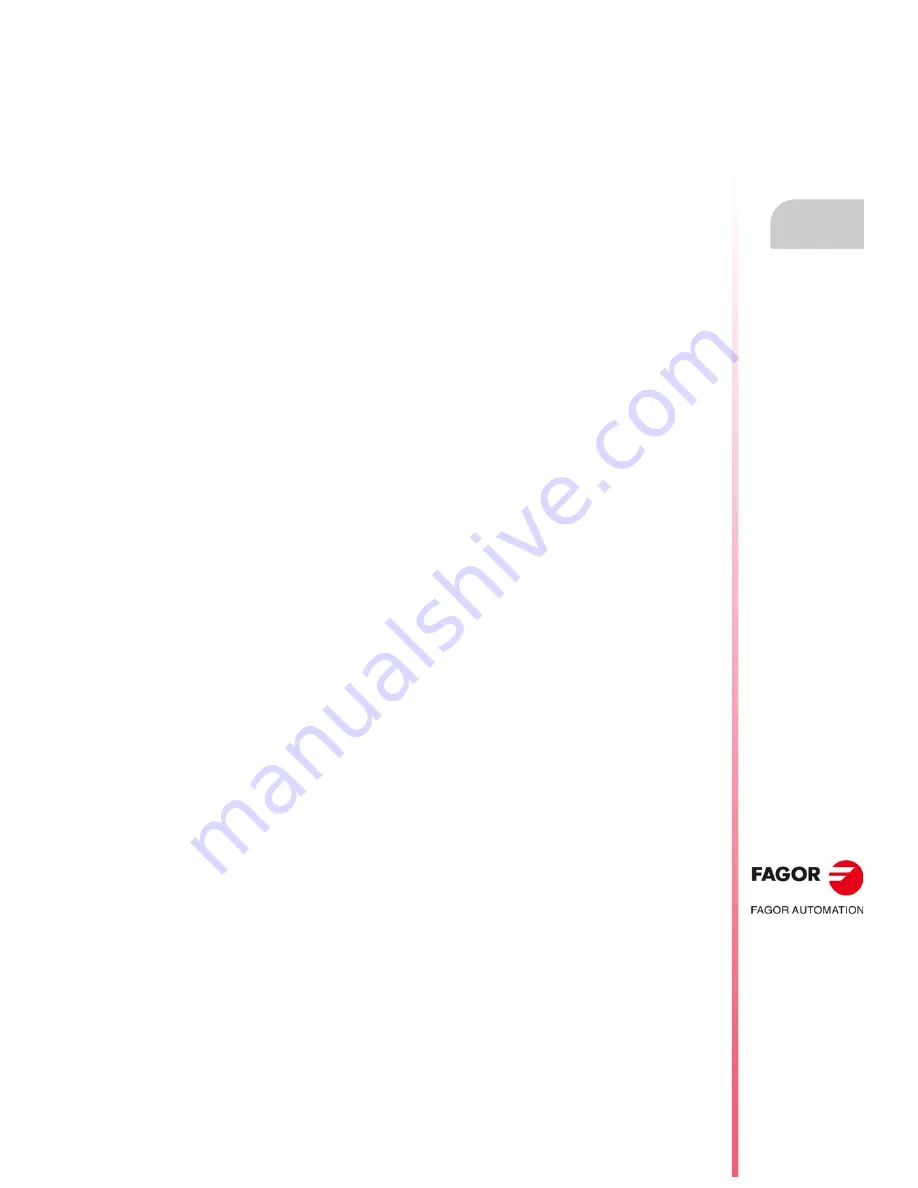
Error solving manual.
CNC 8060
CNC 8065
·97·
(R
EF
: 1709)
1921
'The programmed geometry is not an outside geometry'
DETECTION
During the execution of the cycle.
CAUSE
The geometry programmed in the canned cycle does not correspond to an external
geometry, as indicated in the cycle.
SOLUTION
Change the geometry or define it as internal geometry in the cycle.
1922
'The programmed geometry is not an inside geometry'
DETECTION
During the execution of the cycle.
CAUSE
The geometry programmed in the canned cycle does not correspond to an internal
geometry, as indicated in the cycle.
SOLUTION
Change the geometry or define it as external geometry in the cycle.
1923
'Wrong geometry'
DETECTION
During the execution of the cycle.
CAUSE
The geometry of the canned cycle is wrong.
SOLUTION
Correct the program.
1924
‘Insufficient memory’
DETECTION
During the execution of the cycle.
CAUSE
The system has not enough memory to continue resolving the pocket.
SOLUTION
Contact FAGOR.
1925
'Neither roughing nor finishing has been programmed'
DETECTION
During the execution of the cycle.
CAUSE
No operation has been defined in the canned cycle.
SOLUTION
The canned cycle must have the definition of the roughing or finishing operation. If
an operation does not have a tool, the cycle will not executed it; at least one operation
must have a tool.
1926
'Vertex programmed wrong'
DETECTION
During the execution of the cycle.
CAUSE
The geometry of the canned cycle is wrong.
SOLUTION
Correct the program.
1927
'Wrong cutter for programmed profile'
DETECTION
During the execution of the cycle.
CAUSE
The tool is not valid for the geometry of the programmed cycle.
SOLUTION
Select another tool.
1928
'Grooving pass greater than cutter width'
DETECTION
During the execution of the cycle.
CAUSE
The slot milling (grooving) pass is greater than cutter width.
SOLUTION
Program a grooving (slot milling) pass smaller or equal to the cutter width.
1929
'No spindle speed has been programmed'
DETECTION
During the execution of the cycle.
CAUSE
The spindle speed is 0.
SOLUTION
Define a feedrate higher than 0.
1930
'A zero drilling peck has been programmed'
DETECTION
During the execution of the cycle.
CAUSE
The value of the drilling peck is 0.
SOLUTION
Define a drilling peck other than 0.
1931
'No depth has been programmed'
DETECTION
During the execution of the cycle.
CAUSE
The machining depth is 0.
SOLUTION
Define a machining depth other than 0.
1932
'Spindle missing to execute the cycle'
DETECTION
During the execution of the cycle.
CAUSE
The channel that executes the cycle does not a spindle.
SOLUTION
Yield a spindle to the channel or execute the cycle in a channel with spindle.
Summary of Contents for 8065
Page 1: ...Ref 1709 8060 8065 CNC Error solving manual...
Page 4: ...BLANK PAGE 4...
Page 216: ...Error solving manual CNC 8060 CNC 8065 216 REF 1709...
Page 217: ...Error solving manual CNC 8060 CNC 8065 217 User notes REF 1709...
Page 218: ...Error solving manual CNC 8060 CNC 8065 218 User notes REF 1709...
Page 219: ...Error solving manual CNC 8060 CNC 8065 219 User notes REF 1709...