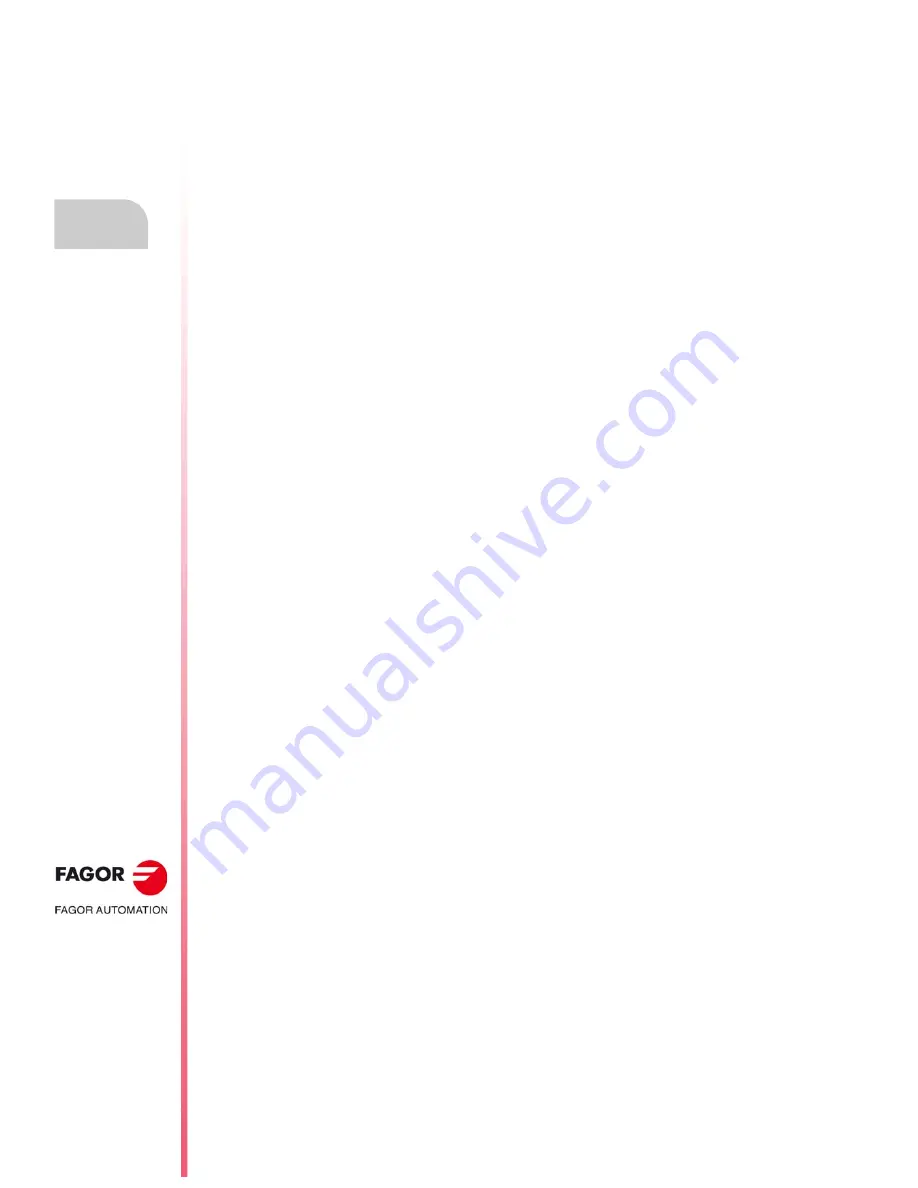
Error solving manual.
CNC 8060
CNC 8065
·10·
(R
EF
: 1709)
0062
'The continuous Jog feedrate exceeds the maximum feedrate set for the axis'
DETECTION
During the validation of the machine parameters.
CAUSE
Parameter JOGFEED is greater than G00FEED.
SOLUTION
Decrease the value of parameter JOGFEED; it must be lower than G00FEED.
0063
'The incremental jog feedrate exceeds the maximum feedrate set for the axis'
DETECTION
During the validation of the machine parameters.
CAUSE
Parameter INCJOGFEED is greater than G00FEED.
SOLUTION
Decrease the value of parameter INCJOGFEED; it must be lower than G00FEED.
0064
'The master and slave axes must have the same I0TYPE'
DETECTION
During the validation of the machine parameters.
CAUSE
The Io types of both gantry axes are not the same.
SOLUTION
Both axes must have the same type of reference mark (parameter I0TYPE).
0065
'A Hirth axis cannot be Gantry"
DETECTION
During the validation of the machine parameters.
CAUSE
'A hirth axis cannot be part of the gantry axis'
SOLUTION
'The axis cannot be a hirth axis (parameter HIRTH). Use another type of axis to make
the gantry axis.
0066
'A Gantry axis cannot have REFSHIFT'
DETECTION
During the validation of the machine parameters.
CAUSE
One of the axes making up the gantry axis has parameter REFSHIFT set to a value
other than zero in some set of parameters.
SOLUTION
Set parameter REFSHIFT all the sets to 0.
0067
'A Gantry axis cannot be unidirectional'
DETECTION
During the validation of the machine parameters.
CAUSE
A unidirectional rotary axis cannot be part of the gantry axis.
SOLUTION
The axis cannot be unidirectional (parameter UNIDIR). Use another type of axis to
make the gantry axis.
0068
'Gantry/Tandem axes: the slave cannot go before the master in AXISNAME'
DETECTION
During the validation of the machine parameters.
CAUSE
The slave axis is defined before the master axis in the axis name assigning tables
(parameter AXISNAME).
SOLUTION
In the table, define the master axis before the slave axis or swap the master and slave
axes in the gantry or tandem pair.
0069
'Gantry axes: The slave cannot have DECINPUT (home switch) if the master does not
have one'
DETECTION
During the validation of the machine parameters.
CAUSE
The slave axis of a gantry axis has a home switch but the master axis doesn't.
SOLUTION
In a gantry axis, there may be a home switch on the master axis, on both axes or on
none (parameter DECINPUT).
0070
'Gantry/Tandem axes: LIMIT+ and LIMIT- must be the same for the master and the slave '
DETECTION
During the validation of the machine parameters.
CAUSE
In a gantry or tandem pair, the software travel limits are different on the two axes.
SOLUTION
Set both axes with the same software travel limits (parameters LIMIT+ and LIMIT-).
0071
'Following error monitoring is not active at the CNC'
DETECTION
During the validation of the machine parameters.
CAUSE
In some set of parameters, following error monitoring is not active. This situation can
only be allowed during setup; once setup is completed, this watch must be enabled.
SOLUTION
Activate the following error monitoring in all sets of parameters (parameter
FLWEMONITOR).
Summary of Contents for 8065
Page 1: ...Ref 1709 8060 8065 CNC Error solving manual...
Page 4: ...BLANK PAGE 4...
Page 216: ...Error solving manual CNC 8060 CNC 8065 216 REF 1709...
Page 217: ...Error solving manual CNC 8060 CNC 8065 217 User notes REF 1709...
Page 218: ...Error solving manual CNC 8060 CNC 8065 218 User notes REF 1709...
Page 219: ...Error solving manual CNC 8060 CNC 8065 219 User notes REF 1709...