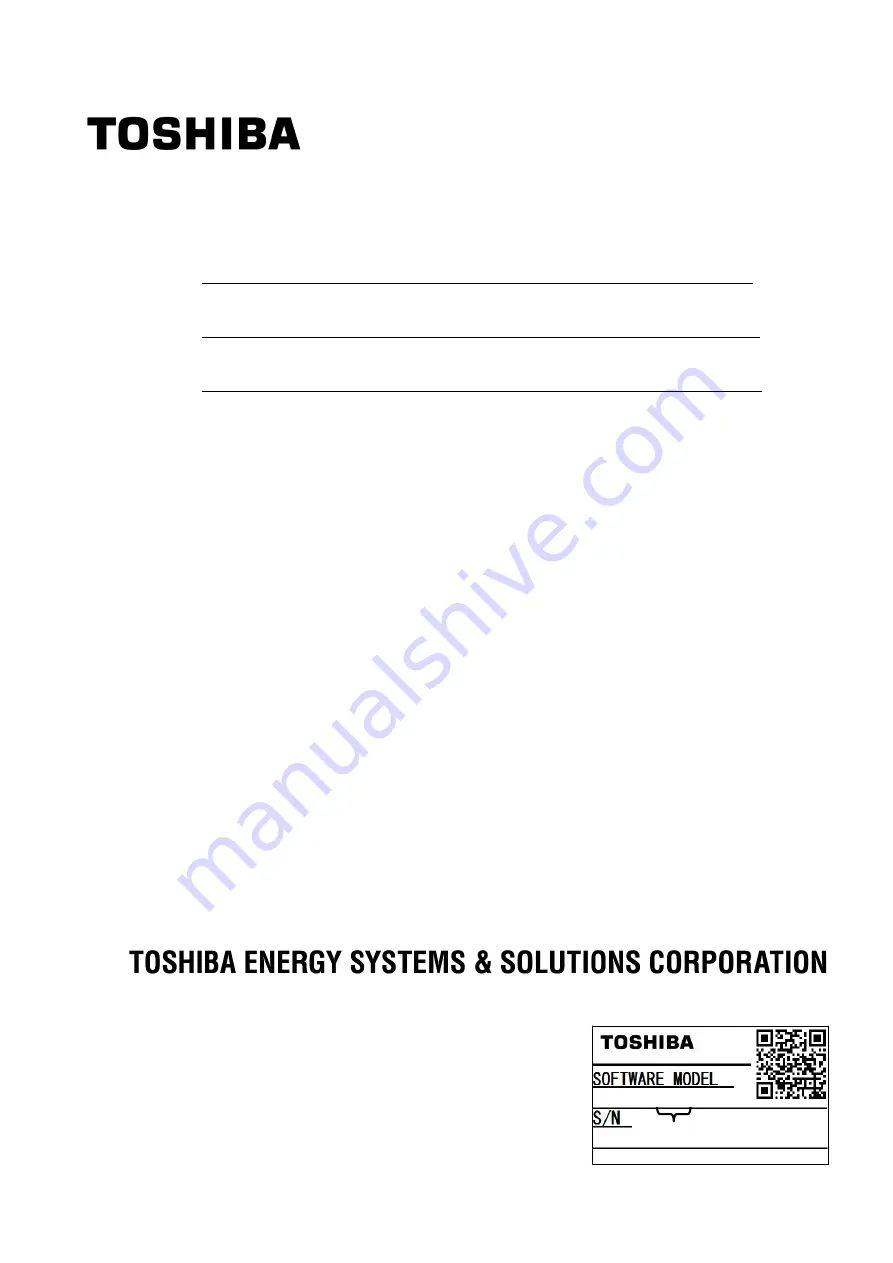
6F2S1915 (Rev. 0.46)
Notice: GRZ200 manual is issued for ‘031’ and ‘032’
software code, which you can identify at ’S, G, and
T positions’ on Software nameplate.
GRZ200-
-
-
S, G, and T positions
TOSHIBA ENERGY SYSTEMS & SOLUTIONS CORPORATION
Instruction manual
Distance Protection IED
GR200 series (GRZ200)
Summary of Contents for GR 200 Series
Page 1047: ...6F2S1915 0 46 GRZ200 Soft 031 032 1026 Figure 8 3 4 Screen shot from GR TIEMS ...
Page 1354: ...6F2S1915 0 46 GRZ200 Soft 031 032 1333 Appendix 1 Signal list for common function ...
Page 1410: ...6F2S1915 0 46 GRZ200 Soft 031 032 1389 This page is intentionally blank ...
Page 1480: ...6F2S1915 0 46 GRZ200 Soft 031 032 1459 Appendix 6 Ordering ...
Page 1497: ...6F2S1915 0 46 GRZ200 Soft 031 032 1476 Appendix 7 Technical data ...
Page 1518: ...6F2S1915 0 46 GRZ200 Soft 031 032 1497 Appendix 8 Manufacture setting ...
Page 1523: ...6F2S1915 0 46 GRZ200 Soft 031 032 1502 Appendix 10 CT requirement ...
Page 1531: ...6F2S1915 0 46 GRZ200 Soft 031 032 1510 Appendix 12 Engineering exercise ...
Page 1563: ......