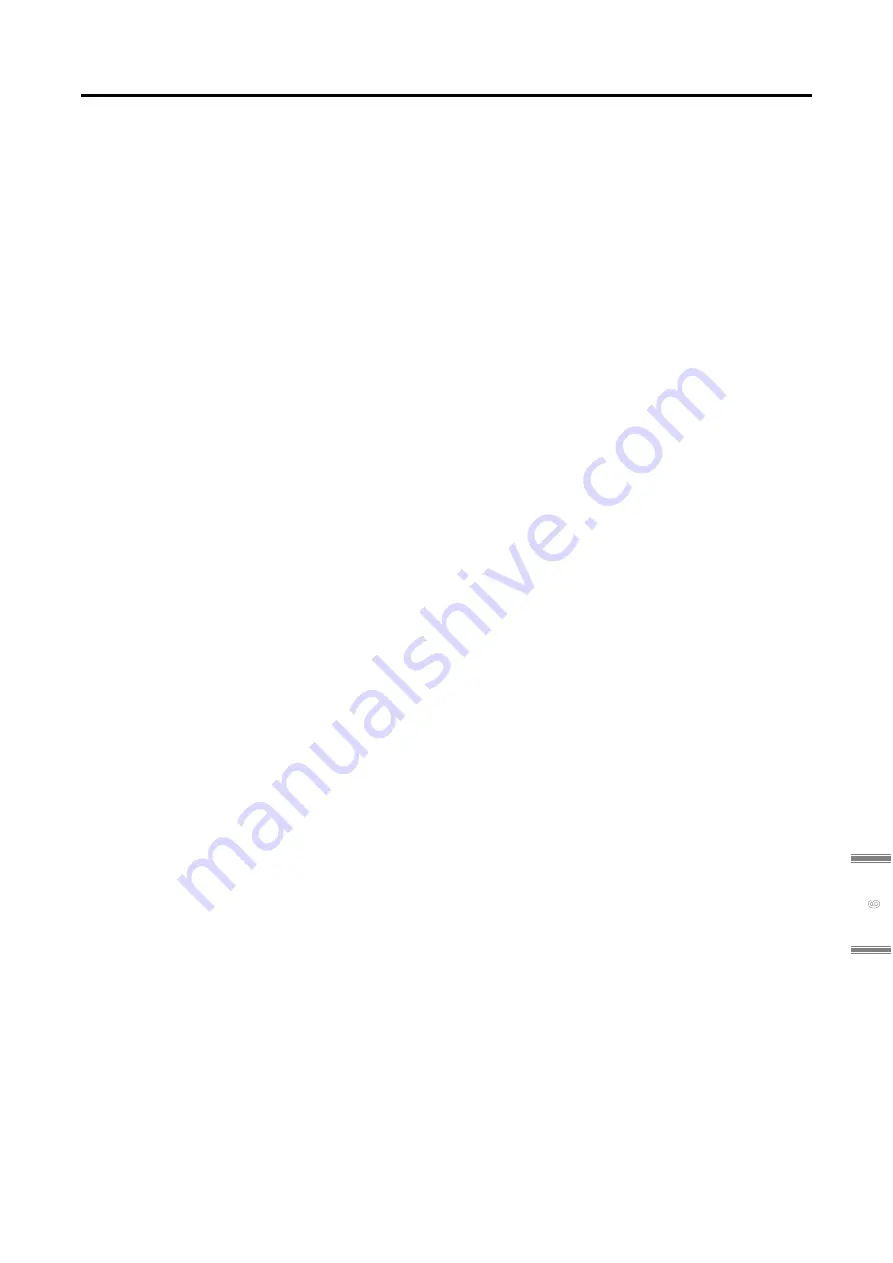
9.2.5 How to use
9-24
9
Dedic
ated func
tion
9.2.5 How to use
■
Tandem operation has the mutual compensating method and the Master-Slave method.
Mutual compensating method: This is the method that 2 axes are checking position
error each other and compensating difference, through local communication function
built in the servo amplifier. Use this method if same motion is required to both axes.
Master-Slave method: This is the method that one side (Slave) checks position
deviation with the other side (Master) and compensates difference. Use this method if a
follow-up motion against the Master axis is required to the Slave axis.
■
For the mutual compensating method
If rotation directions of 2 axes are same, set all parameters same in 2 axes.
If rotation directions of 2 axes are different, set "04: PC-_VC+_TC+" to Group8 ID00
"Position, Velocity, Torque Command Input Polarity", at one axis. And, set "01:
Reversed" to Group8 ID80 "Polarity selection of axes-sync compensation", at both axes.
For the other parameters, set same parameters, at both axes.
Recommends parameters below, at adjustment starting.
Axes-sync compensation proportional gain: 30%, Axes-sync compensation integral
time constant: 1000ms (equal to invalid), Axes-sync compensation filter: 0.0ms
Adjust the value of the axes-sync compensation proportional gain and the axes-sync
compensation filter for minimizing deviation, with checking the axes-sync error monitor.
Make tune of servo gain. See "6. Servo tuning" for tuning procedure. However, some of
functions are not able to use. See "9.2.7 Precautions" for the functions which are not
able to use.
■
For the Master-Slave method
When Master-Slave method is used, the axes-sync compensation function is set as
invalid at Master axis, and set as valid at Slave axis.
If rotation directions of 2 axes are same, set same parameter to Group8 ID00 "Position,
Velocity, Torque Command Input Polarity", in 2 axes. And, set " 00:Not_Reversed " to
Group8 ID80 "Polarity selection of axes-sync compensation", at Slave axis.
If rotation directions of 2 axes are different, set "04: PC-_VC+_TC+" to Group8 ID00
"Position, Velocity, Torque Command Input Polarity" and set " 01:Reversed " to Group1
ID83 "Polarity selection of axes-sync compensation", at Slave axis.
Set Master side parameters as below.
Axes-sync compensation proportional gain: 0% (equal to invalid), Axes-sync
compensation integral time constant: 1000ms (equal to invalid), Axes-sync
compensation filter: 0.0ms
Slave side parameters are recommended as below.
Axes-sync compensation proportional gain: 30%, Axes-sync compensation integral
time constant: 1000ms (equal to invalid), Axes-sync compensation filter: 0.0ms
Adjust the value of the axes-sync compensation proportional gain, the axes-sync
compensation integral time constant and the axes-sync compensation filter for
minimizing deviation, with checking the axes-sync error monitor.
Make tune of servo gain. See "6. Servo tuning" for tuning procedure. However, some of
functions are not able to use. See "9.2.7 Precautions" for the functions which are not
able to use.
Summary of Contents for Sanmotion R 3E S
Page 1: ...M0010630G For Rotary Motor Instruction Manual Analog Pulse Input Type ...
Page 2: ......
Page 76: ...No Text on This Page ...
Page 88: ...No Text on This Page ...
Page 266: ...No Text on This Page ...
Page 332: ...No Text on This Page ...
Page 408: ...No Text on This Page ...
Page 444: ...No Text on This Page ...
Page 511: ...12 7 Optional parts dimensions 12 65 12 Appendix REGIST 1000W Wiring diagram ...
Page 512: ...No Text on This Page ...