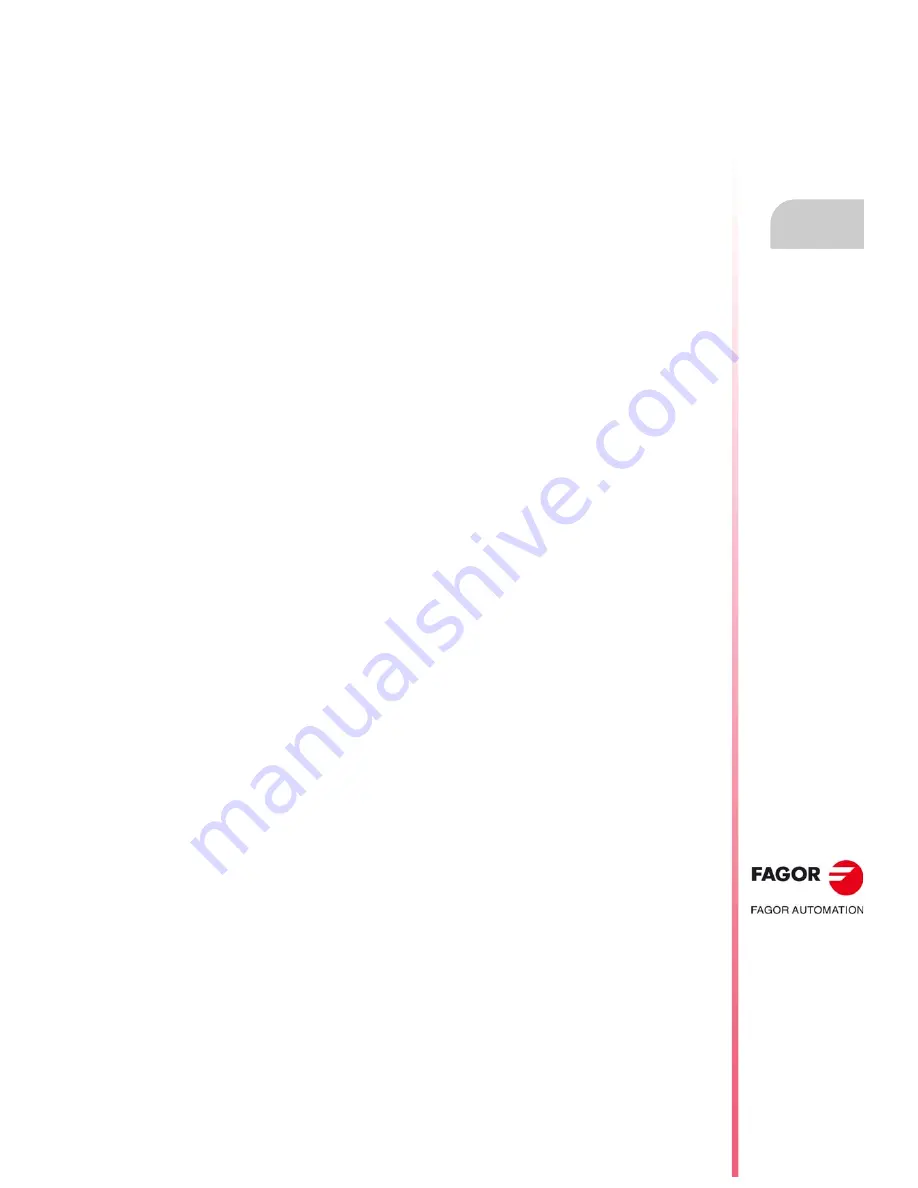
Error solving manual.
CNC 8060
CNC 8065
·5·
(R
EF
: 1709)
0000-0999
0001
'SYSTEM ERROR'
DETECTION
During execution.
CAUSE
Software or hardware errors that cause corrupt data and/or incoherent results.
SOLUTION
This type of errors usually force the CNC output. If the error persists, contact your
supplier.
0002
'SYSTEM WARNING'
DETECTION
During execution.
CAUSE
Warning of internal situations that could become system errors.
SOLUTION
Usually the CNC is restored by closing the warning. If the error persists, contact your
supplier.
0003
'Error when requesting memory. Restart Windows & CNC'
DETECTION
During CNC startup.
CAUSE
The CNC does not have enough memory or the memory is too fragmented.
SOLUTION
Restart the unit and re-initiate the CNC. If the memory is too fragmented, when
starting the unit up and re-initiate the CNC, the error will disappear. If the error persists
after powering up several times, contact your supplier.
0004
'Checksum error in PLC data'
DETECTION
During CNC startup.
CAUSE
The PLC data related to marks, counters, timers and registers saved into a disk is
not valid. The plcdata.bin file that contains these data does not exist, is not accessible
or is corrupt.
CONSEQUENCE The PLC data related to marks, counters, timers and registers is lost.
SOLUTION
If the error persists after powering the CNC up several times, contact your supplier.
0005
'The CNC was not turned off properly, it must be homed'
DETECTION
During CNC startup.
CAUSE
The CNC data related to coordinates, zero offsets, etc. that are saved into the disk
is not valid. The orgdata.tab file that contains these data does not exist, is not
accessible or is corrupt.
CONSEQUENCE The CNC data related to coordinates, zero offsets, parts counter, kinematics, etc. are
lost.
SOLUTION
If the error persists after powering the CNC up several times, contact your supplier.
0006
'Preparation takes longer than half the cycle time.
DETECTION
On CNC startup or during execution.
CAUSE
Data preparation at the CNC per PLC cycle takes too long.
CONSEQUENCE The PREPFREQ parameter does not have the desired effect.
SOLUTION
Decrease the value of the PREPFREQ parameter of the channel.
0007
'To complete the reset, restart the CNC.
DETECTION
After a CNC reset.
CAUSE
The user has reset the CNC twice in a row and none of them has ended correctly.
SOLUTION
Restart the CNC. If the user presses the [RESET] key for the third time, the CNC
application shuts down.
Summary of Contents for 8065
Page 1: ...Ref 1709 8060 8065 CNC Error solving manual...
Page 4: ...BLANK PAGE 4...
Page 216: ...Error solving manual CNC 8060 CNC 8065 216 REF 1709...
Page 217: ...Error solving manual CNC 8060 CNC 8065 217 User notes REF 1709...
Page 218: ...Error solving manual CNC 8060 CNC 8065 218 User notes REF 1709...
Page 219: ...Error solving manual CNC 8060 CNC 8065 219 User notes REF 1709...