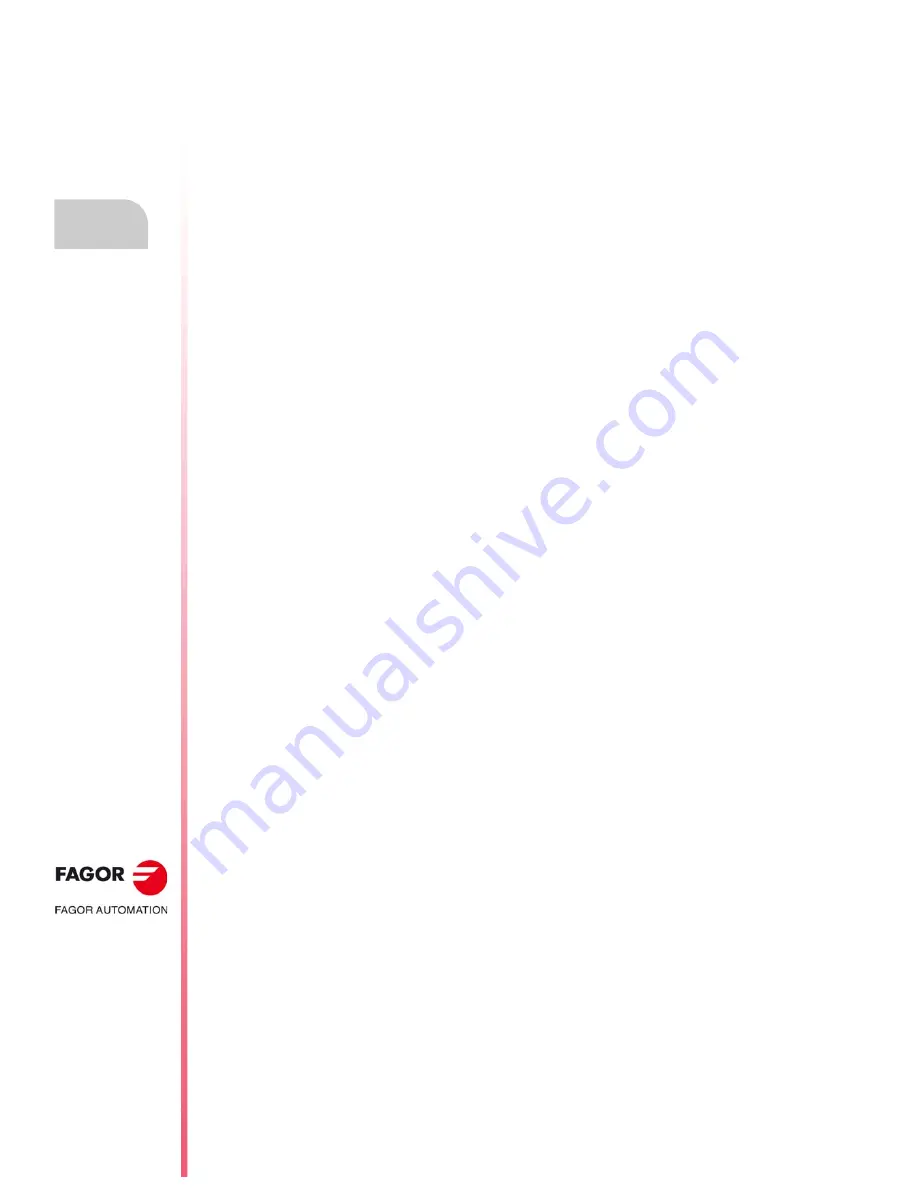
Error solving manual.
CNC 8060
CNC 8065
·132·
(R
EF
: 1709)
3503
'Linear acceleration of section 2 greater than the maximum'
DETECTION
During startup or execution.
CAUSE
The programmed acceleration is greater than the maximum.
SOLUTION
Program a smaller value than the maximum for the acceleration.
3504
'Acceleration changing speed higher than the maximum'
DETECTION
During startup or execution.
CAUSE
The speed programmed for the acceleration change speed is higher than the
maximum.
SOLUTION
Program a lower speed than the maximum.
3505
'Jerk limit overshoot'
DETECTION
During execution.
CAUSE
Jerk overshoot on this path.
SOLUTION
Contact Fagor.
3506
'The Jerk limit will be exceeded'
DETECTION
During the execution of the command to analyze the frequencies.
CAUSE
The frequency is too high for the programmed amplitude.
SOLUTION
Decrease the maximum frequency or decrease the amplitude.
3507
'Acceleration limit exceeded'
DETECTION
During execution.
CAUSE
Too much acceleration on this path.
SOLUTION
Contact Fagor.
3508
'Frequency too high for the programmed speed'
DETECTION
During the execution of the command to analyze the frequencies.
CAUSE
The additive speed is lower than the one resulting for the maximum frequency.
SOLUTION
Decrease the maximum frequency or program a higher additive speed.
3600
'Zero spindle speed'
DETECTION
During execution.
CAUSE
No spindle positioning speed has been programmed.
SOLUTION
Check the programming and make sure that parameters REFFEED2 and G00FEED
of the active spindle gear are not zero.
3601
'Programmed spindle speed greater than the maximum limit'
DETECTION
During execution.
CAUSE
The speed programmed for the spindle exceeds the maximum speed defined in the
machine parameters for the active gear.
SOLUTION
Check spindle parameter G00FEED.
3602
'The spindle cannot be moved in DRO mode'
DETECTION
During execution.
CAUSE
The CNC tries to control an axis that is in DRO mode.
SOLUTION
The CNC cannot control the spindles that are active in DRO mode. To move the axis,
cancel the DRO mode [PLC mark DRO(axis)] and check the status of the SERVOON
mark of the spindle.
3603
'The commanded spindle position exceeds the module range'
DETECTION
During execution.
CAUSE
The CNC is trying to position the spindle in a position that is out of the permitted range
(parameters MODUPLIM and MODLOWLIM).
SOLUTION
Check parameters MODUPLIM and MODLOWLIM
3604
'Spindle positioning direction contrary to the setting of the machine parameter'
DETECTION
During execution.
CAUSE
The programmed positioning movement requires a spindle movement in the opposite
direction to what has been set by machine parameter UNIDIR.
SOLUTION
Check the program and spindle machine parameter UNIDIR.
Summary of Contents for 8065
Page 1: ...Ref 1709 8060 8065 CNC Error solving manual...
Page 4: ...BLANK PAGE 4...
Page 216: ...Error solving manual CNC 8060 CNC 8065 216 REF 1709...
Page 217: ...Error solving manual CNC 8060 CNC 8065 217 User notes REF 1709...
Page 218: ...Error solving manual CNC 8060 CNC 8065 218 User notes REF 1709...
Page 219: ...Error solving manual CNC 8060 CNC 8065 219 User notes REF 1709...